
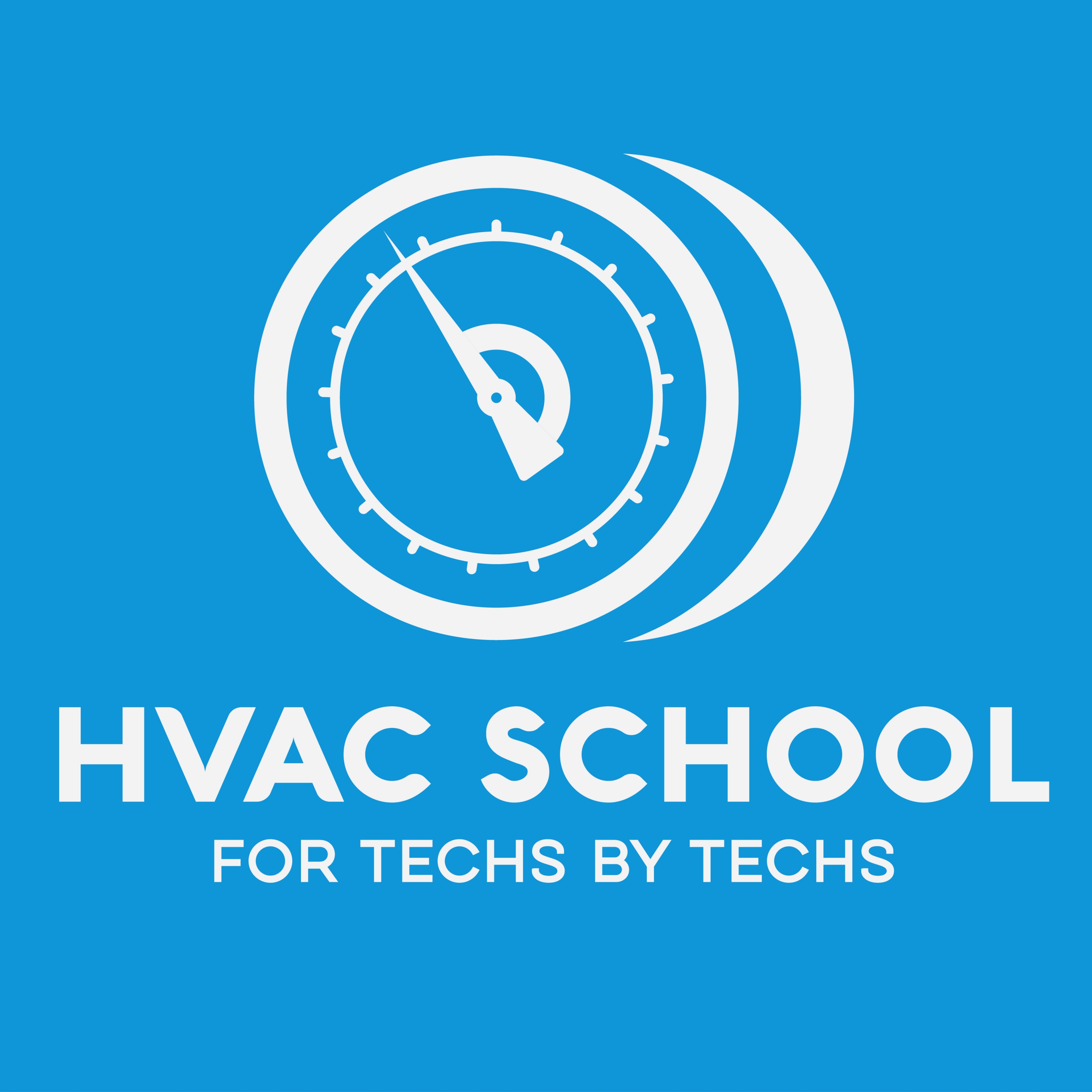
HVAC School - For Techs, By Techs
Bryan Orr
Real training for HVAC ( Heating, Ventilation, Air Conditioning and Refrigeration) Technicians. Including recorded tech training, interviews, diagnostics and general conversations about the trade.
Episodes
Mentioned books

Nov 12, 2020 • 45min
Changing Refrigerant Regulations w/ Bluon
In this episode, Bryan talks with Peter Capuciati and Bryan Johnson from Bluon. They discuss how refrigerant regulations keep changing and how technicians can make sense of it. We've begun phasing out R-22; the refrigerant can no longer be imported or manufactured in the United States. We can still recover and reclaim R-22, but the recovered refrigerant on the market can't meet the usual demand. R-22 went through a phaseout because of its ODP; R-410A has 0 ODP and was the main replacement. However, refrigerant regulations are still changing, as R-410A will soon be ready for a phase-down due to its high GWP. There are two main replacement options for R-410A: R-454B and R-32 (A2L refrigerants). There is also R-466A, but it cuts out even earlier than R-410A on high-pressure and has worse heat transfer capabilities. Right now, R-32 is perhaps the best refrigerant (beside ammonia, which is toxic), and it's even an ingredient in the R-410A blend. However, HVAC technicians and customers alike are apprehensive about the flammability. Although these regulations can be confusing and frustrating, the Bluon team recommends holding off from making capital decisions. While regulations are changing, it may not be a good idea to make a definitive equipment swap without knowing the final rulings. As a technician, it's good to benchmark the equipment. If you need to convert equipment, make sure to tune it to the specific refrigerant that's going in. Peter and the Bryans also discuss: Ozone-depleting potential (ODP) vs. global warming potential (GWP) Equipment efficiency and its effect on GWP R-32 and flammability risk aversion AR5 vs. AR4 Refrigerant blends as replacements Converting various equipment designs Benchmarking Bluon support and training Check out more information about Bluon HERE. Learn more about Refrigeration Technologies HERE. If you have an iPhone, subscribe to the podcast HERE, and if you have an Android phone, subscribe HERE.

Nov 10, 2020 • 9min
Single Phase v Two Phase Refrigeration - Short 101
In this short podcast episode, Bryan talks about the differences between single-phase and two-phase refrigeration. This particular episode is about the fundamentals of physics, chemistry, and science in general. When we talk about phases, we're referring to the changes in the states of matter. We typically think of the states of matter as solid, liquid, and gas. In refrigeration systems, the refrigerant usually changes from a liquid to a vapor in the evaporator and then from a vapor to a liquid in the condenser; that is an example of two-phase refrigeration. We get two-phase refrigeration anytime we're changing the state of matter in order to accomplish refrigeration. When you change the state of matter, you transfer a lot more heat than with a single-phase system. You get more heat in and out between phases due to latent. Between a solid and a liquid, the energy that goes towards the phase change is the latent heat of fusion. Between a liquid and a gas, the energy that goes into the phase change is the latent heat of vaporization. It takes a lot more heat to condense or boil water than it does to change its temperature by one degree, so we take advantage of that capacity to absorb heat into the boiling refrigerant. There are also forms of single-phase refrigeration, including John Gorrie's open-refrigeration machine. Gorrie's machine was just compressing and decompressing air; it was not changing the state of the air. In single-phase refrigeration, we can't make use of the extra energy from changing states. In those cases, condensers would be gas coolers. However, when you think about it, the process of refrigerating the space is a form of single-phase refrigeration; we don't change the phase of the air. So, we merely use two-phase refrigeration to drive single-phase refrigeration. Learn more about Refrigeration Technologies HERE. If you have an iPhone, subscribe to the podcast HERE, and if you have an Android phone, subscribe HERE.

Nov 5, 2020 • 33min
Floating Head Strategies

Oct 29, 2020 • 37min
CO2 Architecture
Don Gillis joins us again to talk more about common types of CO2 systems and how they differ

Oct 27, 2020 • 55min
Heat Pumps in Cold Climates
In this episode, we are joined by three people who know a lot about heat pumps and cold weather. We also cover everything from the way technologies have changed, some of the pitfalls to keep away from, and why heat pumps work even in really cold climates nowadays. Chad Gillespie: Chad is a senior manager, part of Mitsubishi Electric’s Performance Construction Team. He currently leads a national team of business development managers tasked with growing the new construction market for high-performance heat pumps. He has also worked in the construction industry for 26 years and has been with Mitsubishi Electric for 9. Dana Fischer: Dana is a residential area manager at Mitsubishi Electric. He supports and promotes the installation of high-performance, ductless heat pumps in homes across Maine and New Hampshire. Prior to his work at Mitsubishi Electric, he was a program manager for the Efficiency Maine Trust. Scott Libby: Scott is the owner of Royal River Heat Pumps. He has over 35 years of experience and training in the residential HVAC industry. His team sells Mitsubishi Electric exclusively; they are one of the largest heat-pump-only contractors in the country. Heat pumps are becoming more effective and comfortable, so they are now more appealing for cold climates. Although we previously relied on gas and oil in colder climates, we have seen people using heat pumps with success in New England and even Norway. We partially have R-410A and high-speed compressors to thank for those technological advancements to heat pumps. Chad, Dana, Scott, and Bryan also discuss: Offsetting fossil fuel usage Compressor advancements Heat pump performance during the polar vortex Leaky vs. tight buildings Load calculations and equipment selection Seasonal loads Single-zone vs. multi-zone heat pumps Design software Flaring tools Triple evacuation Responsible refrigerant handling Auxiliary heat Mitsubishi Kumo station Learn more about Refrigeration Technologies HERE. If you have an iPhone, subscribe to the podcast HERE, and if you have an Android phone, subscribe HERE.

Oct 22, 2020 • 46min
Demand Cooling + Liquid and Vapor Injection
Trevor Matthews is back and dropping more compressor knowledge on us. This time, he talks about demand cooling and liquid and vapor injection. In low-temperature applications, the discharge temperature would get very high and lead to oil breakdown and thermal overload, so demand cooling is a means of cooling the compressor. Demand cooling injects saturated refrigerant into the compressor body to cool it down. You're not jamming liquid into the compressor; the refrigerant flashes, which achieves a cooling effect. A demand cooling system consists of a module, temperature probe, liquid line solenoid valve, and injection valve. On the Discus compressors, the sensor will go in the port in the compressor head. When installing these, it is important to make sure high-quality goes to the valve. It's normal to have some frost at the outlet during operation; look for frost to make sure the demand cooling system is working properly. Scroll compressors use liquid and vapor injection almost exclusively nowadays. However, there is a difference between liquid and vapor injection for scroll compressors. A liquid injection system helps the compressor avoid high discharge temperatures (and high compression ratios). The vapor injection improves capacity and efficiency. When troubleshooting demand cooling or liquid/vapor injection systems, you need to keep a few things in mind. For example, you need to make sure you have the right amount of tees when you retrofit a compressor with a vapor injection system. You may also have to repipe the vapor line and add a DTC (discharge temperature control valves). Trevor and Bryan also discuss: What happens when we change refrigerants Return gas temperature and mass flow rate Compressor head cooling fans Motor operation and spinning indicators Visual inspection Vapor injection vs. mechanical subcooling KVE vs. K4E Part replacement DTC vs. EEV w/ CoreSense diagnostics Learn more about Refrigeration Technologies HERE. If you have an iPhone, subscribe to the podcast HERE, and if you have an Android phone, subscribe HERE.

Oct 15, 2020 • 39min
Intro to CO2 w/ Don Gillis
Don Gillis with Emerson joins us on the podcast to teach us the basics of CO2 as a refrigerant. He explains how it works and its applications. Carbon dioxide is a colorless, odorless gas that is becoming an important refrigerant for commercial refrigeration (R-744). It is desirable because it has a low critical point and high triple point, so we can use subcritical (below the critical point) and transcritical (above the critical point) CO2. Carbon dioxide also has a very low global warming potential (1), is inexpensive, and is very efficient at transferring heat. Above the critical point, we see transcritical fluid, which is a high-pressure fluid. Below the critical point, you get lower pressures. We don't see CO2 in our everyday air conditioners because it doesn't have the typical pressure-temperature relationship above the critical point (over ~88-degree ambient conditions). It is also more common in regions with colder ambient conditions like Canada. We rarely encounter the triple point in other refrigerants, but it is crucial in CO2 refrigeration. The triple point is the temperature and pressure at which a substance can exist as a solid, liquid, and gas. The triple point of carbon dioxide is very high, so we can come across it in normal equipment operation. We don't want dry ice in the system, so we want to charge the CO2 system with our pressure well above the triple-point pressure. Don and Bryan also discuss: John Gorrie's original machine Recovery (or lack thereof) Sublimation of dry ice (solid to vapor CO2) Risk of asphyxiation in confined spaces Leak detection Saturation and operation pressures of CO2 compared to HFCs Liquid vs. gas tanks Piping and fittings CO2 grades and moisture content Sales and distribution Learn more about Refrigeration Technologies HERE. If you have an iPhone, subscribe to the podcast HERE, and if you have an Android phone, subscribe HERE.

Oct 1, 2020 • 44min
Building Performance QA with Sam Myers
Sam Myers of Retrotec joins Bryan and Kaleb on the podcast to discuss building performance. He also answers some of our listeners' questions. Checking airflow is important for building science as well as HVAC. However, "airflow" is vague and can refer to static pressure readings (which isn't actually "airflow" at all), air from whole-home ventilation systems, or CFM per ton. We can also look at total system airflow with flow hoods. Equipment settings also matter when it comes to measuring airflow as it relates to building performance. Leakiness (of the ducts or structure) is a common building performance issue. Blower door tests can determine the building pressurization and are a great tool for determining leakiness. However, we usually only do comprehensive "airflow," duct leakage, and building envelope tests during renovations or other large-scale projects; we don't typically check "airflow" and duct leakage when we do small repairs like capacitor replacement. When balancing airflow, we usually rely on room-by-room load calculations. However, Sam finds that finding a pressure differential between rooms can be a bit more reliable. The main drawback is that a pressure differential won't tell you if a room isn't getting enough air, but the opposite problem is far more common and can be addressed. The duct system's location also has a lot to do with a building's ventilation or sealing strategy. If the attic is in an unconditioned space in a humid climate, it may be best to seal the area to control the dew point. Sam, Bryan, and Kaleb also discuss: Airflow measurement instruments Total system airflow Balancing and isolating rooms with comfort issues Grilles, diffusers, and vents in zonal duct design Using your senses during balancing Ventilating vs. sealing the building envelope Infiltration and air mixing Split-level homes Blower doors Building performance in commercial HVAC Learn more about Refrigeration Technologies HERE. If you have an iPhone, subscribe to the podcast HERE, and if you have an Android phone, subscribe HERE.

Sep 28, 2020 • 1h
What is Correct Airflow?
The great Ed Janowiak (Jon-Oh-Wok) joins us to talk about what correct airflow really looks like. He also explains how to design for it appropriately. The ACCA design series (Manuals J, S, and D) all go hand in hand to design HVAC systems properly for a given space. Correct airflow will depend on how a technician or designer uses the ACCA design series. When we say "correct airflow," we mean that the CFM per ton matches the sensible and latent load for a space while maximizing comfort for building occupants. In many cases, 400 CFM per ton is the rule-of-thumb baseline for many systems, but it's not a one-size-fits-all solution. The point of the ACCA manuals is to use math to determine solutions tailored to a specific space and avoid rules of thumb. Many technicians prefer higher airflow in the field because it leads to fewer technical problems. However, the occupied space can suffer from reduced latent removal when you have higher airflow. Variable-speed technology helps a bit to allow longer runtimes to help with dehumidification, but consumers may not be in the market to purchase those solutions. We can use airflow grids to determine the CFM on a running system. When those grids determine that the CFM per ton is below 300, that means the equipment is likely failing to match the required sensible BTUs. Airflow also affects pressurization, which you can measure with a manometer. Overall, you will want to track airflow trends and work to optimize the airflow. Ed and Bryan also discuss: Using software for calculations Friction rate Sensible heat ratio (SHR) Equipment selection and code compliance Relative humidity targets Intermittent ventilation Ancillary dehumidification Duct sweating Residential vs. commercial equipment design gap Blower door testing Testing delivered capacity and balancing Zonal pressure testing Extended performance data Learn more about Refrigeration Technologies HERE. If you have an iPhone, subscribe to the podcast HERE, and if you have an Android phone, subscribe HERE.

Sep 24, 2020 • 48min
Digital Compressor Facts
Have you ever heard a compressor that keeps changing in sound as it runs? Trevor with Emerson tells us more about what that is all about and how the digital compressor operates.