
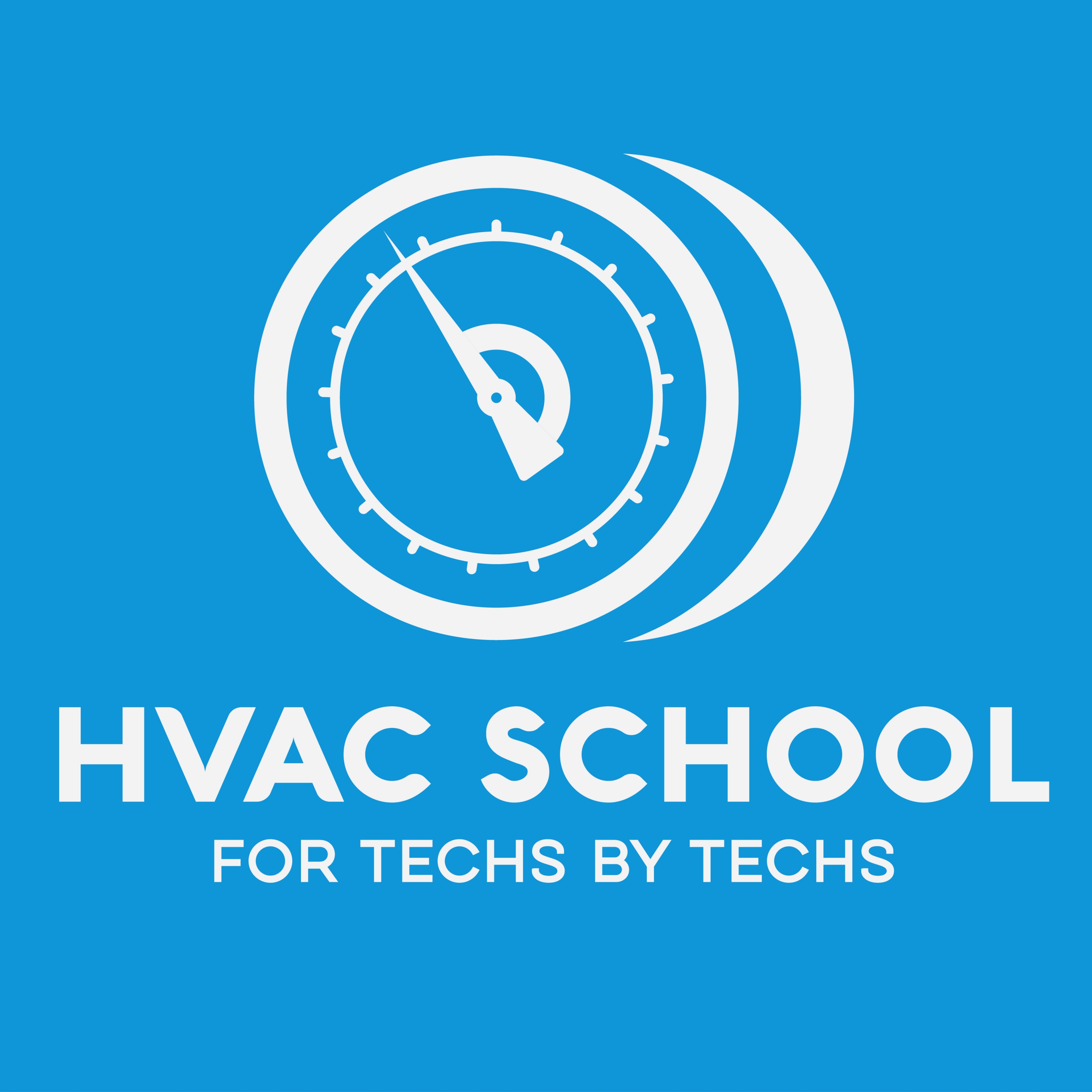
HVAC School - For Techs, By Techs
Bryan Orr
Real training for HVAC ( Heating, Ventilation, Air Conditioning and Refrigeration) Technicians. Including recorded tech training, interviews, diagnostics and general conversations about the trade.
Episodes
Mentioned books

Dec 29, 2020 • 7min
Service Valve Tips - Short 105
In this short podcast episode, Bryan talks about some tips you can use when working with a multi-position service valve. A service valve will have a line connection, which connects the valve to your line set. You also have a gauge port that you can connect to, a valve stem, and a packing gland nut (directly beneath the valve stem). If your stem is completely back-seated, then your gauge port is completely closed from both the line and system connection. If you crack the stem off the back seat, then the gauge, line, and system can all communicate. Completely front-seating the valve will generally close off the line connection, but it may also close off to the system connection on some valves. Mid-seating puts the valve stem right in the center for maximum flow. If you're working with a service valve in a grocery refrigeration application or old A/C system, you may be tempted to use any old wrench on the valve and can damage the valve. So, whenever you work with one of these valves, make sure you use a refrigeration service wrench only. Also, be sure to exercise caution. The packing gland nut helps keep everything together and prevents leaks. However, you need to loosen it by a quarter to full turn before opening the valve. If you don't loosen the packing gland nut, you will have a hard time adjusting the valve, and you may even damage it. Whenever you do any brazing on or near a service valve, be sure to protect it from the heat (such as with Refrigeration Technologies WetRag). You'll also want to mid-seat the valve before you start flowing nitrogen. Learn more about Refrigeration Technologies HERE. If you have an iPhone, subscribe to the podcast HERE, and if you have an Android phone, subscribe HERE.

Dec 24, 2020 • 34min
Refrigeration Scroll Compressors
In this podcast episode, Bryan and Trevor Matthews from Emerson talk through scroll compressors in commercial refrigeration equipment. Scroll compressors are not a monolith; although they all function similarly, they have different fine details and manufacturing protocols by application. Low-temp, medium-temp, high-temp, and A/C scroll compressors each have unique designs, operating conditions, and service considerations. Copeland has a medium-temp scroll compressor line (ZB and ZS) for medium and high-temp applications. They also have a low-temp line (ZF). Within those lines, there are also small displacement and large displacement compressors, advanced scroll temperature protection devices, and other unique features. Since scroll compressors are prone to thermal overload, some Copeland compressors have advanced scroll temperature protection devices. These devices help redirect the discharge gas to the suction gas, which gets the compressor to trip out on thermal overload more quickly. In cases when you're tempted to condemn the compressor, shut it off and let it cool down before you jump to conclusions. The compression ratio is the main difference between A/C and refrigeration scroll compressors. A/C scrolls can handle a compression ratio of 11:1. Conversely, refrigeration scrolls can handle 26:1 compression ratios. Copeland scroll compressors also have electronic controls. When setting up these controls, you need to keep the scroll compressor type and special features in mind, including temperature protection devices. In other words, you can't set up a low-temp compressor the same as a medium-temp and so on. Bryan and Trevor also discuss: Differences across Copeland scroll compressors Low-temp vs. medium-temp vs. high-temp refrigeration Copeland compressor nomenclature Compressor pump down Proper vacuum CoreSense diagnostics Vapor injection and compressor capacity PTC (positive temperature coefficient) thermistors Using AE bulletins as tools Crankcase heaters and other accessories Learn more about Refrigeration Technologies HERE. If you have an iPhone, subscribe to the podcast HERE, and if you have an Android phone, subscribe HERE.

Dec 17, 2020 • 37min
Bert's Top Soft Skills Tips
In this episode, Bryan and Bert talk about soft skills. They also discuss why soft skills are important in highly technical trades. Bert's class defined "soft skills" as communication skills; these can be verbal but may also include body language and how we respond to emotional situations. Bert thinks these skills are some of the most important skills you can develop in the HVAC industry and in life overall. You will only be able to make the most of your talents and career if you work on your communication and people skills. You can start improving your soft skills when you learn to see yourself accurately. Are you introverted or extroverted? Have a Type A or Type B personality? Once you can see your strengths and weaknesses, you can learn where you need to be more engaged with the customer or give them some space. You can analyze your relationships to see where your strengths and weaknesses are (or if you're the problem in your interactions with others). Listening skills are also crucial for interactions with customers. Being a good listener, keeping your emotions in check, and proposing solutions will give your customers a better experience. Having the discipline to be a good listener will also help your work and personal relationships. If you need some tips or have some questions about your general vibe, ask people who want to tell you the truth about their "experience" with you (and listen to them). Body language is also critical. Do your best to show that you're attentive, helpful, and friendly. Bert and Bryan also discuss: Residential vs. commercial interpersonal skills Skills vs. natural abilities Metacognition Customer experience Discipline Working well with your bosses or other employees Eye contact Complaining (just don't do it) Dos and don'ts of showing empathy Learn more about Refrigeration Technologies HERE. If you have an iPhone, subscribe to the podcast HERE, and if you have an Android phone, subscribe HERE.

Dec 10, 2020 • 58min
Gas Furnace Diagnosis & Inspection w/ Jim Bergmann
In this podcast episode, Bryan and Jim Bergmann talk about gas furnace diagnosis and inspection. They cover the ins and outs of furnace assessment. A gas furnace diagnosis requires a few important measurements, but a solid visual inspection is perhaps even more vital. You'll want to look at the venting and condensate disposal systems. You'll want to make sure the flue gas can escape properly and that the terminations are correct and safe; if you're not looking at the manual and checking the venting, you can put your customers at risk of serious CO poisoning and even death. On the condensate disposal system side, you risk trapping flue gases in the trap. Condensate can also build up into the secondary heat exchanger, which leads to a rise in CO. We also need to look out for issues on the electrical side. Reverse polarity and poor grounds are often the greatest culprits for electrical failures. Broken connections are also common problems as with other HVAC systems. Dust and dirt can also get behind the circuit board, which can cause flame rectification problems. Fixing an electronic circuit board can intimidate some techs, but soldering a circuit board is quite a bit like soldering a coil. When it comes to measurements, your pressures are going to be some of the most important readings you can take. It's also a wise idea to have your own combustion analyzer and make sure to take care of it over time. Bryan and Jim also discuss: New MeasureQuick developments Measurements to use in MeasureQuick CAZ testing CO sources 90+ furnace condensate drains Air filtration and MERV ratings AHRI CO testing steps Conduction through the flame rectification circuit Incoming gas pressure Incorporating MeasureQuick into diagnosis Learn more about Refrigeration Technologies HERE. If you have an iPhone, subscribe to the podcast HERE, and if you have an Android phone, subscribe HERE.

Dec 8, 2020 • 8min
Pitot vs. Static Pressure Probe - Short 104
In this short podcast episode, Bryan talks about the differences between pitot tubes and static pressure probes. He also explains how each one works. People often mix up static pressure probes and pitot tubes. A pitot tube is a tube within a tube, and a static pressure probe is just a tube with holes in the side but not at the end. When we measure static pressure, we're measuring the pressure against the duct. (Think of it as balloon pressure rather than air velocity.) We use static pressure probes to look for a differential between a probe and atmospheric pressure or between two probes. As the air travels around a static pressure probe pointing in the correct direction, its velocity force will not act on the probe. We do NOT want to measure velocity with a static pressure probe. Pitot tubes, however, come in twos. One tube comes off the side (attach a hose to this one), and one comes off the bottom. You can use the side port of the pitot tube to measure static pressure. You also have an end port to measure total pressure, which is static pressure plus velocity pressure. When using a pitot tube, you can get the velocity pressure by subtracting the static pressure from the total pressure. You point the pitot tube into the airstream to get that measurement. However, pitot tubes will only give you accurate data if you have an accurate manometer and have ideal velocity conditions. Proper positioning and duct traverse techniques are also integral to getting accurate data. Learn more about Refrigeration Technologies HERE. If you have an iPhone, subscribe to the podcast HERE, and if you have an Android phone, subscribe HERE.

Dec 3, 2020 • 23min
Balancing Evaporators in a Circuit Using the TXV
In this podcast episode, Bryan and Nathan discuss balancing evaporators in a multi-coil circuit. They specifically focus on using the TXV to do so. When we say "balancing evaporators" in a multi-coil circuit, we're referring to the temperature of the air leaving the system; we are worried about the air keeping the product cool in grocery refrigeration. If everything works correctly, the evaporators on a rack can have different temperatures due to different refrigerant flow rates. That's when we can turn out attention to the expansion valves, which meter the refrigerant into the evaporator and manage the refrigerant flow. Balancing evaporators with the TXV is a controversial practice; many people insist that you should balance evaporators with the equivalent line set length only. However, it's not usually possible to repipe the entire circuit, so using the TXV is much more practical. You essentially run higher superheat on the colder cases by using the TXV to create a restriction. When you adjust the TXV, you'll want to do so in quarter-turn increments on the highest and lowest cases and wait for the temperatures to stabilize (about 30 minutes) before making further adjustments. Tuning on rack refrigerators is another related concept. We don't see mechanical EPRs very often anymore, so we can rely on the system to make programmatic adjustments. Once the temperature and operation are stable, you can set your superheat. Typically, balancing evaporators will be more important on systems with electronic EPRs than mechanical EPRs. Bryan and Nathan also discuss: Pressure drop associated with fittings Where to take superheat Flood back risks Modern TXVs and EEVs Defrost controller considerations Discharge air differences Learn more about Refrigeration Technologies HERE. If you have an iPhone, subscribe to the podcast HERE, and if you have an Android phone, subscribe HERE.

Dec 1, 2020 • 9min
Mass Flow vs. Volume Flow - Short 103
In this short podcast episode, Bryan discusses the difference between mass flow and volume flow when referring to HVAC equipment processes. When you are confused as to whether you're dealing with mass or volume flow, think about the units. For example, cubic feet per minute (CFM) is a measure of volume because we're talking about cubic units. We care about the volume when we think about air mixing and velocity, but volume isn't much of an indicator of the actual cooling power. The mass or weight of the air matters more when we think about cooling a space. There is a lot of variation in how much air weighs, which will impact the performance of HVAC equipment under given conditions. Standard air has a weight of 0.075 pounds per cubic foot, but that can vary depending on humidity, temperature, and pressure conditions. When you think about volume flow rate, think about moving boxes of matter. As a blower operates, it moves a series of air "boxes," which is a useful way to look at air velocity. Compressors have a fixed volume in their compression chambers, unlike blower wheels. (Blower wheels move different volumes of air based on motor staging and other conditions.) However, mass flow is NOT fixed. In a compressor, we can fill those boxes with more weight (higher mass flow). On occasion, too much mass will move at once; a hot pull down is a common scenario where we have too much mass flow. In those cases, we can use crankcase pressure regulators. A system's compression ratio also has a major effect on mass flow rate; the "boxes" might be too light to keep the compressor cool enough to operate efficiently. In the worst-case scenario, the compressor may overheat. Learn more about Refrigeration Technologies HERE. If you have an iPhone, subscribe to the podcast HERE, and if you have an Android phone, subscribe HERE.

Nov 26, 2020 • 29min
Freezing Evaporator Fun Facts & Frippery
In this episode, Bryan and Sam discuss freezing evaporator coils. They explain why frozen coils happen and how to address them. When the coil's surface temperature drops below freezing (32 degrees), the moisture in the air that condenses on the coil can freeze to the coil. In those situations, your suction saturation will probably be in the mid to high twenties. Generally, freezing evaporators will occur when you have less load on the evaporator. When there is less heat, the evaporator temperature will drop accordingly. The return air temperature is usually around 35 degrees, though that number can fluctuate on older equipment or on systems with dirty coils. Freeze-ups usually happen due to poor airflow or low refrigerant charge, though low refrigerant is usually less severe than airflow or compound airflow-charge problems. Conditions that cause low mass flow can lead to freeze-ups. When you approach a frozen coil, the first thing you want to do is defrost the coil completely. Then, you will want to check airflow (filter, blower wheel, and coil cleanliness) and then refrigerant restrictions and charge. You'll especially want to make sure you check the liquid line for temperature drops and ensure its temperature is warmer than the outdoor ambient temperature. In addition, static pressure is a valuable reading for determining airflow. Drain lines can also freeze, though it's a rare occurrence. When that happens, you do NOT want to blow out the blockage with nitrogen! You will break the drain line before any ice comes out. Sam and Bryan also discuss: Driving the temperature down Low charge as a cause of freezing Considerations for various system types Using a scale for charging Heat pumps in heat mode ECM motor failures Learn more about Refrigeration Technologies HERE. If you have an iPhone, subscribe to the podcast HERE, and if you have an Android phone, subscribe HERE.

Nov 19, 2020 • 37min
Drain Cleaning - More To It Than We Think
Mike Klokus and Corey Cruz from Kalos come on the podcast to talk about drain cleaning. They discuss their tips and some best practices. Approximately 50% of the calls in the light commercial division have to do with drains, and drain cleaning is a common PM procedure. The procedure starts off when you pull the panel off the air handler and look in the drain pan. Muck can accumulate in the pan and in the back and side channels. Pay attention to the unit orientation and the drain pitch before you even start cleaning. If you need to get underneath the channels, you can use bottle brushes. Dedicated drains are associated with only one unit. However, communal drains have multiple units running into a single drain line and have a special set of considerations. You don't want to pour something caustic into the common drain and have it overflow on the lower levels. It's also best to know where the drain leads; you don't want chemicals to wash out into a garden. Water can also create a slippery surface and cause someone to fall. Generally, the top 3 drain cleaning methods use a shop vacuum, compressed air, or plain water; each one has its place, but they also have drawbacks. While water is ideal for cleaning, it's not always available and practical. Shop vacs are good, but the suction is limited. Compressed air is better at unclogging than cleaning, and it can cause you to blow away piping if there's a loose pipe fitting. Mike, Corey, and Bryan also discuss: Condensate safeties Using shop vacs and extensions Weight in the drain pan Cleaning with chemicals Copper vs. aluminum for bacterial zoogloea Priming the drain line Condensate assembly cleanings in residential HVAC Capping vents (don't do it) Learn more about Refrigeration Technologies HERE. If you have an iPhone, subscribe to the podcast HERE, and if you have an Android phone, subscribe HERE.

Nov 17, 2020 • 6min
Open v Closed Refrigeration - Short 102
In this short podcast episode, Bryan talks about the differences between single-phase and two-phase refrigeration. This particular episode is about the fundamentals of physics, chemistry, and science in general. When we talk about phases, we're referring to the changes in the states of matter. We typically think of the states of matter as solid, liquid, and gas. In refrigeration systems, the refrigerant usually changes from a liquid to a vapor in the evaporator and then from a vapor to a liquid in the condenser; that is an example of two-phase refrigeration. We get two-phase refrigeration anytime we're changing the state of matter in order to accomplish refrigeration. When you change the state of matter, you transfer a lot more heat than with a single-phase system. You get more heat in and out between phases due to latent. Between a solid and a liquid, the energy that goes towards the phase change is the latent heat of fusion. Between a liquid and a gas, the energy that goes into the phase change is the latent heat of vaporization. It takes a lot more heat to condense or boil water than it does to change its temperature by one degree, so we take advantage of that capacity to absorb heat into the boiling refrigerant. There are also forms of single-phase refrigeration, including John Gorrie's open-refrigeration machine. Gorrie's machine was just compressing and decompressing air; it was not changing the state of the air. In single-phase refrigeration, we can't make use of the extra energy from changing states. In those cases, condensers would be gas coolers. However, when you think about it, the process of refrigerating the space is a form of single-phase refrigeration; we don't change the phase of the air. So, we merely use two-phase refrigeration to drive single-phase refrigeration. Learn more about Refrigeration Technologies HERE. If you have an iPhone, subscribe to the podcast HERE, and if you have an Android phone, subscribe HERE.