
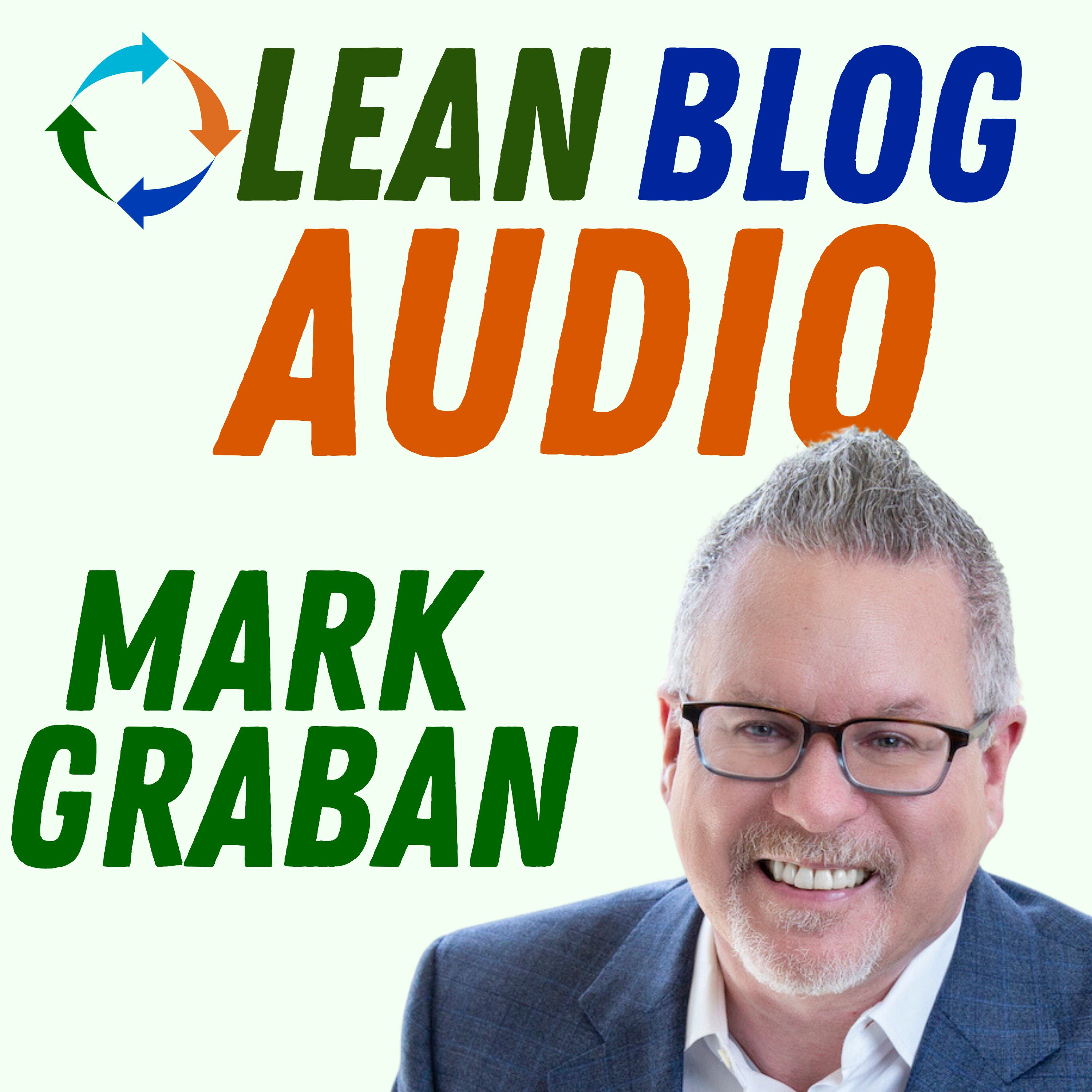
Lean Blog Audio
Mark Graban
Lean Blog Audio features Mark Graban reading and expanding on LeanBlog.org posts. Explore real-world lessons on Lean thinking, psychological safety, continuous improvement, and performance metrics like Process Behavior Charts. Learn how leaders in healthcare, manufacturing, and beyond create cultures of learning, reduce fear, and drive better results.
Listen and learn: leanblog.org/audio
Listen and learn: leanblog.org/audio
Episodes
Mentioned books

Jun 28, 2024 • 3min
Don't Digitize the Suggestion Box -- Improve a Better Way with Kaizen and KaiNexus
The blog post
Digital transformation is about rethinking and reinventing with digital tools. For over 13 years, KaiNexus has moved beyond the outdated suggestion box model.
Traditional suggestion boxes, whether paper or digital, often fail (or usually fail!–ideas get locked away, reviewed by a select few, and lead to frustration.
We believe in dynamic platforms that foster real-time communication and collaboration.
Don't digitize the old, broken way of doing things!
Mark Graban:Don't digitize the old broken process. Whether that's a suggestion box or anything else, digital transformation is about rethinking reinventing the way we do things with digital tools. From the beginning, more than 13 years ago, KaiNexus has never been an electronic suggestion box because suggestion boxes don't work, whether it's in paper form or an online digital form. Why is that? Suggestion boxes in the paper model have a locked box.
Ideas sit. Some special person with a key opens up box maybe once a month, maybe once a quarter. Some far off team talks about those suggestions without coming back to talk to the person who filled out that suggestion box slip. People give up on suggestion boxes, and it's understandable. So we don't want an electronic or a digital version of that.
What we do want is a digital process with proven, continuous improvement methods. We often refer to this as Kaizen, engaging people in opportunity identification, not just jumping to solutions but bringing forward a problem so we can talk about it locally and then escalate it to management by exception. Don't digitize the old, broken way of doing things.

Jun 26, 2024 • 4min
Psychological Safety: Ensuring Every Voice is Heard, Not Necessarily Followed
Blog post
Psychological Safety means everybody gets their say, but it doesn't mean you get your way.
Psychological Safety is an individual's belief, feeling, or perception that it's safe for them to speak up in a situation.
When people are rewarded for speaking candidly, that leads to rigorous debate and better decisions.
Psychological Safety doesn't mean freedom from being challenged or disagreed with.
It doesn't turn the workplace into a democracy and it doesn't mean you need 100% agreement to move forward on anything.
Psychological Safety means you can disagree with your manager or a peer… and they have the safety to disagree in return.
Psychological Safety doesn't mean shutting down a discussion because you feel uncomfortable.
What practices and behaviors have you seen in a workplace that cultivate Psychological Safety? What are some examples of rewarding people for speaking up candidly?
To me, it comes down to three high-level countermeasures for leaders:
Modeling candor, vulnerability, and the behaviors you want to see
Encouraging candor
Rewarding candor
In summary, Psychological Safety is the foundation of a healthy and productive workplace. It ensures that everyone has the opportunity to voice their thoughts and concerns without fear of retribution, even if it doesn't always mean getting their way.
Again, Psychological Safety means everybody gets their say, but it doesn't mean you get your way.
When leaders model, encourage, and reward candor, it fosters an environment where rigorous debate leads to better decision-making and continuous improvement. By adopting practices that promote Psychological Safety, such as open communication, constructive feedback, and a growth mindset, organizations can unlock the full potential of their teams.
If you're looking to cultivate Psychological Safety within your organization and drive better outcomes through open and candid dialogue, I can help. With extensive experience in fostering cultures of learning and innovation, I offer consulting, workshops, and coaching tailored to your specific needs.
Contact me today to learn how we can work together to build a safer, more effective workplace. I'm happy to do a free discovery call with you.
Or check out my book, The Mistakes That Make Us: Cultivating a Culture of Learning and Innovation. Or do both :-)

Jun 25, 2024 • 2min
Join Me on Friday for The Mistakes That Make Us: A Book Birthday Event
The blog post
The LinkedIn event
My latest book, The Mistakes That Make Us: Cultivating a Culture of Learning and Innovation, is turning one year old!
Join me, along with my co-host Elisabeth Swan, for what we hope will be an engaging, insightful, and fun discussion about learning from mistakes. We'll be joined by special surprise guests who will share their unique perspectives and experiences. This isn't just a one-way broadcast–it's an interactive session where we'll conduct live polls and open the virtual floor to your questions, ensuring a dynamic and participative environment.
View this page and click “Attend” to be reminded of this when it starts. A recording will also be available on LinkedIn and my YouTube channel.
Mistakes are a universal experience, and what truly matters is how we learn from them. Together, we will explore ways to improve our ability to learn from mistakes, both as individuals and as organizations. My goal is to uncover practical strategies that can be applied in various contexts to foster a culture of continuous learning and improvement.
We also have a special reason to celebrate. The Mistakes That Make Us is marking its first anniversary/birthday on June 30th. However, since that falls on a Sunday, and let's face it, who wants to be on LinkedIn on a Sunday? I've decided to move the celebration to Friday, June 28th. This will give us the perfect opportunity to not only discuss the themes of the book but also to celebrate its impact over the past year.

Jun 21, 2024 • 2min
Join Me at the Michigan Lean Consortium Annual Conference in August!
The Blog Post
I'm excited to share my breakout session at the Michigan Lean Consortium Annual Conference!
In this session, I dive into the critical role of Psychological Safety as a Foundation for Continuous Improvement.
We explore how fostering an environment where team members feel safe to share ideas, take risks, and learn from mistakes can drive remarkable progress and innovation.
Oh, and did I mention that Traverse City is usually gorgeous in August?

Jun 20, 2024 • 6min
Mistakes and Errors: A Circular Definition; Leadership Matters
Blog post link
When writing or speaking, I use the words “mistake” and “error” interchangeably. The definitions in some dictionaries are comically circular.
Dictionary.com defines an error as:
“a deviation from accuracy or correctness; a MISTAKE, as in action or speech.”
It also defines a mistake as:
“an ERROR in action, calculation, opinion, or judgment caused by poor reasoning, carelessness, insufficient knowledge, etc.”
So, a mistake is an error, and an error is a mistake.

Jun 16, 2024 • 11min
Upcoming Shingo Webinar on Learning From Mistakes and Psychological Safety
Blog post link
I'm excited that the Shingo Institute asked me to present a webinar on June 18th.
Click here to register for the webinar
They've also published an article that I wrote:
Psychological Safety: The Key to Effective Andon Cord Pulls and Continuous Improvement
The webinar description:
Join us for an engaging webinar as we explore the transformative power of cultivating a culture that learns from mistakes, ultimately driving continuous improvement and innovation, leading to greater success! Renowned author Mark Graban will draw upon examples from a diverse array of companies, including industry titans like Toyota and agile software startups such as KaiNexus.
During this session, participants will gain valuable insights into the experiences of CEOs and other leaders, regardless of company size, who have adeptly turned mistakes into opportunities for growth and advancement. While these leaders remain vigilant in error prevention, they recognize the profound value of embracing mistakes as pivotal learning moments, particularly within environments fostering psychological safety and robust problem-solving capabilities.
Through compelling narratives, attendees will discover lessons that both educate and inspire, recognizing that in the dynamic landscape of business, mistakes are inevitable — yet it is the process of learning from them that propels us forward!

Jun 15, 2024 • 5min
The Pitfalls of Safety Bonuses in Lean Factories: A True Story
Blog post
I was talking recently with a trusted friend in the Lean community. He told me a story. It's certainly believable, even if it's second or third-hand to me.
He had no reason to make up a story like this.
A relative of his works in a U.S. factory. Yes, we still have factories here.
I'll call this relative of my friend “Guy,” which is pronounced the American way, not the French way.
Guy's factory would claim to use Lean methods and might even claim a “Toyota Production System” label as its inspiration.

Jun 14, 2024 • 5min
Psychological Safety vs. Psychological Comfort: Understanding the Distinction
Blog post link
The Big Picture: In the Lean community and beyond, some people mistakenly equate “psychological safety” with being comfortable all the time. This misconception can undermine the true essence of psychological safety in the workplace.
Psychological safety is not about constant comfort or shielding managers from discomfort. Synthesizing a few definitions of psychological safety, I say it's a person's belief, feeling, or perception that it's safe enough to speak candidly about things including:
Mistakes
Problems
Ideas
Differing views
without fearing marginalization or punishment.
What Psychological Safety Really Means

Jun 6, 2024 • 3min
Preventing Surgical Errors: Effective Strategies Over Warning Signs in Operating Rooms
The blog post
IMAGE: A sign that reads "CAUTION: DON'T OPERATE ON THE WRONG SIDE"
It's silly, right? I've never seen a sign like this in an operating room. And I'm not advocating for them. It's not the right approach for quality and patient safety.
If warning signs actually prevented mistakes, and given that a vast majority of mistakes are caused by human factors (like fatigue) and systemic factors (like being behind schedule because instruments were delivered late to the O.R.)…1) A sign like this would be posted in every operating room
and2) Wrong-site, wrong-side, and wrong-patient surgeries would never occurBut, of course, it's not that simple.What works?Mistake-proofing works.

Jun 4, 2024 • 6min
Celebrating 100 Years of Shewhart’s Control Charts: A Century of Quality Management
The blog post
TODAY marks the centennial of one of the most significant innovations in quality management: the control chart. 🎂 🎉 🎆
In the early 1920s, Walter A. Shewhart, working at Bell Labs, recognized the need for a statistical method to monitor and control manufacturing processes.
On May 16, 1924, Shewhart created the first “control chart,” a tool that distinguished between common cause variation (inherent in the process) and special cause variation (due to specific, identifiable factors). This simple yet powerful distinction laid the foundation for modern statistical process control (SPC). Control charts were dubbed “Process Behavior Charts” by Donald J. Wheeler Ph.D.)
The latest and greatest of the control charts is the “XmR Chart” — as Wheeler wrote about in Understanding Variation and I wrote about in Measures of Success (a book that has a foreword written by Wheeler).