
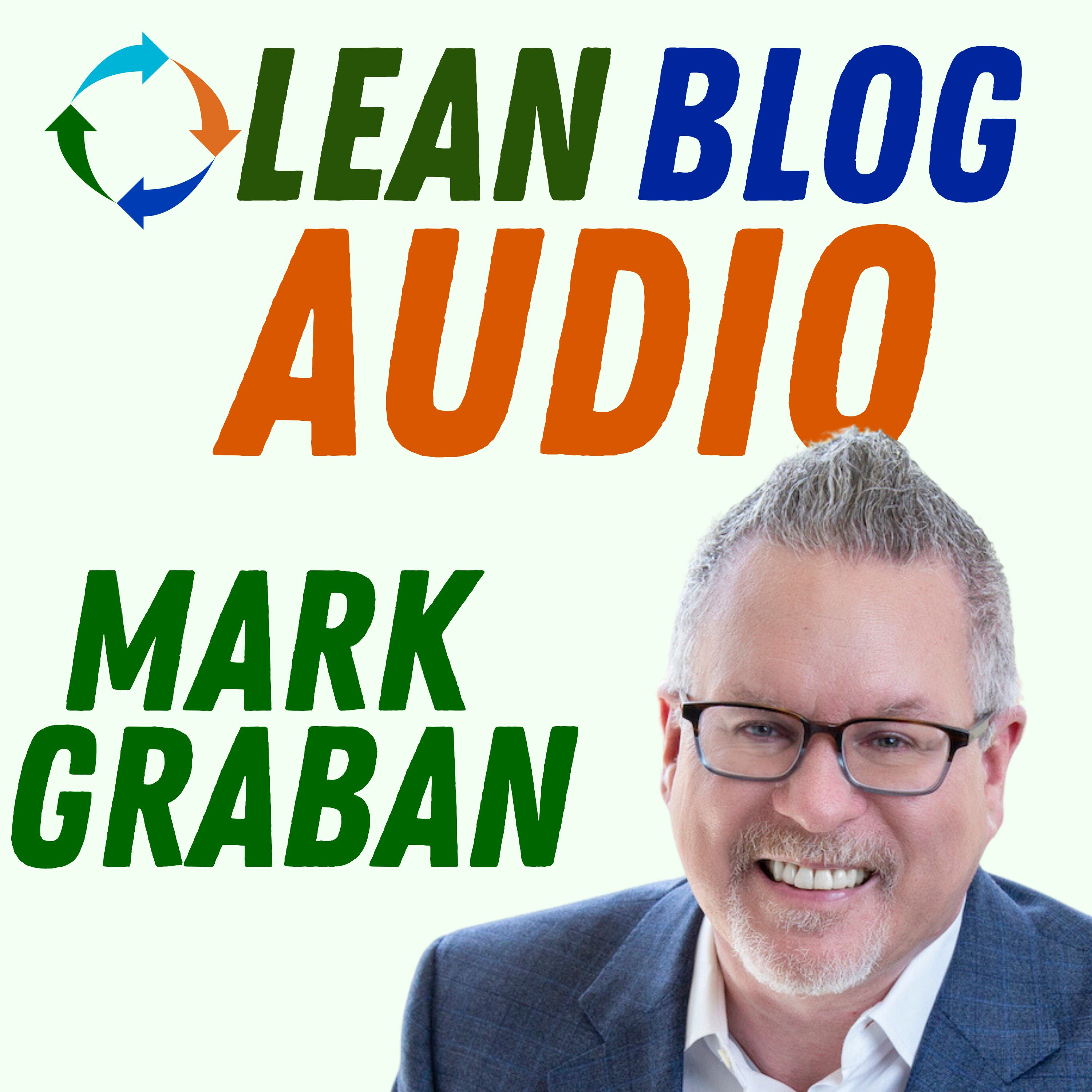
Lean Blog Audio
Mark Graban
Lean Blog Audio features Mark Graban reading and expanding on LeanBlog.org posts. Explore real-world lessons on Lean thinking, psychological safety, continuous improvement, and performance metrics like Process Behavior Charts. Learn how leaders in healthcare, manufacturing, and beyond create cultures of learning, reduce fear, and drive better results.
Listen and learn: leanblog.org/audio
Listen and learn: leanblog.org/audio
Episodes
Mentioned books

Feb 22, 2024 • 9min
Mistakes are Proof that You’re Trying? A Situational Analysis
Exploring the significance of mistakes in various environments and the valuable lessons they offer for growth and improvement. The podcast delves into error prevention in healthcare, with a focus on mistake-proofing methods to enhance patient safety. Emphasizing the need to differentiate between process and innovation mistakes, and the importance of learning from process mistakes for improvement.

Feb 16, 2024 • 11min
What Will a “Quality Stand Down” Day Accomplish at Boeing?
The blog post
What do Boeing frontline mechanics and engineers think about this day? What did they expect going into it? How did the day turn out? I'd love to know.
“Quality is made in the boardroom.”
I rolled my eyes hard when I read this announcement from Boeing, as part of the aftermath of the January 5th door plug blowout incident on an Alaska Airlines flight:
In recent years, there have been many complaints about the Boeing culture. Culture starts with the executive suite. They're responsible for the culture, and they're responsible for the results of bad decisions made in the boardroom or the remote C-suite. Or they should be responsible.
W. Edwards DemingBoeing to hold Quality Stand Downs

Feb 13, 2024 • 3min
Chef Gordon Ramsay on Never Making the Same Mistake Twice
Blog post link
I loved a recent New York Times article about Chef Gordon Ramsay, including this part:
“Ramsay said that when he makes a mistake, he owns up to it. He has been candid about the misjudgments that led to the closure of Amaryllis, his fine dining restaurant in Glasgow, and admits that he has opened restaurants that were “badly conceptualized” or opened in the wrong area. “You should never be embarrassed of failure,” he said. “But never make the same mistake twice.”

Feb 7, 2024 • 4min
Closing Boeing’s “Shadow Factory” is Harder Than it Sounds
Blog post
For a long time, I've heard the phrase “the hidden factory” used to describe various forms of waste in a factory, including rework operations and activity.
I was surprised to hear Boeing CEO Dave Calhoun refer to this in a news story using a similar phrase, “shadow factory.”
Boeing Wants to Close Its ‘Shadow Factories.' It Would Be a Positive Step.

Feb 5, 2024 • 6min
Lean Leadership in Action: CEO Larry Culp's Journey to Revitalize GE at the Gemba
Read the blog post
As I recently shared on LinkedIn, I really appreciated the annual shareholder letter that was published and shared by Larry Culp, who has been CEO of General Electric for just over five years now (the first-ever outsider CEO in their 125+ year history).
Read the full letter here. I've also archived it here as a PDF.
First off, I can't help but notice that the photo shared at the end of the letter is not a corporate headshot of Larry in a power suit and tie. It's a photo from a "gemba" (or factory floor) with him wearing safety glasses, a casual shirt, and a high-visibility vest.
He certainly looks to be in his element and enjoying it. How rare is that amongst CEOs of manufacturing companies of any size? How much better off would other manufacturers (or healthcare organizations) be if they had CEOs who don't just sponsor or support Lean, but are instead leading and driving the culture change? How many hospital CEOs truly enjoy donning PPE to be at the frontlines of patient care?

Jan 16, 2024 • 6min
Mastering Mistake-Proofing: Insights from Toyota's Poka Yoke Approach
Blog post
This post is built around excerpts from the book The Mistakes That Make Us: Cultivating a Culture of Learning and Innovation. Read more about Toyota, including stories and key lessons learned in the book.
Download a free preview of the book
From the book:
Fear and punishment drive people to get better at hiding mistakes when they could channel that energy into preventing them. When they can't be hidden, repeated mistakes illustrate how punishment accomplishes nothing beyond deflecting blame from leaders.
One of my heroes, W. Edwards Deming, who also deeply influenced Toyota executives, shared what may be the most important recommendation in his famed “14 Points for Management”:
“Drive out fear, so that everyone may work effectively for the company.”[i]
Driving out fear means, in part, that everyone can feel safe to speak up about mistakes and improvement ideas, as discussed in Chapters Five and Six. Leaders can also alleviate the fear of making mistakes, to begin with, when they combine the right methods and mindsets.
Starting with mindset, as former Toyota leader Darril Wilburn says,
“It's a leader's responsibility to create a system in which people can be successful.”
Therefore, it's the leader's responsibility to drive out fear. This includes creating work systems where it's easier to do the right thing and more difficult to make a mistake. This responsibility doesn't fall solely on the shoulders of leaders. They also engage their team members in designing effective mistake-proofing methods.
Mistake-proofing, or “poka yoke” in Japanese, is a core method within the Toyota Production System. It's a mindset based on the idea that people want to do good work but are imperfect. So, leaders have an obligation to help.
You might not think of Toyota as an entrepreneurial company today, but it started small in 1926 as a manufacturer of weaving looms based on patents held by founder Sakichi Toyoda. One of his key innovations was a mechanism that would automatically stop a loom when a thread broke, preventing it from cranking out more defective cloth. This innovation also led to huge productivity increases. One worker could now oversee upward of 30 to 50 machines, walking over to respond to problems when they were detected instead of having to hover over a single machine continually.
Toyota originally used the phrase “baka yoke,” which means “idiot-proofing.” Many decades ago, that term upset a Japanese factory worker who, correctly, complained that they weren't an idiot. We should also avoid saying “fool-proofing” or “dummy-proofing,” regardless of how often we hear them spoken around us.
Professor John Grout, the former dean of the Campbell School of Business at Berry College, is an expert on mistakes, receiving some of his early education in the field from Toyota leaders. He thinks mistake-proofing should be called “slip-proofing,” as it's easier to prevent execution errors than bad decisions (planning mistakes). One common slip is closing a file without saving it. The “Are you sure?” dialogue box tries to protect us, but as John points out, we're likely to click “Yes” out of habit. That's a slip on top of a slip–one that's hard to prevent. Using software that continually autosaves your work eliminates that risk (to my benefit, as I write this book in Google Docs).
This post originally appeared at mistakesbook.com.

Jan 13, 2024 • 8min
Psychological Safety in Manufacturing: How Silence in Aerospace Factories Can Turn Deadly
Blog post link
Psychological Safety is not some nice-to-have touchy-feely concept.
Psychological Safety means that you feel safe speaking up in the workplace. That could mean:
Asking questions
Pointing out problems
Admitting mistakes
Disagreeing with your manager
Sharing ideas for improvement
It's been pretty well proven that organizations with a higher level of Psychological Safety perform better.
A lack of Psychological Safety in a factory can turn deadly. A lack of it has proven deadly in healthcare settings too, of course.
If workers and engineers are punished for speaking up about quality problems in aerospace factories, that puts customers (and passengers) at great risk.
When people are pressured into being silent, that's a management problem and a culture problem. I'm not blaming the individuals who keep quiet to save their jobs. I do admire those who take great professional and personal risk to speak up anyway.
This WSJ article (which should be a free-reading link) talks at length about workers being punished at Spirit Aerosystems (a key Boeing supplier, formerly part of Boeing) for speaking up about quality concerns and problems.
There's so much to potentially dig into regarding decisions made by past Boeing executives about spinning off factories or outsourcing work. But I'll keep this post focused on the psychological safety elements.
I saw the punchline of this one story coming a mile away. It's not a funny situation, but I did literally laugh out loud:
“At one point, Dean said, [Spirit] threw a pizza party for employees to celebrate a drop in the number of defects reported. Chatter at the party turned to how everyone knew that the defect numbers were down only because people were reporting fewer problems.”
It's so predictable. It's happened before, and it will happen again.
Dr. Deming wrote about this dynamic 40 years ago, with a story of a factory that offered an incentive for “zero injuries.” Guess what, people stopped reporting injuries, even though people could be seen walking around with arms in slings and such.
Remember, including in healthcare, that “reported incidents” are not the same as “incidents,” especially when Psychological Safety is sorely lacking. In a true Lean Manufacturing environment, people are REWARDED for raising concerns and pointing out problems. We need more of that good Lean culture. Lives are at stake.
More from the WSJ article about people being punished for putting quality first:
The result, some current and former employees say: a factory where workers rush to meet unrealistic quotas and where pointing out problems is discouraged if not punished. Increasingly, they say, planes have been leaving Wichita with so-called escapements, or undetected defects.
“It is known at Spirit that if you make too much noise and cause too much trouble, you will be moved,” said Joshua Dean, a former Spirit quality auditor who says he was fired after flagging misdrilled holes in fuselages. “It doesn't mean you completely disregard stuff, but they don't want you to find everything and write it up.”
And also:
On the Spirit factory floor, some machinists building planes say their concerns about quality rarely get conveyed to more senior managers, and that quality inspectors fear retaliation if they point out too many problems.
Union representatives complained to leaders last fall that the company removed inspectors from line jobs and replaced them with contract workers after they flagged multiple defects. “This is leaving them with great quality and safety concerns,” one of the representatives wrote in an email to union officials. “Also feeling retaliated against for doing their jobs.”
That doesn't give me more confidence about flying on Boeing airplanes. I hope the culture at Airbus isn't as dysfunctional.
‘This Has Been Going on for Years.' Inside Boeing's Manufacturing Mess.

Nov 28, 2023 • 6min
Congrats to Four Podcast Guests Who Were Named to the “Thinkers50” List
Blog post with more info and links
Congratulations to my podcast(s) guests who were named to the Thinkers50 list of influential management thinkers!
I am thrilled to extend my heartiest congratulations to a remarkable group of individuals who have recently graced the stages of my podcasts, “Lean Blog Interviews” and “My Favorite Mistake.” These brilliant minds have been recognized on the prestigious Thinkers50 list for their groundbreaking contributions to the field of management thinking. Each has shared their invaluable insights with us, and it's a true honor to see them receive this well-deserved accolade.⭐ Amy Edmondson (both podcasts)⭐ Erica Dhawan (MFM)⭐ Daniel Pink (both podcasts)⭐ Zeynep Ton (Lean podcast, twice)

Nov 27, 2023 • 1min
Cyber Monday / Week Deal: “Measures of Success” Signed Copies
Blog post with link to purchase and more
I have a limited number of copies of my book Measures of Success: React Less, Lead Better, Improve More that are available for about half of the Amazon retail price — and this includes free shipping.

Nov 16, 2023 • 9min
World Kindness Day, The Mistakes That Make Us, and Help From Karyn Ross
Blog post
tl;dr summary: Karyn Ross enlightened me about World Kindness Day and provided invaluable feedback on my book, The Mistakes That Make Us. Her insights particularly helped me replace the term “grace” with “kindness,” enhancing the book's inclusivity. She also helped me better distinguish between being “nice” and “kind.”