
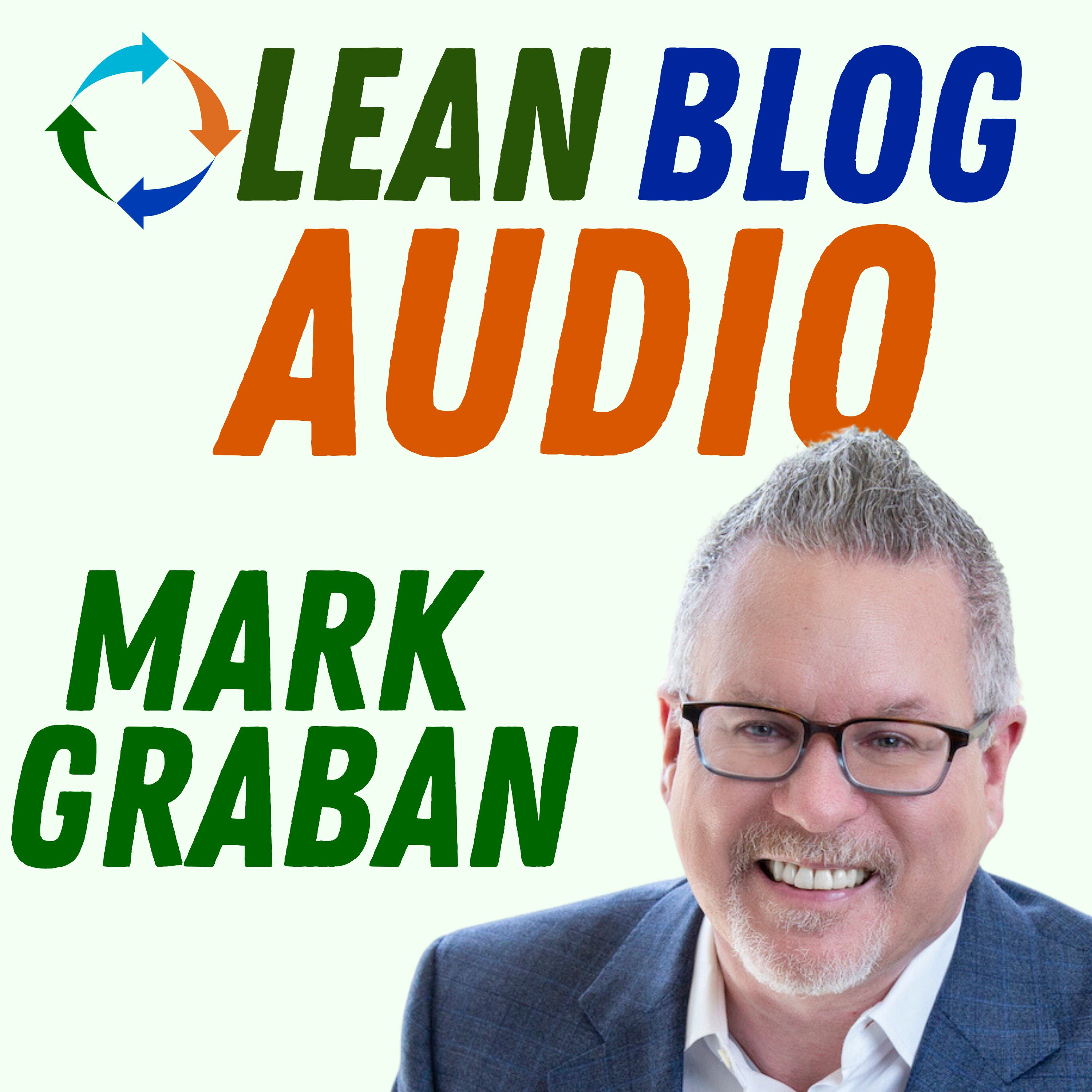
Lean Blog Audio
Mark Graban
Lean Blog Audio features Mark Graban reading and expanding on LeanBlog.org posts. Explore real-world lessons on Lean thinking, psychological safety, continuous improvement, and performance metrics like Process Behavior Charts. Learn how leaders in healthcare, manufacturing, and beyond create cultures of learning, reduce fear, and drive better results.
Listen and learn: leanblog.org/audio
Listen and learn: leanblog.org/audio
Episodes
Mentioned books

Apr 17, 2024 • 10min
Embracing Challenges for Success: Lessons in Toyota Culture and Kaizen from Nate Furuta
Read the blog post
I have been really enjoying this book, released in 2021, by Kiyoshi “Nate” Furuta, a retired Toyota executive: Welcome Problems, Find Success: Creating Toyota Cultures Around the World. I bought it a year ago and wish I had started reading it sooner!
Furuta is the retired former chair and CEO of Toyota Boshoku America, Inc. — an automotive parts supplier to companies including Toyota and General Motors.

Apr 11, 2024 • 6min
GE Aerospace CEO Larry Culp on a Finger-Pointing Culture and a Better Alternative
Read the episode, view video, and more
There was a fascinating article in Bloomberg BusinessWeek about GE doing its final spinoff of GE Vernova (ticker symbol: GEV) and the remaining business that Larry Culp remains CEO of, GE Aerospace (formerly GE Aviation, ticker symbol: GE).
The inside story of how GE CEO Larry Culp dismantled a 131-year-old American giant.
AN EMPIRE DIVIDED

Apr 4, 2024 • 6min
Turning Bad News into Building Blocks: Cultivating a Culture Where Mistakes Fuel Growth (Larry Culp and GE)
The blog post and video
Embracing Imperfections and Learning from Mistakes: A Leadership Insight from the 2022 AME Annual Conference...
In a riveting conversation between Larry Culp (at the time, CEO of GE and now CEO of GE Aerospace) and my good friend Katie Anderson at the 2022 Association for Manufacturing Excellence (AME) Annual Conference, valuable lessons on leadership, transparency, and fostering a culture where challenges and imperfections are openly shared were illuminated.
Come join AME at their 2024 Conference in Atlanta later this year.
Here's a short clip:

Mar 19, 2024 • 17min
The Problem (737 MAX and Beyond) at Boeing Isn't "Idiots." It's Far More Complex Than That... But Fixable
The blog post
As we sit in seat 26A, mindlessly watching a movie, we take for granted that our cell phone (or the shirt off our back) won't be suddenly sucked out through a gaping hole in the side of a plane. That's because the odds of this happening are unimaginably low. Until now, that is. Are we entering a new era where shoddy manufacturing (or maintenance) exposes us to more risk, reversing a decades-old trend of greatly improved aviation safety?
On January 5th, an Alaska Airlines 737 MAX-9, designed and assembled by Boeing, safely executed an emergency landing after a “door plug” blew out of the plane's left side. Thankfully, the resulting hole and loss of pressure didn't suck out any passengers or crew.
Now, the window and middle seats next to the door plug were thankfully empty. That raises questions about what Alaska knew and what chances they were taking by continuing to fly the plane after previous complaints about “whistling sound” and alerts about cabin pressures on previous flights that plane took.
The crew performed valiantly in these circumstances, and we should celebrate them. This incident creates an opportunity for the aviation industry (including regulators) to learn how to ensure this sort of door plug failure never happens again.
Instead of blaming human error, people should ask why the company didn't have better systems to prevent or detect the mistake or mistakes that led to this incident. Some leaders throw up their hands and lament,
“It's human error… we'll never be perfect… so what can we do?”
Instead of leaving that as an unanswered rhetorical question, we need to work at it seriously. What can we do to prevent mistakes and protect ourselves from human error?

Mar 7, 2024 • 8min
Cultivating a Culture of Candor: Transforming Workplace Communication for Better Outcomes
Explore the importance of creating a culture of candor and vulnerability in the workplace, where employees feel safe to express themselves without fear of consequences. Learn from experts like Timothy R. Clark and Amy Edmondson about the value of fostering vulnerability, rewarding candor, and cultivating psychological safety for improved workplace performance.

Mar 5, 2024 • 4min
A Better Question Than "Do You Have Any Questions?"
The blog post
Recently, I've heard an idea a few times that I'd like to share and discuss in this post. As I'm writing this, I can't remember who to cite. That's my mistake. I'll happily correct the post if I remember or somebody lets me know who to credit. Because I love this idea... but it's not my idea.
It's pretty common for a speaker to ask the audience, at the end of a talk:
"Do you have any questions?"
I'm quite certain I've done that. Sometimes, the answer is yes. But the framing of the question is closed-ended. And the question, whether at a talk or during a meeting, might be intimidating. People might wonder, "Is it OK to have questions? Should I be embarrassed if there was something I didn't quite understand?"
That's why it seems a better question is the open-ended version of that:
"What questions do you have?"

Mar 4, 2024 • 8min
Instead of Urging Your Employees to Be Brave, Help Them Feel Safe Speaking Up
The blog post
It’s 9 p.m. in an operating room, just before the last procedure of a long day that had been full of delays. A nurse sees that the surgeon is about to make an incision without first stopping for the expected “timeout,” a crucial step that helps the team confirm, among other things, that the correct surgery is about to be performed on the correct side of the correct patient. The nurse is also concerned they don’t have enough units of blood on hand for this type of procedure.
The nurse pauses and wonders,
“Should I speak up or keep quiet?”

5 snips
Mar 1, 2024 • 8min
Shigeo Shingo & Norman Bodek on Learning From Mistakes, Including Shingo’s
Exploring the philosophy of learning from mistakes using Shingo and Bodek's insights. Emphasizing process improvement and mistake-proofing for zero defects. Evolution from fool-proofing to mistake-proofing in manufacturing.

Feb 29, 2024 • 7min
ChatGPT Summarizes the Chapters in My Book, Measures of Success
The podcast discusses the process of using Chat GPT to summarize the book 'Measures of Success', focusing on the benefits for marketing and concerns about public access. It explores key concepts in organizational metrics, process behavior charts, data variation types, process improvement connections, and practical application of data analysis techniques with real-world examples.

Feb 26, 2024 • 10min
Come to Japan With Me and Katie Anderson in November to Study Lean!
I'm excited to announce that I've registered for Katie Anderson‘s Japan Study Trip in November! Read the blog post.Between 2012 and 2019, I visited Japan five times, and I learned something new each time. I've been really itching to go back. I'm excited to see and learn new things with Katie and her team!!It's a great opportunity to deepen your understanding of Lean and the Toyota Production System. Visiting Japan helps one understand which of the broader cultural elements of the country contribute to a Lean workplace.But it also helps you understand that not all Japanese companies are made in the Toyota mold. Toyota has worked very diligently to cultivate its culture and practices over time. And our organizations can do the same.