
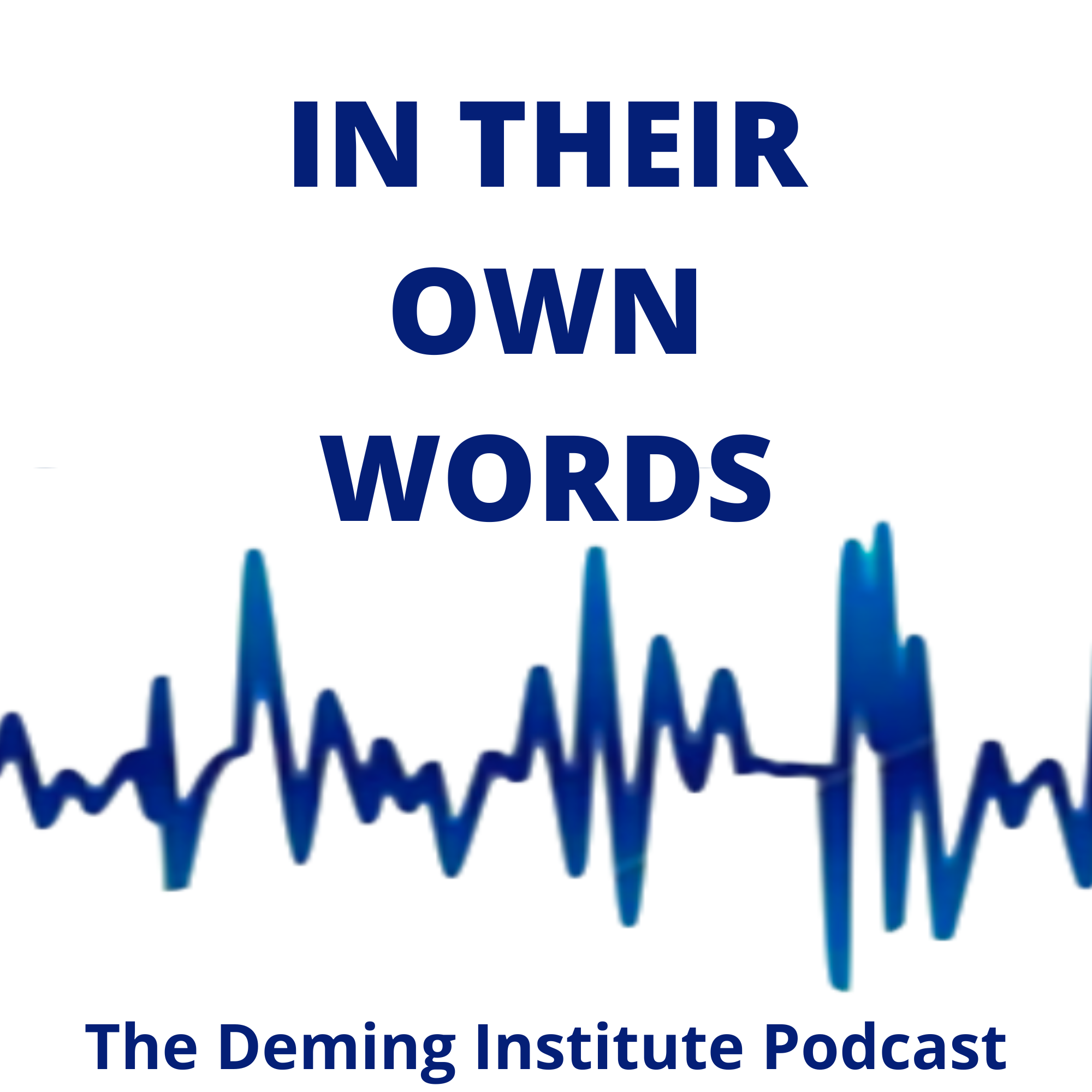
In Their Own Words
The Deming Institute
Interviews with members of The Deming Institute community, including industry leaders, practitioners, educators, Deming family members and others who share their stories of transformation and success through the innovative management and quality theories of Dr. W. Edwards Deming.
Episodes
Mentioned books

Aug 4, 2025 • 1h 10min
Rare Photos and Fresh Stories: An Insider's View of Deming's World (Part 2)
Step into a treasure trove of rare stories, photos, and audio clips as Bill Scherkenbach shares his decades with Dr. Deming. From boardrooms to sleigh rides, discover the moments, minds, and memories that shaped modern quality thinking, told by someone who lived it. A powerful blend of insight, humor, and history you won’t want to miss. (You can see the slides from the podcast here.) TRANSCRIPT 0:00:02.4 Andrew Stotz: My name is Andrew Stotz, and I'll be your host as we dive deeper into the teachings of Dr. W. Edwards Deming. Today, I'm continuing my discussion with Bill Scherkenbach, a dedicated protégé of Dr. Deming since 1972. Bill met with Dr. Deming more than a thousand times and later led statistical methods and process improvement at Ford and GM at Deming's recommendation. He authored 'The Deming Route to Quality and Productivity' at Deming's behest and at 79 is still championing his mentor's message. Learn, have fun, and make a difference. Bill, take it away. 0:00:41.2 Bill Scherkenbach: Well, thank you. Thank you, Andrew. It's an honor to be asked back. Many places don't. 0:00:48.7 Andrew Stotz: I really enjoyed our first discussion, and particularly towards the end of it, it got a little personal and emotional, and I appreciate that you shared your journey. That was amazing. 0:01:00.9 Bill Scherkenbach: Thank you. Thank you. It is personal. 0:01:05.2 Andrew Stotz: Yeah. 0:01:05.4 Bill Scherkenbach: But today, along that wavelength, I brought some pictures or photos and letters and audios of my association with Dr. Deming. So, if you might bring them up, we can start the commenting. 0:01:27.9 Andrew Stotz: Wonderful. Well, hopefully you see a screen now up. 0:01:34.8 Bill Scherkenbach: Yes. Yep. 0:01:35.8 Andrew Stotz: Okay. And for the audience, just to let you know, for the listeners, we're going to show these and I'll try to explain a little bit about what we're talking about because you're not going to be able to see the pictures. But the first thing is the title is An Insider's View of Deming. Learn, have fun, make a difference. And we see a great picture on the left-hand side, and then I threw in a picture of a Lincoln Continental, which we're going to talk about later, which is kind of fun. But maybe you can take it from there, Bill. 0:02:07.2 Bill Scherkenbach: Yeah. Well, we can talk a little bit later on on that, but this is a picture of me and my wife, Mary Ellen, with Dr. Deming having fun. We were at a restaurant in Northville called Elizabeth's, and it's something that he enjoyed to do just about every evening. 0:02:31.3 Andrew Stotz: Great. Well, what a kickoff. So let's go to the next one. And you guys all look great in that photo. 0:02:38.2 Bill Scherkenbach: Thank you. Thank you. Thank you. Yeah. This is a letter that I received from Dr. Deming back in May of '85, auspicious because the letter dated 13 May, that's my birthday. But for those who cannot read it, should I read the letter for you? 0:03:05.2 Andrew Stotz: Either you or I can read it for you. You tell me. 0:03:08.3 Bill Scherkenbach: Okay. Well, yeah. Why don't you read it? 0:03:10.9 Andrew Stotz: Okay. So, the letter is addressed to a particular person. It says, this is written by Dr. Deming, this acknowledges your kind letter of the 29th April. He that depends solely on statistical process control will be out of a job in three years. The record is clear, the record is clean, no exceptions. A whole program of improvement of quality and productivity is necessary, and it requires that top management learn what their job is. No part of the program will by itself suffice. Your letter does not describe your program, hence comment is difficult. I am happy to learn that Bill Scherkenbach will work with you. His achievements are renowned. He is excelled by nobody. I am sure that you will follow his guidance, not only while he is there with you, but from that then on out. I send best wishes and remain yours sincerely, W. Edwards Deming. 0:04:19.2 Bill Scherkenbach: Yes. I did spend a week with this organization, and as Deming said, and in many, many cases, the local management or local part of the organization get very enthusiastic, but the top management did not buy in. And so very little happened there, unfortunately. 0:04:53.9 Andrew Stotz: Yeah. And I missed that the top right-hand corner in handwritten, it says Portland, 20 May 1985. Dear Bill, I neglected to hand this to you in San Francisco, W. E. D. 0:05:08.1 Bill Scherkenbach: Yeah. We went to, we. Dr. Deming and I were in San Francisco to meet with Shoichiro Toyoda and his wife. It was a social call. Shoichiro was in town. I don't know where his brother Tatsuro was. Tatsuro headed up NUMI, but Shoichiro was head of it all and was in the US. And wanted to just have a dinner with Dr. Deming. I'm embarrassingly cloudy. We met in a hotel and I can't tell you which one, but it was a nice, relaxing dinner. The English was a bit stilted, but Soichiro wanted to have a dinner with Dr. Deming and to express his appreciation. 0:06:31.3 Andrew Stotz: And he was a titan of industry at the time and in 1985 was really making a beachhead and a real expansion into the US market. Why did he want to meet with Dr. Deming? What was the connection there? Maybe for those that don't know. 0:06:55.2 Bill Scherkenbach: He was in town and Deming was nearby in town and just wanted to express his appreciation. I guess, Tatsuro, his brother wasn't there, and Tatsuro headed up NUMI, the partnership between GM and Toyota. But Shoichiro was there and just wanted to express appreciation. 0:07:35.1 Andrew Stotz: Great. Okay. So shall we continue on? 0:07:40.0 Bill Scherkenbach: Yeah. We have a Where is Quality Made? Famous talking from Dr. Deming, and hopefully the audio translates well. 0:07:55.3 Andrew Stotz: Yes, we'll see. Let's go. 0:07:59.5 Dr. Deming: Where's quality made? Answer is in the top management. The quality of the output of a company cannot be better than the quality directed at the top. The people in the plants and in service organizations can only produce, at best the design of product and service prescribed and designed by the management. Job security and jobs are dependent on management's foresight to design product and service [that] will entice customers and build the market. 0:08:31.6 Andrew Stotz: So where did that come from? And tell us more about that. 0:08:36.2 Bill Scherkenbach: Well, I'm not exactly sure which particular seminar or meeting that was, but over the years I have, have, we've made a number of audio recordings and videos of Dr. Deming in his meetings. And so we're looking to get them to the Deming Institute so they can process them and distribute. 0:09:11.8 Andrew Stotz: And why is this so important? He's talking about quality is made at the top where we can see many people think that quality is made by the worker. Do your best. Quality is your responsibility. Tell us more about why you wanted to talk about this. 0:09:32.9 Bill Scherkenbach: Well, it's a common, it's a common, very common mistake. He learned back in 1950, and I think I mentioned it in our first talk, that he gave a number of courses at Stanford during the war and people learned SPC. But when the war was over, over here, because management didn't buy in, nothing really happened. And he learned in his visit in 1950 when he was able, as we said, Mr. Koyanagi was able to get a meeting, a number of seminars done with top management in Japan after the war. And he thought that that, he saw that that actually did make a difference, that management was absolutely key. And in every one of his seminars, he would make, he would make this point, that quality is made at the top. 0:10:54.0 Andrew Stotz: And what was interesting is that, of course, the Japanese senior management, were very receptive. It's many times the case that Deming may have interacted with some senior management at the top of a company, but they weren't receptive or willing to implement what he's talking about. 0:11:12.6 Bill Scherkenbach: Yeah. I think I mentioned last time that you need maybe a significant physical or logical or emotional event. And Ford lost a few billion dollars and was then looking, is there a better way? Japan lost a war, and the tradition over there is to perhaps listen to the conqueror. But MacArthur was very astute, my understanding, that you're not going to go in and replace the emperor and really mix the place up from what their culture is, which is very, very, very astute, in my opinion. 0:12:11.4 Andrew Stotz: Okay. So let's continue. And we see a document now up on the screen and a diagram. And maybe you can explain this one. 0:12:24.8 Bill Scherkenbach: Yeah. This is one of the foils, as he called them, that he wrote on his lantern, which is the overhead projector for all the young people. And making another very, very important point. And that is, he's quoting John Tukey, "the more you know what's wrong with a figure, the more useful it becomes." And he also, at various times, would, would, would talk about George Gallup. And Gallup was his friend. And George Gallup would say that unless you've gone through the slogging of collecting data, you shouldn't be too quickly using data or analyzing data. Because if you go to collect it, you know that some people just aren't there. And this is primarily survey stuff that Gallup was talking about. But Tukey was talking about anything. And Deming, along the way, with his learnings from Shewhart, what I've developed is based on Deming's questions come from theory, created a theory, question, data, action cycle, similar to a PDSA. And so that you need to know what the question was before you can use the data. And Dr. Deming's example was you can't use manganese dioxide for just anything. If it's really, really critical work, then you need to know what's in it that could contaminate it or interact with the other chemicals that you're trying to mix it with. Hugely important in chemistry, hugely important anywhere. And he talked, yes, we do have some audio from Dr. Deming talking about another analogy, on I can't even wash the table unless you tell me what you're going to use it for. 0:15:24.0 Andrew Stotz: I remember watching a video of this with him, with Robert Reich, I think it was, being interviewed. And it was such an impactful thing because I always thought you just tell people what to do and they go do it. And so let's listen to the audio. I'm going to play it now. One second. 0:15:42.6 Dr. Deming: You could teach me how to wash a table. Teach you how to rub, scrub, use brushes, rags. I'd be pretty good at it. But you know, I could not wash this table, suppose you told me my job is to wash this table. I have no idea what you mean. There's no meaning to that. You must tell me what you're going to use the table for. I want to see a flow diagram, work moving. Here I am. My job is to wash this table. I do not understand what you mean. Wash this table. There's no meaning to that. I must know what you're going to use the table for, the next stage. What will happen to the table, next stage, in the flow diagram? You want to put books on it? Well, it's clean enough for that now. To wash the table, I just go through it from just here, make a look at it. If I work a little, good enough. If I clean enough to eat off of it, well, it's good enough now. Or use it for an operating table? Oh, totally different now. Totally different. Now I scrub it with scalding water, top, bottom, legs, several times. I scrub the floor underneath and for some radius. If I don't know the next stage, I cannot wash the table. 0:17:28.8 Andrew Stotz: Tell us your thoughts on that. 0:17:31.5 Bill Scherkenbach: Yep. Yep. Well, again, my theory, question, data, action cycle, if you're asking a question, you, you, if you can, and there are some confidential considerations, but if you can, you need to tell the people who are trying to answer the question what you're going to do with it. And so if you want the table washed, tell them you're going to just eat off of it or assemble microchips on it. If you, so that's the responsibility of the manager or anyone who is asking the question. So if you want to improve your questions, you got to go back up and think of, well, what's my underlying theory for the question? If this, then that, that prompts a question and the circle continues. And if you, the only reason to collect data is to take action. Both Eastern and Western philosophers absolutely have said that for centuries. 0:18:55.2 Andrew Stotz: Yeah. What's interesting, I didn't hear him say it in any other cases when he was talking about the next stage. I did hear him say before, like, what's it going to be used for? But you could hear when he's talking about the next stage, it's saying to me, that's saying the responsibility of management is looking at the overall system and communicating that and managing that, not trying to, you know, just give some blind instruction to one group, one team, one person without thinking about how it all interacts. 0:19:29.9 Bill Scherkenbach: Absolutely. Absolutely. But in the local aspect of, well, some question answers are not so local, but it's what the question asker's responsibility to let the people know what they're going to use the data for. 0:19:51.9 Andrew Stotz: Yep. Great lesson. All right. So now I've got a interesting picture up on the screen here. We have Dr. Deming and there's John Turkey, Tukey how do you say his last name? 0:20:05.6 Bill Scherkenbach: John Tukey, T-U-K-E-Y, yep. George Box and Sir David Cox. Anyone in the statistics arena knows them. We also had Stu Hunter and I believe John Hunter was there. They're not in the picture. I took the picture. But we were at Meadowbrook, which is, which is, on the old Dodge estate where Oakland University is near Detroit. And had a, we called the meeting to discuss the importance and the various perspectives of enumerative and analytic. Now, each of these men, Box, Tukey, and Cox, and all of them, all of us in the university, quite honestly, were brought up with enumerative methods. And so your standard distributional stuff and T-tests and whatever. And Deming and Tukey realized the importance of being able to not just take action on the sample, but the cause system, the system that caused the sample, or the process term, in process terms. So yeah, John Tukey was strangely enough, well, not strangely enough, but came up with a graphical method to look at data called the box and whiskers plot, with George Box standing next to him, but it's not that George didn't shave. But Tukey, very, very well known for graphical methods. 0:22:24.2 Bill Scherkenbach: George, well known for experimental methods. One of the Box, Hunter and Hunter book on statistical design of experiments is legendary. And Sir David Cox, logistic regression, which is hugely, strangely, well, not strangely enough, but huge nowadays, very important in AI, in how you would be looking to teach or have your model learn what it is that you would like them to learn to look for. So each of these gentlemen, very, very much a pinnacle of the statistical career. We were very, in a large company like Ford, we were very lucky to be able to make big meetings like this, or meetings with very influential people happen. 0:23:38.9 Andrew Stotz: Yeah. That's got to be amazing because I think when most of us listen to Dr. Deming and all that, we get a lot of what he says. But I would say that the statistical aspect and his depth of statistical knowledge is what many people, you know, it's hard for many Deming followers to deeply connect with that. And I think even myself, having, you know, read everything, listened to him, learned as much as I can, the best that I probably come up with is the idea that once I started understanding variation, one of the things I started realizing is that it's everywhere and it's in everything. And I didn't understand... 0:24:27.3 Bill Scherkenbach: Well, I still have the cartoon of a popcorn maker that was very surprised when he said, "They all popped at once." And his popcorn stand has blown up. So yeah, variation is everywhere, a lot or a little. And the thing is that you need to be able to take appropriate action. Sometime, I can remember, I can remember Bob Stemple asking me, "What did I think of the Shainin methods, Dorian Shainin, and technical approach?" And I wrote back to him and I said, "It's no better or worse than any of the other methods we don't use here at GM." The point is, all of these methods are better than Bop-A-Mole. And one of the things, well, one of the things that concerns me is that in these tool areas, and Deming's counsel to me long ago was he remembers the fights that the technical people, the statisticians in the quality profession, would have over which one is a tenth of a percent better or more effective doing this and that. And they would publicly argue, and Deming said, "Stop. It confuses management because they don't have a clue and they're staying away from all forms of quality." So, you, and I don't know the solution in this day and age where everyone is connected. But all of these methods have their strengths and weaknesses, but you have to have the savvy to figure out which one to use to help you improve. All of, each of these four were great teachers, and I have a comment from Dr. Deming on that. 0:27:11.7 Andrew Stotz: And just in wrapping this up, it's like, I think one of the things that you realize when you see this one and what you're talking about, what I realize is what a powerhouse Dr. Deming was in the area of statistics. And in some ways, it's kind of like seeing a rock star that you love to listen to and that rock star is great. And then one day on a Sunday, you go to the church and you see he's a reverend and a very solemn man who is a very, very devout devotee of Christianity and something. In some ways, that's the way I feel when I look at this, like, wow, just the roots of the depth of that is so fascinating. 0:28:03.2 Bill Scherkenbach: As you mentioned that, I'm thinking back, we were in Iowa and one of the professors there, and I forget his name, but you're right. Deming was held in awe and he was riding in the backseat. I'm driving and this professor is beside me and Dr. Deming said something and I said, how do you know? And the guy thought the world was going to come to an end that I dared ask the master, how did he know? Well, it, it, it ended up fine. 0:28:52.9 Andrew Stotz: That was the question he was trying to teach you to ask. 0:28:55.3 Bill Scherkenbach: Absolutely. You don't accept it at face value. 0:29:02.2 Andrew Stotz: So we got this other slide now. It says, what do you mean by a good teacher? Maybe you want to set this up and then I'll play the audio. 0:29:10.7 Bill Scherkenbach: Yeah. This was one of his favorite stories when he studied under Ronald Fisher, who is the big godfather of statistics, well, relatively modern stuff. So, Fisher was there at University College, as Deming will describe, and Deming wanted to know, and this is where a number of you will have recognized, he wanted to know what great minds were thinking about. 0:29:56.7 Andrew Stotz: All right. I'm going to play the clip right now. 0:30:00.2 Dr. Deming: What do you mean by a good teacher? I taught with a man, head of the department. The whole 150 students spellbound, teaching him what is wrong. And they loved it. What do you mean by a good teacher? Holding students spellbound around him. What do you mean teaching them something? I've had a number of great teachers. One was Professor Ronald Picker, University of London, University College I should say, part of the University of London. In London, 1936, no teaching could be worse. A lovable man, if you tried to work with him, could not read his writing, could stand in the way of it, room was dark and cold, he couldn't help the cold, maybe he could have put some light in the room, make mistakes, Professor Paul Ryder in the front row always helped him out. He'd come in with a piece of paper in his hand the ink not yet dry, talk about it. Wonder why the room was full of people from all over the world. I was one of them. Made a long trip, at my own expense, to learn, and we learned. We learned what that great mind was thinking about, what to him were great or important problems today. 0:31:45.9 Dr. Deming: And we saw the methods that he used for solutions. We saw what this great mind was thinking about. His influence will be known the world over for a long, long time. He would rated zero by most people that rate teachers. Another teacher that I had was Ernest Crown at Yale, very poor teacher. We'd get together afterwards, some of us, and try to figure out what he was teaching us. He was not even charismatic the way Ronald Fisher was, but we learned. We learned what that great mind was thinking about, what he thought was the problem. We learned about perturbation. His work on lunar theory will be a classic for generations. We learned. Worst teacher there could be, but we learned. 0:32:49.0 Andrew Stotz: Wow. Tell us more about that. 0:32:53.6 Bill Scherkenbach: Well, he also had a similar story because, from great teachers at NYU, and that's where I first met him and learned from him. He was my teacher, but NYU had a, they had nominations for great teachers. And Deming was able to convince, and I forget who was the, Ernest Kurnow was the dean, and he convinced the dean to wait 10 years before you survey any of the students. And the question was, did any teacher you have really make a difference in your life? And he was able to get that done or get that process agreed to, and it was for the better because in, and I don't want to... I mean, every generation has said this new generation is going to hell in a handbasket, I mean, that for forever. That's nothing new. But what's popular, it's great to be entertained, and as he said, teaching what is wrong. And so did someone make a difference in your life? And not surprisingly, Deming was one of the people selected as a great teacher from NYU Graduate Business School. 0:35:15.4 Andrew Stotz: So that's your review after 50 years after the course, huh? 0:35:21.6 Bill Scherkenbach: Yeah. 0:35:24.5 Andrew Stotz: Yeah. And so the point is that, let's separate popularity from original thinking. And also he highlighted the idea that some teachers may not come across very organized, very polished. They may need assistance to help them clarify what they're trying to get across. But just because they're kind of a mess in that way, doesn't mean they're not thinking very deeply. In fact, it may be a sign that they're thinking very deeply about it. 0:36:01.9 Bill Scherkenbach: Yeah. Now, again, remember, and I know it's a broad brush, but Deming was eminently logical. Crosby would have loved it. Wine and cheese parties showed Juran more physical. And so I think Deming's preferences there, the key to his statement is teaching what was wrong. Some people get excited in class for a variety of reasons, but the key is what are you teaching? The method depends on the ability of the teacher to connect to the students and actually teach. So it gets you back to physical, logical, and emotional. But for Deming, Fisher struck a chord with him. 0:37:09.9 Andrew Stotz: Yeah. And I think for the listener, the viewer, think about some teacher that really made an impact on you. And it could be that there was a teacher that was able to connect with you emotionally. 0:37:25.2 Bill Scherkenbach: Absolutely. 0:37:26.7 Andrew Stotz: So there's different ways. But I think of Dr. Deming wasn't a teacher of mine in university, but at the age of 24 to learn from him was definitely a teacher that left me with the most to think about. And I would say there was one other teacher, a guy named Greg Florence that was at Long Beach City College who taught me argumentation and debate. And he also really encouraged me to join the debate team, which I really couldn't because I didn't have time because I didn't have money and I had to work. But he really saw something in me, and now I love to teach debate and helping young people construct arguments. And so for all of us, I think this idea of what do you mean by a good teacher is a great discussion. So, love it. Love it. Well, we got another picture now. Speaking of teaching, the City University of New York is in the backdrop. Maybe you can set this one up. 0:38:27.0 Bill Scherkenbach: Yeah. This was a one-day, maybe one and a half with some pre-work, but essentially a one-day meeting in New York that was able to gather some of the top educators in the US, the head of the schools in California. There were some folks from Chicago. We had, as I mentioned, Albert Shanker, who was head of the American Federation of Teachers, was sitting right beside me. Other teacher organizations and education organizations. And we got together for a very meaningful thing. We got together to try and determine what is the aim of education in America. And it turned out that everyone was looking for their mic time, and we couldn't even agree on an aim for education in America. And if you can't agree on an aim, your system is everyone doing their best, and it's all, there's not too much progress, except locally or suboptimally. 0:40:02.3 Andrew Stotz: Yeah. That's a good illustration of the concept of best efforts. Dr. Deming often talked about best efforts. And here you're saying, without an aim, everybody's going to just go in their own direction. And it reminds me of a story I tell people in relation to management, which was that I had a really great boss many years ago in the field of finance research in the stock market. He was very brilliant, and he hired really good analysts. I was surrounded by the best. But he never once really brought us together to say, this is our aim. And so what ended up happening was that each person did their best, which was very good as an individual, but as a group, we never were able to really make an impact. And I explain that to my students nowadays, that I believe it's because he didn't set an aim and bring us together for that. 0:41:09.1 Bill Scherkenbach: Now, one of the, I mean, one of the things Deming very predictably talked about, as I recall, is the grades and gold stars, which were part of his forces of destruction. And the education is the way we approach education here was part of that, even before people get to get beat further down by corporate and other organizational stuff. And the grading and gold stars, I don't know how much that was, that criticism was appreciated. But everyone had a chance to talk. And in my opinion, not too many people listened. 0:42:09.3 Andrew Stotz: Now, the next one is titled Mongolian Rat. What the heck, Bill? 0:42:17.1 Bill Scherkenbach: Well, this is part of teaching what good teaching would be. You've got to listen. It's one of my favorite stories of his. 0:42:30.3 Andrew Stotz: Well, let's roll the tape. 0:42:33.3 Speaker 3: I met a professor in New York. I had a dinner one time in New York with a surgeon, professor of surgery, he gave out some marbles. Had 21 students in the class. He told them describe the surgical procedure on the jaw, in which a certain breed of Mongolian rat was very helpful. The rat would eat the flesh right down the bone, cleaner than a surgeon could do it. Very important rat. Described it in detail. Students listened intently. On examination, one of the questions was to describe the surgical procedure by use of the Mongolian rat. Twenty of the students gave him back the same marbles that he doled out. Described it as exactly the same word that he had described it. He flunked them all. All the 20. One of them said, my dear professor, I've searched the literature, I've inquired around in hospitals and other teachers. I could find no trace of any such procedure. I think that you were loading us. He passed. The others had to take a new examination. They gave him back the same marbles he doled out to them. He wanted to think. 0:43:55.0 Andrew Stotz: Marbles. I haven't heard that expression. Tell us a little bit more about what you want us to take from this. 0:44:02.6 Bill Scherkenbach: Well, I think it's pretty self-explanatory. His comment on education that teachers are handing out marbles and pieces of information, not necessarily knowledge, and the testing, you're expected to give them back what the teacher said instead of how can you process it and put it in the context of other things, as well as, I mean, maybe not in the early grades, but in the later ones, you need to be able to look at various perspectives to see who has this opinion and that opinion. And unfortunately, today, that discourse is nicely shut down. 0:45:07.3 Andrew Stotz: At first, when I heard him saying marbles, I thought he was kind of using marbles as a way of kind of saying pulling their legs, but now I understand that he was trying to say that he's giving something and then the students give it back. 0:45:24.1 Bill Scherkenbach: Yeah. Yeah. Yeah. 0:45:26.0 Andrew Stotz: Okay. Mongolian rats. 0:45:31.0 Bill Scherkenbach: Yep. Yep. So we go from learning to having fun, and here's a picture of our statistical methods office at Ford. 0:45:48.1 Andrew Stotz: And you're sitting in a sleigh? Is that what's happening there? 0:45:50.0 Bill Scherkenbach: We're sitting in a sleigh, yes, at Greenfield Village, which is where the Henry Ford Museum is, and it happened to snow, so we've got the, we've got the horse-drawn sleigh, and I was listening to your first interview of me, and I want to deeply apologize. It's Harry Artinian, and so from the left, you've got Ed Baker and Bill Craft and Pete Jessup, Harry Artinian, Narendra Sheth, Dr. Deming, Debbie Rawlings, Ann Evans, my secretary, uh ooooh, and the gentleman who worked with Jim Bakken, and then me. So, we were working and decided to have a good lunch. 0:46:58.5 Andrew Stotz: And it's a horse-drawn sleigh. And I wasn't sure if you were pulling our leg here because you said, I'm second from the far right. First from the far right, to me, looks like the horse. 0:47:09.0 Bill Scherkenbach: Yes. That's the horse's ass. Yep. 0:47:14.6 Andrew Stotz: That's a big one. 0:47:16.1 Bill Scherkenbach: It is what it is. 0:47:18.7 Andrew Stotz: Yep. Okay. Next one. Who's Sylvester? 0:47:22.3 Bill Scherkenbach: Sylvester is my son's cat. And this is one of the times Dr. Deming was in my home. And he sat down in my office at my home. And Sylvester saw a good lap and he jumped up on it and took it. And as I said, I couldn't tell who was purring louder. They both were content. 0:47:52.7 Andrew Stotz: Yeah. That looks beautiful. 0:47:55.4 Bill Scherkenbach: Yeah. It was very, very peaceful. Another fun thing, after a long day of work at Ford, we would go to Luigi's restaurant in Dearborn. I think there was a Dearborn Marriott, a big hotel. I don't know if it's there now. But that's Larry Moore, director of quality, next to Dr. Deming and me. I had a mustache back then. 0:48:30.4 Andrew Stotz: Yes. And we all loved soft serve ice cream. 0:48:34.0 Bill Scherkenbach: Soft serve ice cream. Yep. 0:48:38.0 Andrew Stotz: Yep. All right. Star-Spangled Banner. 0:48:40.9 Bill Scherkenbach: Yep. Now we're at one of my earlier houses in Northville. And Dr. Deming had written a new tune for the Star-Spangled Banner because it was an old English drinking song, Anna, the what? The Anacrocronistic Society. And he thought it was just too bawdy. I mean, you're an unsingable, except if you're drinking. So he rewrote the music for the Star-Spangled Banner. I have a copy of it here. But he, my son Matthew, my oldest son Matthew, we had just gotten one of those first Macs from Apple, Macintosh. And it had a very elementary music thing. So he put the notes that Deming had handwritten. And we put it in there and it played the tune. And so Deming was playing on our piano the Star-Spangled Banner. 0:50:04.7 Andrew Stotz: So he had a musical talent. 0:50:10.8 Bill Scherkenbach: Oh, yeah. He was a very serious study of, a student of music. Very much so. He wrote a complete Mass. He was a high church Episcopalian. And he wrote a complete Mass of the Holy Spirit with all parts. So, very much a student of music. 0:50:41.8 Andrew Stotz: And how did his religious beliefs, like Episcopalian, as you mentioned, how did that come across? Was he a person who talked about that? Was he a person that didn't talk about that? Like, how did that come across? 0:50:59.2 Bill Scherkenbach: It was more of a private thing. But then again, on every one of his books, he would begin a chapter with some quotation from different books. And many of them were from the Bible. I can remember one time in London, I'm Catholic, and so we were celebrating the St. Peter and Paul that Sunday. But he was in London and he was at St. Paul's and they weren't giving Peter any traction. But he looked up and he said, yep, you're right. It was both of those saint days. 0:51:58.3 Andrew Stotz: All right. Next one, Drive Out Fear. 0:52:01.8 Bill Scherkenbach: Oh, yeah. This was Professor Arnold. And we were having lunch in the Ford dining room, one of the Ford dining rooms. And Dr. Deming wasn't too happy of what Professor Arnold was talking about. And Professor Arnold didn't look too happy either. So, I framed the picture and put Drive Out Fear underneath it and hung it in my office. And Deming came and looked at it and smiled. 0:52:46.5 Andrew Stotz: And what was the background on Professor Arnold? And in this case, did they have opposing views or was it a particular thing or what was it that was... 0:52:58.4 Bill Scherkenbach: I don't remember the particular conversation, but Professor Arnold was head of the statistics department at Oakland University. And Ford had an agreement with Oakland University that we established a master's degree in statistics, according to Dr. Deming's viewpoint on enumerative and analytic. And no, he was very, very capable gentleman. I mean, one of the things Dr. Deming mentioned to me is if the two of us agreed all the time, one of us is redundant. So there were always discussions. This is just a snapshot in time. 0:53:52.3 Andrew Stotz: I love that quote, that one of us is redundant. That's powerful, powerful. 0:53:59.4 Bill Scherkenbach: Absolutely. Yep. This is another having fun after learning in... There were a number of restaurants we went to. He particularly liked Elizabeth's, 0:54:16.1 Andrew Stotz: And how was their relationship? How did he treat your lovely wife? 0:54:22.5 Bill Scherkenbach: Oh, I mean, very lovingly. I mean, I don't know how to describe it, but one of the family. 0:54:36.2 Andrew Stotz: Yeah. He seemed from my observation, like a true gentleman. 0:54:42.5 Bill Scherkenbach: Absolutely. Absolutely. 0:54:46.0 Andrew Stotz: Well, here we come to the Lincoln that we started off with. This is a great picture too. 0:54:51.4 Bill Scherkenbach: Yeah. That's a picture I had. It wasn't a Hasselblad, but it was a two and a quarter frame. And I had black and white film in it, but this is one of a number of pictures I took of him at the Cosmos Club. I think it was a very good picture. And in any event, it was blending learning and having fun. 0:55:19.7 Andrew Stotz: Yeah. And the Cosmos Club was near his house? 0:55:22.5 Bill Scherkenbach: Yeah. Well, it was depending on who drove. I mean, it was just, it was down a few blocks and then a number of blocks on Massachusetts Avenue. I enjoyed the drive from his house because you'd pass the Naval Observatory, which for years was the home of the chief of naval operations here. But a few decades, a few, I don't know how long ago, the vice president pulled rank on him. And so the Naval Observatory, beautiful, beautiful old house. So, the vice president lives there now. And a lot of people think Massachusetts Avenue in that area is Embassy Row. So you're passing a number of embassies on the way. And the Cosmos Club, anyone can look up. I mean, it's by invitation, members only, and Nobel laureates and Pulitzer Prize winners and a very distinguished membership, let's say. 0:56:39.3 Andrew Stotz: Here was another one, Making a Difference with Don Peterson. 0:56:43.0 Bill Scherkenbach: Yep. Yep. We're, we're, this is one of the meetings we had with Don. And it wasn't this meeting, but we were in one of them. Okay. You have it on the right there. That we periodically would have, Dr. Deming and I would have breakfast with Jim Bakken in what was known as the Penthouse at Ford. There are 12 floors, and then there was the 13th and 14th, which were private quarters, essentially. And so we were having breakfast one morning and finishing breakfast, and I'm walking a little bit ahead, and I run ahead and press the elevator button to go down one floor, and the door opens, and there's Henry Ford II in cowboy belt buckle and boots, no hat. He's going to a board meeting, he says, and Jim shied away, said, "Oh, I'm sorry, Mr. Ford." He said, "Shut up, Jim, get in here." And so we got in the elevator, and it was the small elevator. And so we're back to back, belly to belly, and Jim introduces Dr. Deming to Mr. Ford, and Ford said, "I've heard of you, Dr. Deming. God, we really need your help." And Deming had the presence of saying, "I heard of you too, Mr. Ford." It was the longest one-floor elevator ride I've ever had in my life. 0:58:49.1 Andrew Stotz: That's fascinating. All right. Next one, talking with workers. 0:58:54.1 Bill Scherkenbach: Yep. Yep. He made it a point. And this is a fine line, because you want to be able to have workers say, how, how, are they able to take pride in their work? And are there any problems and all of that? But you don't want to be in a position of then going to management and telling them because of fear in the organization. So, Dr. Deming was very good at listening and getting people to talk about their jobs and their ability to take joy and, well, pride in their work. So we had many, many meetings, different places. And this next one is with the Ford Batavia plant, I think. 1:00:01.2 Andrew Stotz: Yep. 1:00:02.4 Bill Scherkenbach: Yeah. We're riding on the tractors and having a good time. 1:00:11.3 Andrew Stotz: Who's driving? 1:00:14.2 Bill Scherkenbach: The plant manager, Ron Kaseya, was driving. 1:00:16.9 Andrew Stotz: Okay. 1:00:17.9 Bill Scherkenbach: And so I absolutely do not recall what we were laughing at, but we were having a good time. And the Batavia transaxle plant, a number of people will recognize as where Ford, it really made the point that doing better than spec is really what the job is. And it's a very powerful video that's been out there and people would recognize it as well, because we were producing the exact same transaxle in Mazda. And Mazda was influenced a lot of by Genichi Taguchi and looked to reduce variation around the nominal and not just be happy that we made spec. And John Betty, who was head up of powertrain operations and then went to the Department of Defense as assistant secretary of defense for procurement, I think, because of the quality expertise. Betty is in the front of the video saying he's absolutely convinced that this is a superior way to look at manufacturing, to look at the management of any process. You want to get your customers to brag, not just not complain. 1:02:10.3 Andrew Stotz: Yeah. Courage. 1:02:11.8 Bill Scherkenbach: And all of this takes courage. And especially in his seminars in London say, the Brits had the advantage. You guys can take courage every day. We can't get that in the US anymore. Or it's very rare to be able to buy it here. 1:02:36.3 Andrew Stotz: For the listeners, there's a logo of the John Courage beer, premium beer. 1:02:45.7 Bill Scherkenbach: Yes. Yes. It's an amber pills. 1:02:49.8 Andrew Stotz: Okay. 1:02:52.4 Bill Scherkenbach: And last but not least, well, not last, but we're looking for, and I ran across this quote from Yogi Berra, and it's very applicable right now. And Yogi Berra said, I never said... Well, what did he say? 1:03:19.2 Andrew Stotz: Never said most of the things I said. 1:03:21.4 Bill Scherkenbach: Most of the things I could have said. I never said most of the things I said. Yeah. And every day online, I see people saying Dr. Deming said this, and he said that. And if he did, I've never heard him say it. And not that I've heard him say everything. But if he did say something like, if it's not measurable, you can't manage it. He would have followed it with, that's not right. The unknown and unknowable. And so you've got a lot of people misunderstanding what Dr. Deming said. And you've got to go with, I never said most of the things that I said. 1:04:24.0 Andrew Stotz: Well, that's the great thing about this discussion is that we're getting it from the horse's mouth, someone that was there listening and being a part of it. 1:04:32.1 Bill Scherkenbach: Well, I'm glad you saw the other end of the horse. 1:04:37.5 Andrew Stotz: Yeah. So, I'm going to close out this by just sharing a little personal connection. And that is, I'm showing a picture of me in my 1963 suicide door Lincoln Continental, which I owned for 10 years in beautiful Bangkok, Thailand. And much like being kind of wild taking a ride to the Cosmos Club with Dr. Deming driving his Lincoln Continental, you could imagine how odd it looked seeing this American guy driving this 1963 Lincoln Continental on the streets of Bangkok. But I just thought I would share that just to have some fun. So, yeah. 1:05:14.3 Bill Scherkenbach: That's beautiful. Absolutely. Yeah. I didn't think the streets were that wide. 1:05:22.1 Andrew Stotz: It gets stuck in traffic, that's for sure. But wow, there's so many things that we covered. I mean, I just really, really enjoyed that trip down memory lane. Is there anything you want to share to wrap it up? 1:05:36.1 Bill Scherkenbach: No. As I said, our last conversation, we've just scratched the surface. There's so much, so much more to talk about and preserve, I think. 1:05:48.9 Andrew Stotz: Yeah. Well, I really enjoyed it. 1:05:52.1 Bill Scherkenbach: I have done my best. 1:05:53.6 Andrew Stotz: Yes, you have. You have. I've enjoyed it, and I'm sure the listeners and the viewers will enjoy it too. So, on behalf of everyone at the Deming Institute, I just want to thank you for taking the time to pull that together and to walk us through it. And for listeners out there, remember to go to Deming.org to continue your journey. And of course, go to LinkedIn to find Bill and reach out and share your interpretations of what we went through. And maybe you have a story that you'd like to share also. So, this is your host, Andrew Stotz, and I'm going to leave you with one of my favorite quotes from Dr. Deming. And that is, “people are entitled to joy in work."

Jul 21, 2025 • 1h 23min
From Student to Colleague: An Insider's View of Deming's World (Part 1)
What was it like to learn from Dr. Deming himself -- a decade before his name became legend in U.S. business circles? In this deeply personal episode, William Scherkenbach shares with host Andrew Stotz what it was like to sit in Deming’s classroom in 1972, join him for late-night chats at the Cosmos Club, and help ignite transformational change at Ford and GM. Learn how Deming’s teachings shaped a lifetime of purpose, and why Scherkenbach, now in his 80th year, is stepping back into the arena with lessons still burning bright. TRANSCRIPT 0:00:02.3 Andrew Stotz: My name is Andrew Stotz, and I'll be your host as we continue our journey into the teachings of Dr. W. Edwards Deming. Today, I'm here with featured guest William Scherkenbach, and he is known as one of the men who has spent a huge amount of time with Dr. Deming, as he mentioned to me previously, starting from 1972, over a thousand meetings and many other activities that he's been involved in. So, Bill, welcome to the show. Why don't you give us a little background about you? 0:00:39.5 William Scherkenbach: Oh, okay. Good to be here, Andrew. Well, I'm going to start with, since it's about Deming, in '72, I was newly married in April, but had been accepted to NYU Graduate School of Business, and I don't know, I never found out who wrote the course syllabus, but whoever did wrote something that it sounded like a darn interesting course, sampling, manufacturing. I was a protocol officer at the United Nations at the time and was going to night school at the New York University Graduate School of Business. So, I said, this sounds like a good course, interesting course. Had no idea who Dr. Deming was, and I walked into the first class, and there was an old, I'm 26, so he was 72 in 1972, and he was one of the first, one of the only old person who didn't say, I used to be, and I don't want to stereotype all of my peers now that I'm 79, but hopefully I don't fall into the, well, I used to be and what happened. But he did tell, I mean, statistics can be a very technical subject, and the way he taught it, I had courses in some theory of sampling, which was one of his books. 0:02:52.2 William Scherkenbach: He had three, I said three courses. The other course that I took was based on his lectures in Japan in 1950, and in fact, two of them. The third course was an extension of that. So, he was, he would teach the statistics, but he was able to tell the history of the people behind all of the thoughts and the formulas and approaches, and I found that extremely, extremely interesting. And he handed out tons of papers and material, and it was just a very, very good experience. I know he had, and he had, in my opinion, a great sense of humor, but then statisticians, what's our status? Yeah, we're like accountants, in any event. . 0:04:12.2 Andrew Stotz: Why was he teaching? I mean, at 72, most men, you know, maybe women also, but most of us are like, it's the twilight of our years, and we now know he had 30 more years to go, but why was he teaching? And also, what's interesting is when I think about Deming, I think about his overall system of what he's teaching, whereas it's interesting to think about how he taught one relatively narrow subject. 0:04:43.7 William Scherkenbach: I'll get to that as to why I think he was teaching. But yeah, back then there were no 14 Points, no glimmer of Profound Knowledge. It was, not theoretical statistics, but applied statistics with a theory behind it. And he still was really expanding on Shewhart 's work with the difference between enumerative and analytic. He used his own. Now, why he was teaching, years later, probably 1987, so yeah, a bunch of years later, when I was at Ford and I had attended at the time, I attended a senior executive week-long get-together in order to get constancy of purpose or more continuity in the senior executive group. One of the people we brought in was Dr. Peter Kastenbaum. And I found as I attended his lecture in that week-long meeting, he was a student of CI Lewis. And CI Lewis, Deming learned about from Walter Shewhart and his work in the epistemology theory of knowledge. And in any event, Deming, when he was asked, and at the time it was still in the '30s, I think, when he was at the School of Agriculture, or the agriculture department, and bringing in Shewhart, he had tried to get CI Lewis to come talk. And CI said, I would love to, but I have a commitment to my students. And so I can't adjust my schedule. 0:07:33.9 William Scherkenbach: And the students, the people who wanted to learn were sacred. And I think that had a huge impact on Dr. Deming. I mean, he spoke about it a lot. And the way, you know, in a lot of the videos that Clare Crawford-Mason did, lovingly called the old curmudgeon. But for students, he had the greatest empathy and charity for, he just didn't suffer fools gladly. If you showed him that you weren't willing to learn, he took great joy in letting them know where they, where they stood. 0:08:43.1 Andrew Stotz: And one of the things when I went into my first Deming seminar in 1990, so now we're fast forwarding 30 years from when you first met him. It was almost like there was a safe harbor for workers, for young people, for people with open minds. I mean, I didn't, I watched as he didn't suffer fools, but I'm just curious, when you go back to 1972 in those classes, I'm assuming that he was pretty gentle with the students, encouraging them and all that was... 0:09:19.0 William Scherkenbach: Oh, absolutely. In my experience, I mean, if you were by, you know, in a student in graduate school, even though the graduate school of business in New York, down on 90 Church Street, Wall Street area, there were very few people going directly from your bachelor's to the master's program. And so these were people that had probably 10 years experience in business doing stuff. And yet by going to the class, absolutely were willing to learn, listen to different points of view, which is absolutely crucial. As you progress with theory of knowledge to be able to get different perspectives on whatever it is you're trying to look at. 0:10:23.2 Andrew Stotz: I would like to continue on this period of time just because it's a snapshot we don't get that often or that easily. You mentioned CI Lewis, a man who lived from about 1880 to about the year I was born, around 1964-65, and he was known for his understanding and discussion about logic and things like that. But why was CI Lewis someone that was interesting to Dr. Deming? What was the connection from your perspective? 0:10:59.6 William Scherkenbach: Well, my understanding is Shewhart referred to him, and Lewis was a professor at Harvard, and he was in the Peirce, I believe it's called. It looks like Peirce, but it's Peirce School of, or Chair of Philosophy, and Charles Sanders Peirce was a huge, huge influence in epistemology. And so that whole chain of thought or train of thought interested Deming, but it really was, he was introduced to it by Walter Shewhart. 0:11:48.3 Andrew Stotz: There's a famous quote, I believe, by Deming about CI Lewis and his book Mind and the World Order. 0:11:56.0 William Scherkenbach: Mind and the World Order, yeah. 0:11:59.9 Andrew Stotz: Deming said he had to read it six times before he fully understood and could apply its insights. And sometimes I think maybe Dr. Deming was truly inspired by that because when I think about his work, I'm still reading it and rereading it. And just listening to the video that you did many years ago with Tim talking about reduced variation, reduced variation, what he was talking about. Sometimes when we see the big picture, there's many different components of Deming's teachings. But if you had to bring it down to kind of its core, you know, he mentioned on that video that I just watched this morning, he mentioned reduced variation, and that will get you lower costs, happier customers, more jobs. How would you say, after you've looked at it from so many different angles over so many different years, how would you say you would sum up Dr. Deming's message to the world? 0:13:01.5 William Scherkenbach: Well, that's a difficult thing to sum up. Back then, when we did the video, which was in the early '80s, maybe '84, again, he had his 14 Points by then, but he hadn't, it hadn't really, the Profound Knowledge part of that wasn't there. Now, he had used what Shewhart said, and he had read, tried to read CI Lewis, and when he spoke about the connection between theory and questions, that's what he got from Shewhart and, well, and from Lewis, and a bunch of other pragmatist philosophers. So, he, you know, he was influenced by it, and, well, that's all I can say. 0:14:27.5 Andrew Stotz: So, let's go back in time. So, you're sitting in this classroom, you're intrigued, inspired. How did the relationship go at, towards the end of the class, and then as you finished that class, how did you guys keep in touch, and how did the relationship develop? 0:14:51.0 William Scherkenbach: Well, that is an interesting story. I usually am, well, I am introverted. So I had, after I moved from New York, I got a job at Booz Allen and Hamilton in Washington, DC. So in '74, when I got the degree from NYU, we moved to Silver Spring. And obviously, he's lived on Butterworth Place since there was a Butterworth Place. So we were able to, one of the things, and this is, well, I will say it, one of his advice to me, although he gave everyone an A, I later kidded him, he didn't remember that he gave me a B. No, he gave me an A. In any event, but one of his piece of advice was, you really don't need to join ASQC. You know more about quality than any of those inspectors. And so he had learned from the '50s in the past 20 years from the 50s that inspection wasn't going to do it. Well, I didn't take his advice, and I joined ASQC, and I was reading... 0:16:36.1 Andrew Stotz:Which for those who don't know is the American Society for... 0:16:41.6 William Scherkenbach: Quality Control, back then, now it's just the American Society for Quality. I had recommended when we did a big recommendations and forecasts for the year 2000 that quality, it should be the Society for Quality worldwide, but it's ASQ now. Let's see. 0:17:07.7 Andrew Stotz: So he recommended you don't join and you didn't follow his recommendation. 0:17:12.1 William Scherkenbach: I don't join, and I read an article, and it was by a professor in Virginia Tech, and he was showing a c-chart and the data were in control, and his recommendations were to penalize the people that were high and reward the people that were low, which is even back then, Dr. Deming was absolutely on track with that. If your process is in control, it doesn't make any sense to rank order or think that any of them are sufficiently different to reward or penalize. And I had never done this, but it was, I wrote a letter to quality progress. I sent a copy to Dr. Deming, and he said, "By golly, you're right on, that's great." And so I think it probably was '75, yeah, 1975. So I had been a year or so out, and he started inviting me over to his place at Butterworth, and we would go to the Cosmos Club. And that was a logistical challenge because at the time he had, well, his garage was a separate, not attached, it was in the backyard and emptied onto an alley. And he had a huge Lincoln Continental, the ones with the doors that opened from the center. 0:19:29.0 William Scherkenbach: And he would get in and drive and then park it in back of the club and someone would watch over it. But those were some good memories. So that was my introduction to keep contact with him. As I said, I had never done that. I don't think I've written a letter to an editor ever again. 0:20:04.8 Andrew Stotz: And you're mentioning about Butterworth, which is in DC. 0:20:12.6 William Scherkenbach: Butterworth Place, yeah. 0:20:14.7 Andrew Stotz: And Butterworth Place where he had his consulting business, which he ran, I believe, out of his basement. 0:20:18.3 William Scherkenbach: Out of the basement, yep, yep, yep. 0:20:21.2 Andrew Stotz: And just out of curiosity, what was it like when you first went to his home? Here, you had met him as your teacher, you respected him, you'd been away for a little bit, he invited you over. What was that like on your first walk into his home? 0:20:38.5 William Scherkenbach: Well, went down the side, the entrance to the basement was on the side of the house, and Seal had her desk set up right by the door. And then, I don't know if you can see, this is neat compared to his desk. It was filled with books and papers, but he knew where everything was. But it was a very cordial atmosphere. 0:21:25.2 Andrew Stotz: So when you mentioned Cecelia Kilian, is that her name, who was his assistant at the time? 0:21:36.3 William Scherkenbach: Yes, yes. 0:21:38.0 Andrew Stotz: Okay, so you... 0:21:38.8 William Scherkenbach: Yeah. For Jeepers. I don't know how long, but it had to be 50 years or so. So I don't, I mean, back in the '70s, I don't know of any other. He might have had, well, okay. He, yeah. 0:22:01.1 Andrew Stotz: I think it's about 40 or 50 years. So that's an incredible relationship he had with her. And I believe she wrote something. I think I have one of her, a book that she wrote that described his life. I can't remember that one right now but... 0:22:14.2 William Scherkenbach: Yeah. A lot of, yeah, it contained a lot of... 0:22:16.6 Andrew Stotz: The World of Dr. W. Edwards Deming, I think was the name of it, yeah. 0:22:20.6 William Scherkenbach: Okay. It contained a lot of his diaries on a number of his visits to Japan and elsewhere. 0:22:32.1 Andrew Stotz: So for some of us, when we go into our professor's offices, we see it stacked full of papers, but they've been sitting there for years. And we know that the professor just doesn't really do much with it. It's just all sitting there. Why did he have so much stuff on it? Was it incoming stuff that was coming to him? Was it something he was writing? Something he was reading? What was it that was coming in and out of his desk? 0:22:55.7 William Scherkenbach: A combination of stuff. I don't know. I mean, he was constantly writing, dictating to seal, but writing and reading. He got a, I mean, as the decades proceeded out of into the '80s, after '82, the NBC white or the '80, the NBC white paper calls were coming in from all over, all over the world. So yeah, a lot of people sending him stuff. 0:23:35.8 Andrew Stotz: I remember seeing him pulling out little scraps of paper at the seminar where he was taking notes and things like that at '90. So I could imagine he was just prolific at jotting things down. And when you read what he wrote, he really is assembling a lot of the notes and things that he's heard from different people. You can really capture that. 0:23:59.0 William Scherkenbach: Yeah. He didn't have an identic memory, but he took notes and quite, you know, and what he would do at the end of the day before retiring, he'd review the notes and commit them to memory as best he could. So he, yeah, very definitely. I mean, we would, you know, and well, okay. We're still in the early days before Ford and GM, but. 0:24:37.6 Andrew Stotz: Yeah. And I want to, if I shoot forward to '90, '92, when I studied with him, I was impressed with his energy at his age and he was just on a mission. And when I hear about your discussion about the class and at that time, it's like he was forming his, you know, System of Profound Knowledge, his 14 Points. When do you think it really became a mission for him to help, let's say American industry? 0:25:09.0 William Scherkenbach: Oh, well, I think it was a mission when Ford began its relationship with him. The ability of a large corporation, as well, and Ford at the same time Pontiac, the Pontiac division, not the whole GM, but Pontiac, was learning as well. But the attachment to Ford was that you had Don Peterson at the time was president of Ford, and he was intellectually curious, and he and Deming were on the same frequency. Now, I don't want to jump ahead, but if anyone has, well, you've read my second book there, you'll know that I have mentioned that the way to change is physical, logical, and emotional. And when you look at the gurus back then, there was Deming, who was the logical guru. You had Phil Crosby, who was the emotional guru. You go to the flag and the wine and cheese party, and Deming would say, "No," and Joe Juran, who was interested in focusing on the physical organization, you report to me kind of a thing. And so each of these behemoths were passing each other in the night with the greatest respect. But, but, and so they had their constituents. The challenge is to be able to broaden the appeal. 0:27:33.8 Andrew Stotz: So we've gone through '72, and then now '75, you've written your piece, and he's brought you into the fold. You're starting to spend some time with him. I believe it was about 1981 or so when he started working with Ford. And at that time, the quality director, I think, was Larry Moore at the time. And of course, you mentioned Donald Peterson. Maybe you can help us now understand from your own perspective of what you were doing between that time and how you saw that happening. 0:28:13.4 William Scherkenbach: Well, I had, my career was, after Booz Allen, mostly in the quality reliability area. I went from Booz Allen and Hamilton to, I moved to Columbia, Maryland, because I can fondly remember my grandfather in Ironwood, Michigan, worked at the Oliver Mine. There's a lot of iron ore mines up in the UP. ANd he would, and his work, once he got out of the mines later on, was he would cut across the backyard, and his office was right there. And so he would walk home for lunch and take a nap and walk back. And I thought that really was a good style of life. So Columbia, Maryland, was designed by Rouse to be a live-in, work-in community. And so we were gonna, we moved to Columbia, and there was a consulting firm called Hitman Associates, and their specialty was energy and environmental consulting. So did a bunch of that, worked my way up to a vice president. And so, but in '81, Deming said, you know, Ford really is interested. He was convinced, and again, it's déjà vu, he spoke about, when he spoke fondly about his lectures in Japan in 1950 and onward, that he was, he was very concerned that top management needed to be there, because he had seen all the excitement at Stanford during the war, and it died out afterwards, because management wasn't involved. 0:30:42.8 Andrew Stotz: What do you mean by that? What do you mean by the excitement at Stanford? You mean people working together for the efforts of the war, or was there a particular thing that was happening at Stanford? 0:30:51.7 William Scherkenbach: Well, they were, he attributed it to the lack of management support. I mean, they learned SPC. We were able to improve quality of war material or whatever, whoever attended the Stanford courses. But he saw the same thing in Japan and was lucky to, and I'm not sure if it was Ishikawa. I'm just not sure, but he was able to get someone to make the call after a few of the seminars for the engineers to make the call to the top management to attend the next batch. And he was able, he was able to do that. And that he thought was very helpful. I, I, gave them a leg up on whatever steps were next. I'm reminded of a quote from, I think it was Lao Tzu. And he said that someone asked him, "Well, you talk to the king, why or the emperor, why are things so screwed up?" And he said, "Well, I get to talk to him an hour a week and the rest of the time his ears are filled with a bunch of crap." Or whatever the Chinese equivalent of that is. And he said, "Of course the king isn't going to be able to act correctly." Yeah, there are a lot of things that impacted any company that he helped. 0:33:07.6 Andrew Stotz: It's interesting because I believe that, I think it was Kenichi Koyanagi. 0:33:15.8 William Scherkenbach: Koyanagi, yes, it was. 0:33:17.8 Andrew Stotz: And it was in 1950 and he had a series of lectures that he did a series of times. But it's interesting that, you know, that seemed like it should have catapulted him, but then to go to where you met him in 1972 and all that, he still hadn't really made his impact in America. And that's, to me, that's a little bit interesting. 0:33:44.4 William Scherkenbach: Yeah, and quite, my take, I mean, you could tell even in '72 and '3 in classes, he was very frustrated that he wasn't being listened to. I mean, he had, his business was expert testimony in statistical design of surveys. He did road truck, truck transport studies to be able to help the interstate commerce commission. And made periodic trips back to Japan, well known in Japan, but frustrated that no one really knew about him or wasn't listening to him in the US. And that was, I mean, for years, that was my, my aim. And that is to help him be known for turning America around, not just Japan. But it's usually difficult. I mean, we did a great job at Ford and GM and a bunch of companies, but it's all dissipated. 0:35:25.9 Andrew Stotz: It's interesting because it's not like he just went as a guest and gave a couple of guest lectures. He did about 35 lectures in 1950. About 28 or almost 30 of them were to engineers and technical staff. And then about seven of them were to top level executives. And, you know, one of the quotes he said at the time from those lectures was, "the problem is at the top, quality is made in the boardroom." So just going back, that's 1950, then you meet him in 1970, then in '72, then you start to build this relationship. You've talked about Booz Allen Hamilton. Tell us more about how it progressed into working more with him, in particular Ford and that thing that started in, let's say, 1981 with Ford. 0:36:22.0 William Scherkenbach: Well, again, he was very enthusiastic about Ford because Peterson was very receptive to this, his approach. And again, it's, I think the British philosopher Johnson said, "there's nothing like the prospect of being hung in the morning to heighten a man's senses." So he, Ford had lost a couple billion bucks. They hadn't cashed in like Chrysler. GM lost a bunch too, but that, and Japan had lost a war. So does it take a significant emotional, logical, or physical event? For some folks it does. So he was very encouraged about what he was seeing at Ford. And he had recommended that Ford hire someone to be there full time to coordinate, manage, if you will. And I was one of the people he recommended and I was the one that Ford hired. So I came in as Director of Statistical Methods and Process Improvement. And they set it up outside, as Deming said, they set it up outside the quality. Larry Moore was the Director of Quality and I was Director of Statistical Methods. And that's the way it was set up. 0:38:08.0 Andrew Stotz: Were you surprised when you received that call? How did you feel when you got that call to say, "Why don't you go over there and do this job at Ford?" 0:38:18.6 William Scherkenbach: Oh, extremely, extremely happy. Yeah. Yeah. 0:38:23.1 Andrew Stotz: And so did you, did you move to Michigan or what did you do? 0:38:27.7 Andrew Stotz: I'm sorry? 0:38:29.4 Andrew Stotz: Did you move or what happened next as you took that job? 0:38:32.0 William Scherkenbach: Oh yeah, we were living in Columbia. We moved the family to the Detroit area and ended up getting a house in Northville, which is a Northwest suburb of Detroit. 0:38:49.9 Andrew Stotz: And how long were you at Ford? 0:38:53.8 William Scherkenbach: About five and a half years. And I left Ford because Deming thought that GM needed my help. Things were going well. I mean, had a great, great bunch of associates, Pete Chessa, Ed Baker, Narendra Sheth, and a bunch of, a bunch of other folks. Ed Baker took the directorship when I left. That was my, well, I recommended a number of them, but yeah, he followed on. Deming thought that there was a good organization set up. And me being a glutton for punishment went to, well, not really. A bunch of great, great people in GM, but it's, they were, each of the general managers managed a billion dollar business and a lot of, difficult to get the silos to communicate. And it really, there was not much cooperation, a lot of backstabbing. 0:40:25.0 Andrew Stotz: And how did Dr. Deming take this project on? And what was the relationship between him and, you know, let's say Donald Peterson, who was the running the company and all the people that he had involved, like yourself, and you mentioned about Ed Baker and other people, I guess, Sandy Munro and others that were there. And just curious, and Larry Moore, how did he approach that? That's a huge organization and he's coming in right at the top. What was his approach to handling that? 0:41:02.1 S2 Well, my approach was based on his recommendation that the Director of Statistical Methods should report directly to the president or the chairman, the president typically. And so based on that, I figured that what I would, how we would organize the office, my associates would each be assigned to a key vice president to be their alter ego. So we did it in a, on a divisional level. And that worked, I think, very well. The difficulty was trying to match personalities and expertise to the particular vice president. Ed Baker had very good relations with the Latin American organization, and, and he and Harry Hannett, Harold Hannett helped a lot in developing administrative applications as well. And so we sort of came up with a matrix of organization and discipline. We needed someone for finance and engineering and manufacturing, supply chain, and was able to matrix the office associates in to be able to be on site with those people to get stuff, to get stuff done. 0:43:09.5 Andrew Stotz: And what was your message at that time, and what was Dr. Deming's message? Because as we know, his message has come together very strongly after that. But at that point, it's not like he had the 14 Points that he could give them Out of the Crisis or you could give them your books that you had done. So what was like the guiding philosophy or the main things that you guys were trying to get across? 0:43:35.9 William Scherkenbach: Well, I mean, he had given in, I think, Quality, Productivity, Competitive Position back in the late '70s, and he was doing it through George Washington University, even though Myron Tribus at MIT published it. But it was a series of lectures, and he didn't really, even in the later 70s, didn't have the, the, the 14 Points. And so those came a couple years later, his thinking through, and Profound Knowledge didn't come until much later over a number of discussions of folks. But the, I mean, the key, I mean, my opinion of why it all dropped out is we dropped the ball in not working with the board. And at Ford, we didn't, weren't able to influence the Ford family. And so Peterson retires and Red Poling, a finance guy, steps in and, and everything slowly disintegrates. At least not disintegrates, well, yes. I mean, what was important under Peterson was different. But that happens in any company. A new CEO comes on board or is elected, and they've got their priorities based, as Deming would say, on their evaluation system. What's their, how are they compensated? 0:45:46.8 William Scherkenbach: And so we just didn't spend the time there nor at GM with how do you elect or select your next CEO? And so smaller companies have a better, I would think, well, I don't know. I would imagine smaller companies have a better time of that, especially closely held and family held companies. You could, if you can reach the family, you should be able to get some continuity there. 0:46:23.5 Andrew Stotz: So Donald Peterson stepped down early 1995. And when did you guys make or when did you make your transition from Ford to GM? 0:46:38.5 William Scherkenbach: '88. 0:46:39.6 Andrew Stotz: Okay, so you continued at Ford. 0:46:42.1 William Scherkenbach: The end of '88, yeah, and I left GM in '93, the year Dr. Deming died later. But I had left in, in, well, in order to help him better. 0:47:07.8 Andrew Stotz: And let's now talk about the transition over to General Motors that you made. And where did that come from? Was it Dr. Deming that was recommending it or someone from General Motors? Or what... 0:47:21.4 William Scherkenbach: Yeah, Deming spoke with them and spoke with me. And I was a willing worker to be able to go where he thought I could be most helpful. 0:47:41.9 Andrew Stotz: And was he exasperated or frustrated that for the changes that happened in '95 when Peterson stepped down, he started to see the writing on the wall? Or was he still hopeful? 0:47:55.4 William Scherkenbach: No, Deming died in '93, so he didn't see any of that. 0:47:58.9 Andrew Stotz: No, no, what I mean is when Peterson stepped down, it was about '85. And then you remain at Ford until '88. 0:48:08.0 William Scherkenbach: No, Peterson didn't step down in '85. I mean, he was still there when I left. 0:48:14.0 Andrew Stotz: So he was still chairman at the time. 0:48:17.3 William Scherkenbach: Yeah. 0:48:17.6 Andrew Stotz: Maybe I'm meaning he stepped down from president. So my mistake on that. 0:48:20.3 William Scherkenbach: Oh, but he was there. 0:48:24.3 Andrew Stotz: So when did it start... 0:48:25.9 William Scherkenbach: True. I mean, true, he was still there when Deming had died. 0:48:31.3 Andrew Stotz: Yeah, okay. So did the whole team leave Ford and go to GM or was it just you that went? 0:48:39.1 William Scherkenbach: Oh, just me. Just me. 0:48:42.8 Andrew Stotz: Okay. And then. 0:48:44.0 William Scherkenbach: Yeah, because we had set up something that Deming was very pleased with. And so they were, everyone was working together and helping one another. 0:48:59.5 Andrew Stotz: Okay. So then you went to General Motors. What did you do different? What was different in your role? What did you learn from Ford that you now brought to GM? What went right? What went wrong? What was your experience with GM at that time? 0:49:16.5 William Scherkenbach: Well, I've got a, let's see. Remember Bill Hoagland was the person, Hoagland managed Pontiac when Deming helped Pontiac and Ron Moen was involved in the Pontiac. But Bill Hoagland was in one of the reorganizations at GM was head of, he was group, group vice president for Buick, Oldsmobile, Cadillac. And so I went over and directly reported to him and each of the, I mean, Wendy Coles was in, Gypsy Rainey, although Gypsy was temporary, worked for powertrain and Pontiac and still, but powertrain was where a lot of the expertise was and emphasis was, and then Buick and Cadillac and so, and Oldsmobile. So we, and in addition to that, General Motors had a corporate-wide effort in cooperation with the UAW called the Quality Network. And I was appointed a member of that, of that and, and helped them a lot and as well as the corporate quality office, but focused on Buick, Oldsmobile, Cadillac. 0:51:18.6 Andrew Stotz: And then tell us about what was your next step in your own personal journey? And then let's now get into how you got more involved with Deming and his teachings and the like. 0:51:32.8 William Scherkenbach: Well, I mean, he would be at GM two and three days a month, and then every quarter he'd be here for, just like Ford, for a four-day seminar. And while at Ford and at GM, I took uh vacation to help him as he gave seminars and met people throughout the world. Even when he was probably 84, 85, I can remember, well, one of the, he always, not always, but he would schedule seminars in England over the Fourth of July because the English don't celebrate that, although he said perhaps they should, but right after the Ascot races. And so he would do four-day seminars. And on one case, we had one series of weeks, the week before Fourth of July, we did a four-day seminar in the US and then went to London to do another four-day seminar. And he went to South Africa for the next four-day seminar with Heero Hacquebord. I didn't go, but I went down to Brazil and I was dragging with that, with that schedule. So he was able to relish and enjoy the helping others. I mean, enjoy triggers a memory. We were at helping powertrain and Gypsy was there, Dr. Gypsy Rainey. 0:53:59.2 William Scherkenbach: And she, we were talking and goofing around and he started being cross at us. And Gypsy said, "Well, aren't we supposed to be having fun?" And Deming said, "I'm having fun." "You guys straighten out." Enjoy, enjoy, enjoy, yeah. 0:54:40.6 Andrew Stotz: And for the typical person to imagine a man at the age of 80, 85, traveling around the world. And it's not like you're traveling on vacation in London, you're walking into a room full of people, your energy is up, you're going and it's not like he's giving a keynote speech for an hour, give us a picture of his energy. 0:55:09.5 William Scherkenbach: And over in London, it was brutal because the hotel, I forget what hotel we're in. When he started there, I think it was Dr. Bernard that he wanted to help. And Bernard wasn't available. So he recommended Henry Neave. And so Henry was a good student, a quick learner. So he helped on a few of them. And I can still remember, I mean, the air, it was 4th of July in London and the humidity was there. There's no air conditioning in the hotel. I could remember Henry, please forgive me, but Henry is sitting in his doorway, sitting on a trash can, doing some notes in his skivvies. And it was hot and humid and awful. But so it reminded Deming a lot of the lectures in Japan in 1950, where he was sweating by 8 AM in the morning. So, yeah. 0:56:30.6 Andrew Stotz: What was it that kept him going? Why was he doing this? 0:56:39.5 William Scherkenbach: I think he, again, I don't know. I never asked him that. He was very, to me, he was on a mission. He wanted to be able to help people live better, okay, and take joy in what they do. And so he was, and I think that was the driving thing. And as long as he had the stamina, he was, he was in, in, in heaven. 0:57:21.1 Andrew Stotz: So let's keep progressing now, and let's move forward towards the latter part of Dr. Deming's life, where we're talking about 1990, 1988, 1990, 1992. What changed in your relationship and your involvement with what he was doing, and what changes did you see in the way he was talking about? You had observed him back in 1972, so here he is in 1990, a very, very different man in some ways, but very similar. How did you observe that? 0:57:56.6 William Scherkenbach: Well, toward the end, it was, I mean, it was, it was not, not pleasant to see him up there with oxygen up his nose, and it just, there had to have been a better way. But Nancy Mann was running those seminars, and they did their best to make life comfortable, but there had to have been a better way to, but I don't know what it was. He obviously wanted to continue to do it, and he had help doing it, but I don't know how effective the last year of seminars were. 0:59:01.1 Andrew Stotz: Well, I mean, I would say in some ways they were very effective, because I attended in 1990 and 1992, and I even took a picture, and I had a picture, and in the background of the picture of him is a nurse, and for me, I just was blown away and knocked out. And I think that one of the things for the listeners and the viewers is to ask yourself, we're all busy doing our work, and we're doing a lot of activities, and we're accomplishing things, but for what purpose, for what mission? And I think that that's what I gained from him is that because he had a mission to help, as you said, make the world a better place, make people have a better life in their job, and help people wake up, that mission really drove him. 0:59:57.8 William Scherkenbach: Yeah, and it, it really did. But for me personally, it was just not pleasant to see him suffering. 1:00:09.6 Andrew Stotz: And was he in pain? Was he just exhausted? What was it like behind the scenes when he'd come off stage and take a break? 1:00:18.7 William Scherkenbach: Yeah, yeah. 1:00:20.8 Andrew Stotz: And would he take naps or? 1:00:23.2 William Scherkenbach: In the early days, we'd go to, well, at Ford and GM, we would go out to dinner just about every night and talk and enjoy the conversation. We'd, my wife Mary Ellen, went many, many times. He enjoyed Northville, some of the restaurants there, and enjoyed the Deming martinis after the meetings at the Cosmos Club. So very, very much he enjoyed that, that time off the podium. So, but he couldn't do that in the, in the later years. 1:01:28.7 Andrew Stotz: And let's now try to understand the progression as you progress away from General Motors and did other things. How did your career progress in those years until when you retired or to where you are now? Maybe give us a picture of that. 1:01:51.4 William Scherkenbach: I tried to help. I've developed my view on how to operationalize change, worked for, was vice president of a company in Taiwan, spent a couple of, and before that had helped Dell, and would spend probably ending up a couple of years in PRC and Taiwan, and growing and learning to learn, in my opinion, there's too much generalization of, well, Asians or Chinese or whatever. There are many, many subgroups, and so change has to be bespoke. What will work for one person won't work for another. For instance, trying to talk to a number of Chinese executives saying, drive out fear, and they will, oh, there's no fear here. It's respect. And so, yeah. But that was their sincere belief that what they were doing wasn't instilling fear. But it broadened my perspective on what to do. And then probably 10 years ago, my wife started to come down with Alzheimer's, and while we lived in Austin, Texas, and that I've spent, she died three years ago, but that was pretty much all-consuming. That's where I focused. And now it's been three years. I'm looking, and I'm a year younger than Deming when he started, although he was 79 when he was interviewed for the 1980 White Paper. 1:04:36.3 William Scherkenbach: So I'm in my 80th year. So, and I'm feeling good, and I also would like to help people. 1:04:46.6 Andrew Stotz: And I've noticed on your LinkedIn, you've started bringing out interesting papers and transcripts and so many different things that you've been coming out. What is your goal? What is your mission? 1:05:02.3 William Scherkenbach: Well, I also would like to take the next step and contribute to help the improvement, not just the US, but any organization that shows they're serious for wanting to, wanting to improve. On the hope, and again, it's hope, as Deming said, that to be able to light a few bonfires that would turn into prairie fires that might consume more and more companies. And so you've got to light the match somewhere. And I just don't know. Again, I've been out of it for a number of years, but I just don't know. I know there is no big company besides, well, but even Toyota. I can remember Deming and I were in California and had dinner. Toyoda-san and his wife invited Deming and me to a dinner. And just, I was blown away with what he understood responsibilities were. I don't know, although I do have a Toyota Prius plug-in, which is perfect because I'm getting 99 miles a gallon because during my, doing shopping and whatever here in Pensacola, I never use gas. It goes 50 miles without needing to plug in. 1:07:00.6 William Scherkenbach: And so I do my stuff. But when I drive to Texas or Michigan, Michigan mostly to see the family, it's there. But all over, it's a wonderful vehicle. So maybe they're the only company in the world that, but I don't know. I haven't sat down with their executive. 1:07:26.4 Andrew Stotz: And behind me, I have two of your books, and I just want to talk briefly about them and give some advice for people. The first one is The Deming Route to Quality and Productivity: Roadmaps and Roadblocks, and the second one is Deming's Road to Continual Improvement. Maybe you could just give some context of someone who's not read these books and they're new to the philosophy and all that. How do these books, how can they help them? 1:07:58.8 William Scherkenbach: Well, the first book, Deming asked me to write in, I think it was '84. And I don't remember the first edition, but it might be '85, we got it out. But he asked me to write it, and because he thought I would, I could reach a different audience, and he liked it so much, they handed it out in a number of his seminars for a number of years. So. 1:08:40.7 Andrew Stotz: And there's my original version of it. I'm holding up my... 1:08:47.0 William Scherkenbach: Yeah, that's a later version. 1:08:49.7 Andrew Stotz: And it says the first printing was '86, I think it said, and then I got a 1991 version, which maybe I got it at one of the, I'm sure I got it at one of the seminars, and I've had it, and I've got marks on it and all that. And Deming on the back of it said, "this book will supplement and enhance my own works in teaching. Mr. Scherkenbach's masterful understanding of a system, of a process, of a stable system, and of an unstable system are obvious and effective in his work as well as in his teaching." And I know that on Deming's Road to Continual Improvement, you do a good amount of discussion at the beginning about the difference between a process and a system to try to help people understand those types of things. How should a reader, where should they start? 1:09:42.8 William Scherkenbach: Well, not with chapter six, as in CI Lewis, but well, I don't know what... I don't remember what chapter six is. As I said, the first book, and a lot of people after that did it, is essentially not regurgitating, but saying in a little bit different words about Deming's 14 Points. What I did on the first book is arrange them in the order that I think, and groupings that I think the 14 Points could be understood better. The second book was, the first half was reviewing the Deming philosophy, and the second half is how you would go about and get it done. And that's where the physiological, emotional, and all of my studies on operationalizing anything. 1:10:55.4 Andrew Stotz: And in chapter three on page 98, you talk about physical barriers, and you talk about physical, logical, emotional. You mentioned a little bit of that when you talked about the different gurus out there in quality, but this was a good quote. It says, Dr. Deming writes about the golfer who cannot improve his game because he's already in the state of statistical control. He points out that you have only one chance to train a person. Someone whose skill level is in statistical control will find great difficulty improving his skills. 1:11:32.1 William Scherkenbach: Yeah. Well, yeah, I mean, well, you're old enough to know the Fosbury Flop. I mean, for all high jumpers did the straddle in jumping and made some great records, but many of them had difficulty converting their straddle to the Fosbury Flop to go over backwards head first. And that's what got you better performance. So anything, whether it's golf or any skill, if you've got to change somehow, you've got to be able to change the system, which is whether you're in production or whether it's a skill. If you're in control, that's your opportunity to impact the system to get better. 1:12:40.3 Andrew Stotz: Yeah, and this was Dick Fosbury in 1968, Mexico City Olympics, where he basically went in and blew everybody away by going in and flipping over backwards when everybody else was straddling or scissors or something like that. And this is a great story. 1:12:57.0 William Scherkenbach: You can't do that. [laughter] 1:12:58.8 Andrew Stotz: Yeah, and it's a great story of something on the outside. An outsider came in and changed the system rather than an existing person within it. And that made me think about when you talked about Ford and having an outsider helping in the different departments. You know, what extent does that reflect the way that we learn? You know, can we learn internally, or do we need outside advice and influence to make the big changes? 1:13:29.7 William Scherkenbach: Yeah. I mean, we had a swim coach, Higgins, at the Naval Academy, and he was known for, again, following in Olympic swimming. And I'm probably going to get the strokes wrong, but there was no such thing as a butterfly stroke. And he used it in swimming the breaststroke, and supposedly the only criteria was recovery had to be underwater with two hands. But I'm screwing up the story, I'm sure, but Higgins rewrote, rewrote the book by doing something a little bit different or drastically different. 1:14:25.4 Andrew Stotz: I'd like to wrap up this fascinating discovery, or journey of discovery of you and your relationship also with Dr. Deming. Let's wrap it up by talking about kind of your final memories of the last days of Dr. Deming and how you kind of put that all in context for your own life. And having this man come in your life and bring you into your life, I'm curious, towards the end of his life, how did you process his passing as well as his contribution to your life? 1:15:08.1 William Scherkenbach: That's, that's difficult and personal. I, he was a great mentor, a great friend, a great teacher, a great person, and with, on a mission with a name and impacted me. I was very, very lucky to be able to, when I look back on it, to recognize, to sign up for his courses, and then the next thing was writing that letter to the editor and fostering that relationship. Very, very, very difficult. But, I mean, he outlived a bunch of folks that he was greatly influenced by, and the mission continues. 1:16:34.1 Andrew Stotz: And if Dr. Deming was looking down from heaven and he saw that you're kind of reentering the fray after, you know, your struggles as you've described with your wife and the loss of your wife, what would he say to you now? What would he say as your teacher over all those years? 1:16:56.3 William Scherkenbach: Do your best. 1:16:59.0 Andrew Stotz: Yeah, wonderful. 1:17:01.4 William Scherkenbach: He knows, but he knows I know what to do. So, you need to know what to do and then to do the best. But I was, I mean, he was very, he received, and I forget the year, but he was at Ford and he got a call from Cel that his wife was not doing well. And so we, I immediately canceled everything and got him to the airport and he got to spend that last night with his wife. And he was very, very appreciative. So I'm sure he was helping, helping me deal with my wife. 1:17:56.4 Andrew Stotz: Yeah. Well, Bill, on behalf of everyone at the Deming Institute and myself personally, I want to thank you for this discussion and opening up you know, your journey with Dr. Deming. I feel like I understand Dr. Deming more, but I also understand you more. And I really appreciate that. And for the listeners out there, remember to go to Deming.org to continue your journey. And also let me give you, the listeners and viewers, the resources. First, we have Bill's book, which you can get online, The Deming Route to Quality and Productivity. We have Deming's Road to Continual Improvement, which Bill wrote. But I think even more importantly is go to his LinkedIn. He's on LinkedIn as William Scherkenbach and his tagline is helping individuals and organizations learn, have fun, and make a difference. So if you want to learn, have fun, and make a difference, send him a message. And I think you'll find that it's incredibly engaging. Are there any final words that you want to share with the listeners and the viewers? 1:19:08.9 William Scherkenbach: I appreciate your questions. In thinking about this interview, we barely scratched the surface. There are a ton of other stories, but we can save that for another time. 1:19:26.1 Andrew Stotz: Something tells me we're going to have some fun and continue to have fun in these discussions. So I really appreciate it and it's great to get to know you. Ladies and gentlemen. 1:19:36.7 William Scherkenbach: Thank you, Andrew. 1:19:37.7 Andrew Stotz: You're welcome. This is your host, Andrew Stotz, and I'm going to leave you with one of my favorite quotes from Dr. Deming, and that is that "people are entitled to joy in work."

Jul 7, 2025 • 24min
Mapping More of the Process: Path for Improvement (Part 10)
What if you could tackle a persistent problem without guesswork? In Part 10 of the Path to Improvement series, John Dues and Andrew Stotz discuss how John's team uses Plan-Do-Study-Act (PDSA) cycles to calm a chaotic process with precision. Discover how to shift from blame to solutions by leveraging data and Deming thinking. You'll also find out where the team stands on their path to reducing chronic absenteeism in their schools. Listen now! #EducationLeadership #ContinuousImprovement #SystemsThinking #DemingInEducation TRANSCRIPT 0:00:02.2 Andrew Stotz: My name is Andrew Stotz, and I'll be your host as we dive deeper into the teachings of Dr. W. Edwards Deming. Today I'm continuing my discussion with John Dues, who is part of the new generation of educators striving to apply Dr. Deming's principles to unleash student joy in learning. The topic for today is mapping the process, part two. John, take it away. 0:00:23.5 John Dues: Hey, Andrew. It's good to be back. Yeah, we've now been talking about our efforts to improve chronic absenteeism for several episodes. And we've talked about two Plan-Do-Study-Act or PDSA cycles focused on where we were working with specific students and their families regarding obstacles to getting to school. And then we shifted gears, and we started running this PDSA cycle three that we talked about last time. And just as a refresher for listeners, the objective of PDSA three is to create a process map, basically. And the goal for the process map is to standardize our attendance intervention system. And I think one of the things that comes to mind when you sort of work on process maps or on important processes is this quote from Dr. Deming. He said, If you can't describe what you're doing as a process, you don't know what you're doing, which is pretty convicting when you really think about it. I think a lot of people initially will say, No, no, no, I know exactly what our process is. And then you say, Well, write it down, map it. And then it becomes much more apparent that most people most of the time have a very rough version in their head that they can't translate into an actual written process. 0:01:44.8 Andrew Stotz: And I'm curious why that is, because on the one hand, when I've done mapping a process, you end up with, Okay, but then there's this exception, and then there's this. And oh, yeah, but don't forget that. So there's like all these intricacies. That's one reason. And then there's another reason is why is that someone's tunnel vision on I know the process because I know the three parts of the process that I'm working with. Why do you think it's hard for people to understand the whole process? 0:02:11.9 John Dues: Well, I think that first reason is probably the biggest reason where there's when they actually start mapping it, there's all these things that they initially left out. And I think as soon as an organization gets to a certain number of employees and has a certain amount of complexity, or you have to add a person that's now going to do part of what you previously did because your role changed or something shifted, needs change, or whatever in the environment. And you have to bring them in. You realize pretty quickly that you can't rely on that stuff that lived in your head anymore. So I think it's a combination of all those things for why this becomes so important. And the other reason I mean, the reason you want to do this is so that there's a starting place, a standard place where people are working from so that whatever it is that the focus is that it can be improved. It's hard to do that when there's no set process to start with. 0:03:08.5 John Dues: Let me. I'll share my screen and just kind of as a refresher, take a look at some of that data that we've talked about so far on this chronic absenteeism front. So, you'll remember that we have this long range goal to improve chronic absenteeism. We've kind of talked about where we are now, where we want to be. So where we are now is in that sort of 40 to 50 % range in terms of chronic absenteeism. We want to be down in under 5%. We have eight years of data going back to the 16-17 school year. And the other thing we've talked about on the data front is that really we have this pre-pandemic world and this post-pandemic world when it comes to chronic absenteeism. For anybody that's watching, you can clearly see this on the process behavior chart or control chart that's on the screen where prior to COVID, we're sort of humming along around 25% chronic absenteeism, which is still high. But now, since COVID, we've since the pandemic, we've skyrocketed. So there's this clear, sort of, new reality, new system for schools like ours that... 0:04:23.7 Andrew Stotz: And can you, just for someone that may be just popping in and hearing this, can you just describe what is chronic absenteeism rate? 0:04:31.9 John Dues: Yes, chronic absenteeism is a standard federally defined level of absenteeism where kids are called chronically absent once they've missed 10% or more of the school year. So the percent of kids that are chronically absent is what's being displayed. 0:04:50.5 Andrew Stotz: So if a school has 100 kids, this chart is saying that 50% of them are chronically absent? 0:04:58.9 John Dues: Yes. Yep. 0:05:00.5 Andrew Stotz: Okay. Yep. 0:05:01.1 John Dues: And that's not since the pandemic happened. That's not atypical, especially for schools that serve a high population of students that are economically disadvantaged, basically, unfortunately. So that's the goal, sort of cut it by a significant amount, 40 to 50% down to less than 5%. So that's the goal. And we've looked at the... Last time we looked at sort of the processes that are currently in place. So just as a quick refresher, United Schools, where I work, is a small urban public charter school system. We have four campuses, and there's people from each of the campuses on this attendance improvement team. And what we've been doing lately is sort of mapping out the process that each campus is using. Each campus has their own little process for intervening with kids that are chronically absent. They have different people that are doing different parts of that process. And so we started with just saying, what is it that your process looks like? 0:06:09.3 John Dues: And we looked at a couple of those maps. So this first map is from one of the campuses. It's pretty simple. There's just one or two people involved. The way they represented it initially is just maybe 10 or 15 steps that they're going through to sort of identify who's having attendance issues, sending letters to families, contacting families, that type of thing. But you can see, initially, at least as they mapped it, it's a pretty simple process. And then when we looked at one of our other campuses and they mapped theirs out, it was a slightly more in-depth process. There's sort of more detail. There are more people involved in the process. I'd say there's probably a little more sophistication to sort of when and how they were intervening with parents. And a lot of the intervening is just sort of the compliance requirements. When a kid reaches a certain number of missed hours, we're required to send them a letter to their parents, for example. So a lot of the process currently focuses on sort of the legal requirements when it comes to absenteeism in Ohio's law. But these are two campuses that are about three miles apart, and you can see, even though they're following the same legal sort of requirements from the state, they have very different processes for how that work is being done. 0:07:38.9 Andrew Stotz: Or could you also say that this particular campus, the people involved may have a much deeper understanding of it or a desire to map it out with more detail? Or do you think it's significantly different? 0:07:52.3 John Dues: I think that this second one that looks like it has more steps, I think they have a person that's more of their sort of 1.0 FTEs, like more of their 1.0 FTE is focused on just attendance, whereas it's sort of like a divided responsibility. 0:08:09.7 Andrew Stotz: Wait, what's a 1.0 FTE? 0:08:12.1 John Dues: Like one full-time equivalent person. So a big part of the person's job is this attendance process. So they know this process pretty deeply. So they were able to map it in more detail, basically. So that was interesting. So part of this PDSA cycle three was, so the plan was really had sort of two steps. One, create a standardized process map for the system as a whole that everybody's going to work from. And then, once that's drafted, gather some feedback, both quantitative and qualitative feedback from our network leadership team. So that was the Plan. The Do was just make the map and then gather the input. So that's what's been happening of late with this team. But we can see pretty quickly what they did. And it certainly does help to have an improvement advisor, someone with a deep knowledge of the Deming philosophy and mapping processes, because he's the one at the meetings. He's the one sort of taking everything that the team is telling him, the process maps that the campus teams have done. And then he's putting it all together based at their input. And their input is certainly super important, but he's also very talented at building processes that are coherent and can be understood by many across our system. 0:09:40.3 John Dues: And so what he ended up doing using their input is he's now got a process map that includes not just the nuts and bolts like, okay, the kid has an attendance problem, and we have to send letters and do things like that. He's going back and created a process map that includes four different stages. So this first stage that if you're viewing this part of the process map is just for onboarding, which was completely missing from all of the campus maps. It wasn't on the... So the idea here is the very first thing, the beginning of this process is a new student enrolls. And as soon as they enroll, a family enrolls, there's going to be a number of things that happen, mostly on the educational side, like what is good attendance? So right from the get-go, one of the things they're going to do is they have this welcome folder that a family gets when they come for their tour or their orientation. And right in that welcome folder is going to be our attendance framework that defines what good attendance is and when, where it really starts to become an issue and impacts a kid's education. So this whole first process map, this whole first stage is about onboarding and educating the family and the student about what good attendance is, which was, again, completely missing from the process before. 0:11:10.2 John Dues: The second stage is attendance monitoring. So, the kid's been onboarded, school has started, and now there's a process to monitor every student's attendance, whether they have a problem or not. And this monitoring system is going to be standardized so that different notifications are being sent home to families, different sort of letters, letting them know when things are becoming a problem. So again, this whole process is about monitoring attendance after providing some of that education. And then, if through that monitoring, it becomes apparent that the student needs additional intervention, the next stage is sort of that attendance intervention plan. So this is where the full map before for each campus just focused on this part. And this is obviously, if you look at this compared to the campus maps, this is much more in detail about what's happening. I'd say, the other thing that's happening here is there's problem-solving with the family. So instead of just saying, warning, your kid has gotten to this number of missed hours, and you send that home in a letter, once that happens, you can see that there's actually Plan-Do-Study-Act cycles being run with the family and the student that are off track from attendance perspective and some individual problem solving is happening. 0:12:52.3 John Dues: See, we run three PDSA cycles to try to get them back on track. So that's a brand new component to this attendance system. And then from there, for some kids, if we get them back on track, then we don't have to take any further action. But for other students, there are some, again, some legal requirements. And so the last stage of that process is if we do have to file official truancy charges, sort of like what, or let the state know that the student is now truant, there's some steps that we take to make that filing. But that's far after many, many steps have been taken to educate, to run PDSA cycles with individual kids that are off track, to try to get the family and sort of the knowledge they need to understand, like how to keep their student on track when they're in school. So, there's a good chance that this will change pretty quickly, this process map, it's a good one, I think, having gone through it, it's a solid process, but it'll, as soon as it like gets battle tested, there's going to be updates. Now, that's not say you're going to change things willy nilly, but what you are going to do is you're going to learn what's working, what's not, you sort of have this hypothesis, but at least now, since everybody's working from the standard process, we can make improvements that then can go out to the entire system. 0:14:32.9 Andrew Stotz: Great. I'm curious, what is the definition of truancy these days? When I was in school, there was trouble in River City and it was trouble with a capital T and that rhyme with P and that stands for pool. So you had the trouble of all the kids hanging out at the pool place, but I'm just curious what's going on. What is the definition of truancy these days? 0:15:01.3 John Dues: Yeah, it's when they, I mean, students have to have missed a certain number of hours of instruction. And now instead of attendance being measured in days, there's basically a threshold that you hit in terms of numbers of hours missed that then you legally have to file truancy. 0:15:24.4 Andrew Stotz: But what does truancy mean? 0:15:27.3 John Dues: Truancy just means that you've missed a lot of school, basically. 0:15:31.1 Andrew Stotz: Okay. 0:15:31.4 John Dues: Yeah. Yeah. And in terms of reasons, when we did those first PDSAs, not all those kids were necessarily truant, but they all had serious absenteeism issues. I think what we talked about was that we found that there were many different issues that were sort of at the root of that, which is part of the challenge here is we have high numbers of chronic absenteeism and then lots of different reasons for that. And so how do you problem solve with all those different folks to help get them back on track? That's part of the challenge. For sure, part of the challenge. But so where the team is at now, so they've completed this third PDSA cycle. So the Do was to make the process map and then get the input from the leadership team. And now they're doing the Study and the Act. So the Study, one of the things I talked about was that the initial feedback from folks that aren't a part of the team was more education needed to happen during that onboarding process. 0:16:39.9 John Dues: So that was sort of like a blind spot before. Not that people didn't talk about it, but now it's systematized. Here's the piece of paper, the attendance framework you're going to give them. There's an orientation session on attendance. There's a session with students during their orientation about what's good attendance and how many days does that equate to in terms of missing school throughout the year, that types of things. Another big thing in the study was more personal touches throughout the process and not just sort of those notifications that I talked about, like the attendance warning letters. The group sort of talked about, while some of these letters are required, whether they're that effective or not is definitely in question. 0:17:25.1 John Dues: Another thing is we have a role at each campus that's called Dean of Family and Community Engagement. And so something like attendance is the responsibility of everybody in the school. But if there's a point person at each campus, it's that Dean of Family and Community Engagement. And so there's some worry about, like when I go back to this process, it's the Dean of Family and Community Engagement or DFCE, they're sort of the point person running these PDSAs and the PDSAs can be time intensive. So one of the concerns is, will they be able to sort of handle the workload that sort of comes with this new process? And I think that's definitely an open question, but at least it's on the radar. It's not like no one is saying, here's the process, go figure out how to make this work. That would be a bad way to do it. There's a recognition that we think we need to do some of this problem solving with individual cases, but there's also this recognition that there's going to be a time constraint for the DFCEs. And then another big X factor that was a part of this study write-up was transportation. Because we've talked about how bad transportation, yellow school buses have been in Columbus this year. We've had a lot of problems. And so what's that look like next year, and how does this factor in? When we did those interviews with students and families, it wasn't the primary reason for all families, but I think in about 50% of the families, transportation had some role in the attendance issues. So these are things that are on folks' minds as they're working through this. 0:19:06.5 Andrew Stotz: That's a lot of progress on this. 0:19:09.3 John Dues: Yeah, a lot of progress, I think. And you get questions like, is it worth all the time to do this? And it's like, is this improving anything? And if you're looking at the outcome, probably not yet. But now that there's this standardized process, I think we can actually make some inroads on this chronic absenteeism process. It would be very hard to do in the absence of this standardization that we're going through and this input from the group to put more sort of resources towards this to get some expertise in terms of putting together a process instead of leaving it up to individual people that maybe don't have this skill set. 0:19:53.9 Andrew Stotz: You also recently posted on your LinkedIn about the idea of a system and results. If you don't even understand the system, how are you going to get the results that you want from the system? 0:20:05.8 John Dues: Exactly. If you don't understand what's causing the problem, if you don't have a whole systems view, you could put a process in place that actually makes things worse, may make things better in one area, but make them worse in another area. So yeah, this is complicated stuff when you're trying to make change in a complex system like a school system. 0:20:25.7 Andrew Stotz: Interesting. 0:20:26.2 John Dues: Yeah, the last step is just the Act. So they're deciding what to do. Are they going to adopt this? Are they going to adapt it or abandon the idea? So I think we're not going to abandon it because obviously we're moving forward with this new process map. And it's, I would call this adapt though. So we're going to adapt this process map into the system, but very high likelihood that there are going to be many adjustments to it as it gets put into action. As I was just saying, it's not adopt because if it was adopt, this thing, this process map would be sort of run through a number of cycles where it had been tested, the kinks had been worked out, and it's sort of going to be, this is the way. So what we're doing now is adapt. So we're going to make some improvements based on this initial feedback we got from the leadership team. Now we'll make some additional adjustments, especially next school year because the school year is over during the initial implementation. 0:21:29.8 John Dues: And the other sort of part of the Act was if you read the steps in this process map from start to finish. There are a lot of artifacts that go along with this that don't exist. So for example, this attendance slide deck for new student orientation. That's a part of the process. We probably don't want to leave that up to each individual group to create on their own because what is the content of that? And so that has to be created. So there are a number of things like that, that the improvement advisor for the project is going to take on either creating himself or he's going to strongly support the creation. So those are also standardized across the network. So you see, it's a lot of work. 0:22:20.4 Andrew Stotz: Yeah. 0:22:22.2 John Dues: So that would be where we pick up with, once students come back in August, and that's kind of leaving things off at the end of this school year. 0:22:31.6 Andrew Stotz: That's great. I was mentioning about this little jingle that I was talking about, and it comes from a 1957 movie called The Music Man. And he says, his line is, there's trouble in River City, and it starts with T, and that rhymes with P, and that stands for pool. And it's this guy, he's a con man, a hustler, who's gone to the citizens of a town in River City, Iowa, telling them that the corrupting influence is the pool table in the town that's going to keep the kids from going to school. And he wants to start like a marching band. But for those old-timers that seen that movie, they'll love that reference. And if you haven't seen it, go see The Music Man on... I don't know. It's hard to find things on Netflix these days like that, but maybe it's on YouTube. 0:23:27.9 John Dues: Very classic, just like that. 0:23:30.2 Andrew Stotz: But I remember listening to that when I was young, because my parents always had musicals. My sisters actually played musicals on the record player. So you always was hearing the songs of musicals. 0:23:43.8 John Dues: Well, it seems like the truancy thing is, that's not a new problem necessarily. 0:23:48.1 Andrew Stotz: Oh, yeah, that's for sure. That's for sure. Well, why don't we wrap it up there? And on behalf of everyone at the Deming Institute, I want to thank you again for this discussion. And for listeners, remember to go to deming.org to continue your journey. And you can find John's book, "Win-Win: W. Edwards Deming, the System of Profound Knowledge, and the Science of Improving Schools" on Amazon. This is your host, Andrew Stotz, and I'll leave you with one of my favorite quotes from Dr. Deming. "People are entitled to joy in work."

Apr 14, 2025 • 29min
Mapping the Process: Path to Improvement (Part 9)
How can we improve attendance when every school has a different process? In this episode, John Dues continues his exploration of Deming’s philosophy in action, focusing on chronic absenteeism. As part of their third PDSA cycle, John’s team shifts from individual interventions to process standardization—mapping how each of their four campuses handles attendance interventions. The surprising discovery? Each school follows a different process, revealing hidden variation and inefficiencies. By visualizing these systems, the team is not only grasping the current condition but also setting the stage for a reliable, scalable, and effective process. This methodical approach highlights how understanding systems and reducing variation are key to meaningful improvement. TRANSCRIPT 0:00:02.1 Andrew Stotz: My name is Andrew Stotz and I'll be your host as we dive deeper into the teachings of Dr. W. Edwards Deming. Today, I'm continuing my discussion with John Dues, who is part of the new generation of educators striving to apply Dr. Deming's principles to unleash student joy in learning. The topic for today is Mapping the Process. John, take it away. 0:00:26.7 John Dues: Hey Andrew. It's good to be back. Yeah. For the folks that have been following along for the past several episodes we've been working towards defining this problem more narrowly in terms of this chronic absenteeism issue we've been talking about. And for the last few episodes we've been talking about how the team didn't have enough information to write that precise problem statement. And we took a look at gathering additional information by running a couple PDSA cycles in those first two cycles that we've discussed so far. We know we had zeroed in on a handful of students and ran PDSAs with them and their families about their obstacles getting to school. And then we left off talking about how we were going to shift gears in PDSA cycle three. And instead we were going to focus on standardizing our process. So creating a process map for how we intervene with kids with our attendance teams across the network. So that's what the team is currently working on. But just as a sort of quick reminder to folks, and especially if you're watching, we have this model that we've been working through, this four step improvement model where you set the challenge or direction, grasp the current condition, establish your next target condition, and experiment to overcome obstacles. 0:01:48.1 John Dues: And then like we've talked about several times, we're doing this with the team and that includes people working in the system, people with the authority to change or work on the system, and then at least one person with significant knowledge of the System of Profound Knowledge, like an SOPK coach. And we've been using this model that's on the screen to sort of symbolize or I guess visualize what those four steps look like. You're sort of marching up this mountain towards this challenge or direction. And we've also talked about this long range goal that we've had and we've taken a look at some data where we have our chronic absenteeism rate mapped out over the last eight years or so. We have this long range goal. So this is the direction of the challenge where we're trying to take our chronic absenteeism from above 50% down to 5%. We have the data going back to the 2016/17 school year. Then we also talked about how there's this, not surprisingly, there's this sort of pre-pandemic level of chronic absenteeism, which was again too high. It's not where we wanted it, but we have this major shift up where we've seen this significant jump in chronic absenteeism since the pandemic hit. 0:03:15.0 John Dues: So in those four years, 2020/21, 21/22, 22/23 and 23/24 we were up in the 51, 52, even up into the close to the 60% range in chronic absenteeism at the height of the pandemic. So for PDSA cycle three, really doing two things. So, and we're going to talk about this in the episode today. If you remember back way at the start of this series, we looked at something I called a system flowchart. So we'll kind of revisit that and then we're going to take a look at two process maps that were created by two of our school teams to sort of map their current process. And then we'll walk through, sort of we'll take that, we'll walk through what the plan is for this PDSA cycle three. So let's start by looking back at this system flowchart. I'll sort of reorient you to this. So we have up on the, and this is the current state. So up on the top we have the target system which is attendance. And then we have this aim that is sort of a three part aim. 0:04:42.7 John Dues: We want to define strong attendance for students and staff, make sure everybody's on the same page. We want to ensure that students, families and staff have a shared understanding of what it means to have strong attendance. And then we are working on improving and creating systems that identify and remove barriers to strong attendance for students and staff. And then over on the left hand side we have sort of inputs. So these are things that contribute or their conditions that impact our system. And then in the middle we have our core activities. So the things that are happening that impact attendance and then there's outputs, both negative and positive outputs that come out of this system. And then we get feedback from our customers, we do research on this feedback and then we make design if it's a new system or redesign if it's a current system. And some of these things, some of those contributing conditions are, Ohio has a set of transportation laws. You know, there's our school model and our the way we operate our school hours, our expectations regarding student attendance, our various intervention systems, neighborhood dynamics, how far our families live from school. 0:06:03.4 John Dues: These are all things that contribute to our sort of inputs into our system. And then we have these core activities. And remember, we could just zero in on attendance systems. But there are many other parts of our system that impact whether or not kids come to school. So for one, many of our families are always going to be new to our system. So for example, in our middle schools, where they start with sixth grade some number of those kids are going to be from our elementary schools. Some number of those kids are going to come from other neighborhood schools, but they're all going to be new to that middle school. So whether they're coming from our elementary school or not, you have to think about how is the student and family being onboarded to our system. Another thing we're looking at is school culture and trust. You know, how much trust is in there, in the school. Do they have a strong culture between teachers and families or teachers and students, or the principal and teachers? Then there's academic systems how engaging are classes, those types of things. 0:07:05.7 John Dues: Then we have the attendance intervention systems, which is obviously a core focus. We have health and wellness and changes around mindset since we went through the pandemic. And then finally the third sort of, or sorry, the third, not the third, but the sixth core activity that we talked about was transportation. So we've talked about lots of problems with our busing system this year. So that's another thing that has a big impact on attendance. And so what this group, again is working on the core activity is the attendance intervention systems. What's the process for that? But I had mentioned in an earlier episode that we have another group that's working on transportation and busing and how we can improve that. So the whole point of the system flowchart is there's many, many things that go into something like an attendance rate. And many of these things are very challenging. Some are largely out of our control, but much of it is largely in our control. And we're trying to pull the levers that we think are most important when it comes to student attendance. 0:08:09.2 Andrew Stotz: And just one thing on that, one of the things I just find so frustrating and it's part of this class I'm teaching tonight is how do we scale a business. And one of the ways that's critical to scaling is simplifying. And sometimes, like, when I look at all of this complexity, on the one hand, you're like, okay, well, that's our job, right? Our job is to manage complexity. And that's the reason why we don't have a thousand competitors coming in, because it's complex and it's difficult. And on the other hand, it's like the simplifier in me is like, how do we simplify this? You know, like, I'm just curious about how you see complexity versus simplification. And in particular, it may just be in this stage, you're just putting everything up there, and it's just overwhelming. Like, oh, my God, there's so much involved in just fixing one thing, you know? What are your thoughts on that? 0:09:11.5 John Dues: Yeah, that's, I mean, that's a really good question. It's, I mean, I think it is a complex system because there's so many moving parts. And I think part of the nature of a complex system versus something like a complicated system is that when you try to impact some part of the system that has these ripple effects into other parts of the system, many of which are unattended or unintended consequences. So, yeah, I mean, I think one thing we have working in our favor is very stable senior leadership. So we're pretty good at understanding how we all work. We have a pretty good historical knowledge of how our school system has worked over time. And we have a pretty good holistic view of all of this complexity. Not that we're all able to improve it all at once, but I think we have a pretty good grasp of what's going on. And even a team like this there we could move faster perhaps, but I think we're trying to be pretty deliberate about the changes that we're making. 0:10:24.7 John Dues: And we're also deliberate about the levers that we're trying to pull for improvement. And these things change over time. So even something like transportation, I mean, the reason that we're working on that now and that we've chosen to work on that now is because the transportation that we're getting from the district is so untenable. Whereas 15 years ago, when I was a principal in our system, while the busing wasn't perfect, it was pretty consistent. You know, most days it dropped off at about the same time. It picked the kids up at about the same time every day. And while it was nowhere near where you would want it to be overall, it wasn't my biggest pain point as a principal. Now kids are literally missing hours or buses aren't showing up at all. And so we have to figure out a way to make this work. And to your point this was a system when charter schools were set up in Ohio, is just basically like the district, the nearby district, which is usually a big urban district, is going to do the busing for charter schools. 0:11:35.5 John Dues: And there really wasn't any more thought to it than that and so from the district's perspective, they they have to manage a lot of complexity. They have their own schools, they're busing for charters, which there's about 15,000 kids in charter schools in Columbus. And then they're also busing for private schools. And the district itself still has a very large geographic footprint, even though the number of students that attend there are about half what it was 50 years ago. So they have very spread out buildings, some of which are far below capacity, but they still have students attending them. So they haven't shrunk that geographic footprint. So that's a challenge as well. And at a time when it's become very difficult to find bus drivers. So I don't take lightly, like the challenges that the district is facing in this, but we got to get kids to school as a... Just as a basic starting point to be being able to do school well. 0:12:31.8 Andrew Stotz: Okay, keep going. 0:12:33.8 John Dues: I mean, it's also a really good segue. We'll take a look at a couple of the process maps. So we have our four campuses. We have something different going on. So even though our four campuses are geographically pretty proximate to each other, they have four different processes going on with their attendance intervention system. So take a look at this first process map, which is pretty simple from start to finish. What is that? 1, 2, 3, 4, 5, 6, 7, 8, 9. It's really nine steps and it really... 0:13:08.6 Andrew Stotz: And for the listeners out there that can't see it, he's got a process map, State Street. And what it shows is some circles and some squares and some tilted squares. I don't know what those are called. 0:13:23.5 John Dues: Yeah, I mean, it's just the circles are the start and end points. 0:13:26.9 Andrew Stotz: Okay. 0:13:27.8 John Dues: The squares are the steps in the process. And then the diamonds are, when there's a... Some decision has to be made in the process. 0:13:37.0 Andrew Stotz: Okay, great. 0:13:38.0 John Dues: So we're not going to go through all of these steps. But if you are watching this is a pretty simple process at one of our campuses, while there are multiple people sort of involved, it's also true that one person is driving a lot of this work. But the point is, especially for people that are watching, when you sort of walk through these 10 steps, you're going to see that this map is going to look very different and less complicated than the map at one of our other campuses. But the point is, especially if you can see things visually that you can tell just by looking at the two maps, there are two very different processes going on. And these two schools, this first one is actually an elementary school that feeds into the middle school. That is the map that we'll look at second, so this is the first process map. And then when we look at the second map, we can see very quickly, just visually speaking, there are far more steps, it's far more complicated. There's far more decision points. There's a lot more detail here, and there's a lot of interfacing between multiple people that all play a role in this particular process. 0:14:55.4 John Dues: And it's not that one is right and one is wrong. It's just that when you have these two campuses doing it differently, there very likely is inefficiencies. 0:15:06.8 Andrew Stotz: And are they mapping the same thing? And they... 0:15:10.6 John Dues: Yes, it's the same process. It's how they intervene as the state requires for kids that have some type of attendance issue. And there's different thresholds that mean different parts of the process kick in as a result. But they're operating within the same state process that you have to follow. But even so, you can see that they have a very different sort of illustration of what that process looks like. And if I had the other two campuses, we'd have four separate versions. And remember all these steps and you know, all these decision points. There's documents that exist. There's meetings that happen. There's agendas for those meetings. There's agendas for meeting with parents. There's letters that have to be mailed. And so you can imagine if everybody is creating separate forms, separate meeting agendas, keeping this information in different ways. There's probably a way to design this that's far more effective and efficient by pulling from the four different processes to create one process. And oh, by the way, if you do that, it makes training easier for anybody new that's going to take on some of the clerical roles or some of the interfacing with parents. 0:16:26.9 John Dues: And then if you have one process that you're working from, then you can also share best practices as they emerge as you're working. But if you have four variants, it's much harder to share that information. 0:16:43.4 Andrew Stotz: And you know, it's questionable whether this is a core function. It is an important process. Is it the core? 0:16:54.8 John Dues: Yeah, I mean, I would say it's a, I guess depending on how you define core. I mean, it's a required process. It's a process that the state requires and a lot of the sub steps are required components. Now, interestingly, this, the setup for this attendance intervention system came out of some legislation called Health...House Bill 410. And it's been in place for maybe five years or so, four or five years. And they're changing it right now. So there's new language. 0:17:30.2 Andrew Stotz: Just when we got it set. 0:17:32.2 John Dues: Just when we got it set. But we at least know the likely changes that are coming. So Ohio operates on a two year budget cycle. So in this new budget that will likely pass on. Well, it has to pass by June 30th. Right now there's language in there that changes this process for schools and actually gives schools way more leeway. So we'll sort of be ahead of the game because we're going to have our own process mapped and you know, we can remove some of those things that are a little more cumbersome on the school teams. And to your point, those things that were compliance related but didn't have really impact on improving attendance, we could just remove those now. We'll have some more freedom there. 0:18:13.8 Andrew Stotz: I mentioned about the core thing because there's a great book I read called Clockwork by Michael Michalowicz and he talks about identifying what is the core function in your business and then really focusing in on that. And it's interesting because one of the benefits of that is that if you don't do that, you can get caught up in every process like, and then all of a sudden it's just everything is seen as equal. 0:18:43.6 John Dues: Right. Yeah. 0:18:44.6 Andrew Stotz: Anyways, keep going. 0:18:45.9 John Dues: Yeah, it's one of those weird things and I'll stop sharing. Yeah, that was the last visual. But that's one of those things where like I said for the last five years or so these things have been required. And I think you'd be hard pressed to find a school system that would say these, the way things are outlined as requirements for schools to do on this front are not effective but people do them because they're required. And you know, I think with this updated language, we'll have some more flexibility to do this how we want to do it. 0:19:20.4 Andrew Stotz: And how does this, just to clarify how it fits into that mountain diagram, this is trying to assess or deal with the obstacle or is this the current state? I noticed that it said current state for the process map. But is the purpose of what you're... The original one you show. But is the purpose of what you're doing trying to overcome the, identify and overcome the obstacle? 0:19:46.8 John Dues: Well, I would say this is a part of grasping that current condition. You know, we did that early on in terms of that system flowchart, in terms of what the whole system looks like. And now what we're doing is learning about the processes at each individual school. Well, I'd say when you map out a process like this, and I think people would probably, my guess is, is that senior leaders would often say, well, no, we have a process and you know, everybody follows the same thing. And then if you actually mapped it like that, step by step, what you would see is tons of variation, tons of variation. 0:20:23.9 Andrew Stotz: So one of the benefits of that is it's not only, it's about facing the reality or understanding the true current state. Like everybody can say, no, no, no, we all know what the current situation is. No, we don't. 0:20:41.2 John Dues: No, you don't. And every time I sit with a team and make these process maps, we'll say, okay, what's the next step? And you know, maybe a couple people will pipe up and then someone inevitably goes, well, no, wait a second, that's not what we do. What we do next is X, Y or Z. I mean, it's... And that happens over and over and over again with this with this process just seems to be a part of it. It's not a bug. It's actually a feature of this mapping exercise. 0:21:08.5 Andrew Stotz: And many people try to solve these problems by just jumping in rather than taking the time to really, truly understand the current state. You know, what's the risk of the action taker? 0:21:22.7 John Dues: Well, yeah, I mean, I think what happens a lot of times is like when people don't really understand a process like this is they start blaming people for things that aren't going right. That's what typically happens. 0:21:35.8 Andrew Stotz: I want people to take responsibility around here. 0:21:38.3 John Dues: We have to hold people accountable, but you can't hold them accountable to a process that's unknown. Right. It's not well specified, but that's what typically happens. So, so yeah, so the objective for this PDSA cycle, so we're on this third cycle. So those first two were focused on talking to individual kids, interviewing with individual kids. And we said well let's actually look at our process for how we're intervening from a school perspective as a team at each of the schools and let's standardize that process. 0:22:13.1 John Dues: So that's what we're doing. We're sort of mapping it from start to finish, gathering feedback from key stakeholders as we sort of map a standardized process that works across all four schools. And really one of the things that we're doing right now is we're saying can we develop a process? And we have these four dimensions that we're looking for to sort of meet. One is functional, one is, is it reliable? Third, to your point about the business talk you're giving tonight is is it scalable? You know, does it work across the entire school and across the entire school system? And then is it effective? And we're basically, the attendance improvement team basically is going to put together the process and then they're going to put it in front of our senior leaders and we're going to rate sort of the process across those four dimensions and they've sort of predicted what they think is going to, how it's going to hold up when it's sort of tested by those senior leaders. 0:23:12.8 John Dues: So that's kind of what we're doing right now. So step one is mapping the four campuses and then we're going to map one standardized process, at least a rough draft. And again, so once that initial network wide or system wide map is created, we're going to put it in front of that senior leadership group. We're going to give them a brief survey, sort of a Likert scale across those four dimensions and see, see what they think basically. So that's our next step right now. 0:23:40.6 Andrew Stotz: Exciting, exciting. I want to tell a little story to wrap up my contribution here and that is after many years of living in Asia, I started to realize that everything's connected in Asia, people are connected. If you want to be mean to somebody, it's going to come back around to you. And if you want to push on somebody, it's going to come back around because everybody knows everybody. And I like to picture it like a circle. Let's just say a bunch of people in a circle facing the same direction. And then let's say they all put their right arm on the right shoulder of the man or woman in front of them. So now we have a circle that's connected in such a way. And if you think you're going to get something done by squeezing on the shoulder of the person in front of you, the problem you're going to face is that that's going to transmit all the way around the circle until all of a sudden you're going to be squeezed. And that is my visualization of the way influence works in Asia. Yeah, but I feel like it's the same type of thing when you just say, I want to hold people accountable and we need responsibility around here. 0:24:57.8 Andrew Stotz: What ends up happening is that the only choice that someone has is just to squeeze on the person in front of them. And when they do that, it just transmits a squeeze all the way around. It builds fear, it builds distrust and all of that. And so that. That was a visualization I was having when you were talking. 0:25:16.4 John Dues: Yeah, I mean, I think... And it can be convicting a little bit there. There's a Dr. Deming quote that I'll share to sort of wrap this. Before I do that, I think again, I go back to we... There are these unknown things about how to improve attendance. And so this PDSA, this plan, do study, act cycle, we're using one, again, was intervening with kids and trying to work with a handful of kids that had attendance issues and just see what works and what doesn't. We've shifted gears in this third cycle to something very different. But this is all part of one comprehensive effort by this team to put this new system in place. And all of these pieces of information are important, but this and this mapping, the process thing I think is a great... And I think maybe a lot of people wouldn't think about that as a PDSA to plan a new process, but you can absolutely use it in that way. But the Dr. Deming quote that I think of when I do process mapping is "if you can't describe what you're doing as a process, you don't know what you're doing." 0:26:21.7 John Dues: And I think that's true. Again, it's not to convict people, but I think often when we say, well, that's this thing is going wrong, we need to hold people accountable. And then you ask that person that's making that claim, well, what is the process for this thing? And they often can't tell you. Or they do, it's so vague that nobody could. 0:26:45.3 Andrew Stotz: Or they say, that's not my responsibility. My responsibility is to hold you accountable for getting the result. 0:26:51.4 John Dues: Right. Yeah. And, and, and many people, many organizations don't write these things down. You know, they don't write them down and share them with folks. So that's just some of these simple things are as part of the power making things exciting. 0:27:05.1 Andrew Stotz: Exciting. Well, yeah, how about we wrap it up there and so what are we going to get next time? 0:27:10.7 John Dues: Yeah, I think so. What we went through quickly here at the end was the plan for this PDSA cycle. So by the time we get back together, will have the process map for the system and we'll have had the feedback back and we'll be able to compare that to what the group predicted. 0:27:28.8 Andrew Stotz: So ladies and gentlemen, we're watching it in real time unfold the applications of Dr. Deming's principles. And isn't that what we want? You know, obviously we love theory and we love ideas, but we really need to be all thinking about how we apply these things. And so from my perspective, I'm really enjoying this series and I'm learning a lot. And as I mentioned before, I've been improving some of my thinking and some of my teaching in particular, based upon the discussions that we've had. So on behalf of everyone at the Deming Institute, I want to thank you again for this discussion and for listeners remember to go to deming.org to continue your journey. And also you can find John's book, Win Win: W. Edwards Deming the System of Profound Knowledge and the Science of Improving Schools on Amazon.com This is your host, Andrew Stotz. And I'll leave you with one of my favorite quotes from Dr. Deming. I know you've heard it before, but I'm going to say it again. Until we have joy. "People are entitled to joy in work."

Apr 7, 2025 • 1h 4min
Getting Started with Quality as an Organizational Strategy: A Conversation with Cliff Norman and David Williams
Why would any leader choose to take on a transformation that requires rethinking how they lead, how their organization functions, and how they learn? In this episode, we dive deeper with Cliff Norman and David Williams, co-authors of Quality as an Organizational Strategy, exploring Chapter 11: “Getting Started.” They share powerful stories, practical steps, and the deep-rooted challenges leaders face when shifting from conventional methods to building true learning organizations grounded in Dr. Deming’s philosophy. This conversation highlights why improvement cannot be delegated, why leadership transformation is essential, and how to begin the journey—with clarity, commitment, and courage. TRANSCRIPT 0:00:02.1 Andrew Stotz: My name is Andrew Stotz and I'll be your host as we dive deeper into the teachings of Dr. W. Edwards Deming. Today we are going to continue our conversation with Dave Williams and Cliff Norman about their book Quality as an Organizational Strategy. I found this book fascinating because I think it's addressing something where there's been a bit of a hole and that is how do we think about the strategy of our business? And so we already had our conversation in a prior episode about the overview of the book, but today we're going to be talking about specifically, now this is kind of funny because we're going to be talking about the back of the book and that is chapter 11, getting started. Dave, why don't you take it away? 0:00:53.3 Dave Williams: Well, thanks, Andrew. Thanks for having us back on the Deming podcast. So, as you mentioned, part of the way that the book is laid out is that it describes kind of the foundations that are behind quality as an organizational strategy and begins sort of with an introduction that explains a good bit about how Dr. Deming had this provocation of a need for leaders to transform the way that they approach leading organizations. And part of that was to move not just from process based improvement projects, but to start to think about major systems in the organization and to pursue quality as the overall strategy and create a continuous improvement organization or learning organization. And so the book lays some of the foundation behind the science of improvement or behind profound knowledge that underpin the thinking, walks through quality as an organizational strategy, as a method of five interdependent activities. Then at the end it comes back full circle to say, well, this is great, now you've learned about these theories and methods. But a natural question for any leader would be, how do I get started? And one of the first things that we talk about in that section actually is about why leaders would want to do this transformation. 0:02:30.9 Dave Williams: And this actually came from a conversation that Lloyd and Cliff and I had in 2020 where we were talking about getting on this journey of building the book. And we all kind of recognized that this was really, really hard work. And we were curious or we, we didn't have a good answer of what was our theory about why somebody would deviate from the way in which they work today and embark on a transformational change of the way that they approach leadership, the way that they approach organizations. And actually I ended up going on a journey of interviewing a whole host of leaders who had been influenced by Deming, who had been involved in improvement in healthcare, folks like Dr. Berwick and Paul Batalden and Brent James. I interviewed some folks in the UK and other places, like John Seddon, and asked them, oh and I should Blaine Godfrey, who had been the lead of the Durand Institute, and I posed the question, what causes somebody to want to embark on this change? And many people actually had a hard time articulating it. But the answer that emerged, or actually Blaine Godfrey was the one that kind of framed it the best, I think, for us, was a number of things. 0:03:57.7 Dave Williams: Sometimes it's something like a book like this comes out and people read it and it's interesting and new. Sometimes it's an event happens, a patient safety event or a major accident or something of which causes people to have to change or do something different. Sometimes it's a discouragement with a desire that you know you could do better, but you don't have methods or know how to. So there were a host of things that we listed, and those are some of a sample of them that might invite somebody to say, the way that we're working today is not getting us to the level that we want to. And now we want to embark on something different. And we might look to something like quality as an organizational strategy as a method for us to transform the way that we're working and build on the shoulders of Deming's philosophy and the science of improvement and do it differently. 0:04:56.0 Andrew Stotz: And when I look at the book, you guys are bringing together a lot of different stuff. It's not just a Deming book. It's Deming is a part of this, and that's fascinating. One of the questions I have is when we look at, let's say, a business owner, a business leader is looking for answers, as you said, maybe it's an event, maybe it's a discouragement, maybe it's a feeling like we can do better. Maybe it's just being beaten by competitors. They come to a point where they start looking for answers and they find some fantastic books, authors, ideas, consultants, all this and I think about whether that's Peter Drucker or whether that's the Lean movement or whether that's, let's say Taguchi or something like that is the teachings that you guys are talking about - and I'm going to specifically ask about the teachings of Dr. Deming. Is it more or is it more difficult or less difficult to implement than other books or styles or methods that someone's going to come across? 0:06:08.7 Cliff Norman: I have to quote one of my colleagues here who probably knew about more about Deming than anybody in API or all of us combined, that's Ron Moen, who did, I think it was 88 seminars, four-day seminars with Dr. Deming. Dr. Deming once told him, he said, Ron, I believe you've been to more of these and I've been to. And it's kind of a joke. He had a great sense of humor. But you know, Ron told me the problem with Deming is he's asking us to change. And there's all sorts of things out there that require the management and the leadership, they really don't have to do anything different. And there are several things out there. In fact, Philip Crosby, one of the three gurus during when they launched, he was more the evangelical and had a way of talking to management so that they understood it, which that was his contribution to all that. But when Six Sigma came up and black belts and all that, and Crosby looked at him and says, that's not going to change the system. He said, all you're doing is killing a bear for management, killing a bear for management, and then you'll get a black belt. 0:07:19.9 Cliff Norman: You know, And I thought, wow that's pretty profound. Because the management at that point doesn't have to do anything, just have the black belt ceremony. There's absolutely no change on their part. Where Deming, as Ron says, he's kind of a pain. You've got to learn about variation, you got to learn about Shewhart charts. You've got to be able to put together a family of measures for your organization. You've got to understand your organization's system. You need to understand psychology, you need to understand theory of knowledge and how people learn how they change. And nothing else out there puts that on leaders. And so that was a question that Dave was lending back to. Why would somebody do this to themselves? You know, why would they take on this whole extra thing to learn and all the rest of it. And for the people that I know that have made that, that bridge, the pure joy that they get and the rewards they get from people who are learning and that they're leading and that they're changing and they're able to go to other organizations and repeat this and call them up and say, thank you so much for helping me learn how to be a real leader. 0:08:35.8 Cliff Norman: I mean, that's the reward in it. But it requires a real change on the part of the leader. And I don't know of anything else, Andrew, that actually requires that kind of in depth change. And there was one of our leaders, Joe Balthazar, he had Jane and I do four years in a row with his leadership team, teach them the science of improvement. The same curriculum, same leaders, four years in a row. And the second year I was doing it, I said, don't we need... No, no, Cliff, I want you to do exactly what you did last year. He said, it takes years for people to understand this. And I thought, wow, this is unbelievable. But on the fourth year, the VP of sales walked up to me and he says, I think I figured it out. And I thought, wow. And it does it literally... Because you've got to depart from where you've been and start thinking about how you're going to change and let go of what's made you successful up to this point. And that's hard, that's hard for anybody to do. 0:09:47.2 Cliff Norman: And anybody's been through that four day seminar knows when they crossed that path that all of a sudden they had to say, you know what I've been doing, I can see where I've been, the problem and not the solution. And that's tough for us. That really is tough. And Deming says you have to give up that guilt trip. And once you understand the theory of variation, once you understand systems, once you understand psychology and theory of knowledge, it's time then for you to move on and let go of the guilt. I hope that makes sense. But that's the difficulty in this. 0:10:17.6 Andrew Stotz: It reminds me of two, it made me think about two things. I mean, I was just a 24 year old guy when I attended the seminars that I did, and they weren't even four day. I think they were two-day ones at Quality Enhancement Seminars in, what was it, George Washington, I think. But the point that I remember, as just a young guy who I was, I pretty much admired all these business leaders. And then to see Dr. Deming really nail em to the wall and say it's about you changing. And whether he was saying that directly or whether that he was implying that through the Red Bead experiment or other things, it's about you shaping the system. That really blew me away because I had already read some books and I was pretty excited. And then it also made me think about, let's say there's a really good book, I would say Good to Great by Jim Collins that highlights some things that you can do to succeed and make your business better. And you can just buy that book and hand it to your management team and go, hey, implement what you learned from this book. 0:11:20.8 Andrew Stotz: Whereas with the Deming book, it's like there's just so much more to it. So I guess the answer to this is it is more takes time. There's more thinking going on. And I think that's part of the whole point of what your book does, is to help us map it out. So why don't we go through and think about this and kind of maybe step by step through what is the starting point and how do we go? 0:11:45.4 Cliff Norman: Andrew, I just got to add to what you just said there and go back to Joe Balthazar at Hallmark Building Supplies. He shared with me that, and he's the one that said I want you to do these four year seminars dedicated Deming's idea of Profound knowledge. And he said, Cliff, the day I made it, I knew I'd made it. Is my son Joey spilled his milk. He's about three years old. And he said, I started to do my normal leap across the table and he said I was about mid air. And I thought, oh my, this is what they do. This is part of their system. This is common. And I'm treating this like it's special. And that was so profound for him. And when, when you move beyond the Shewhart chart and you see events in your life around you relative to the theory of variation, common and special cause variation at a deep way like that, that's the kind of transformation you want to see in a leader. And Joe will tell you he's forever grateful for Deming and everything he's learned, and I think that's the reward. But people need to be willing to go on that journey, as Dave was saying. 0:12:53.0 Andrew Stotz: So Dave, why don't you walk us through a little bit of what you guys are teaching in that chapter. 0:13:00.3 Dave Williams: Sure. Well, one of the next steps obviously is if somebody, if a leadership team thinks that they want to go on this journey, there's some considerations they got to think about. As we've already sort of alluded to or touched on, this is a leadership responsibility and a leadership change. And so there's got to be will amongst the leadership team in order to say we want to work together and work hard to do this work. That this is not something that, similar to Cliff's example of say, having black belts, that we can just hand it off, somebody else will do it, and we can just keep going about our business and hope. It's important that leaders spend time recognizing and thinking about the fact that this is going to involve them doing work, doing effort, changing the way that they think, changing the way that they practice. And I like to say it's good hard work. I mean it's going to be something that's deeply rewarding. But it does require them to have that will. And with will then it's going to come time and energy, right? They've got to make the space, they've got to create regular routines and opportunities for them to learn just in terms of content, learn in terms of practice or application and learn in the process of doing the improvement work and doing the change to the way that they work in the organization. 0:14:38.0 Dave Williams: So there's going to be a need to build in that ability. And then a third thing is to ask whether you think this is something that you can do on your own or whether it might be useful to have help. And help may be an internal, a consultant, but likely not to promote consulting it but, but there's a good chance that you're going to need somebody that has both experience in improvement and helping people do results-driven improvement as well as somebody who has experience doing system wide change through a lens like QOS. And, and the advantage of that often is it it gives you as a leadership team to focus in on your job of thinking and looking and learning and allow somebody else to be an external intervener, somebody who comes in and creates some of the support, some of the context, some of the ways that can make it easier for you to step back and look at your organization in a different way. And so many times those are some of the things that should be considered as teams working through it. Cliff, what would you add or improve upon. 0:16:07.3 Cliff Norman: The idea of external help. Deming was pretty black and white about that. I was kind of surprised. I went back and read one of his quotes. He said, "I should mention also the costly fallacy held by many people in management that a consultant must know all about a process in order to work on it. All evidence is exactly the contrary. Competent men in every position, from top management to the humblest worker know all there is to know about their work except how to improve it. Help towards improvement can come only from outside knowledge." And I was reflecting on that today with Jane who's been involved in this for 40 plus years also. I said Jane, when he said that, I think it was accurate because at that time she and I were going to Duran seminars. There's only two books out there with methods. One was Ishikawa's book on Guide to Quality Control. And the other was Feigenbaum's book. And then of course you had Duran's book on The Quality Handbook, which was a nice doorstop. But there wasn't that much knowledge about improvement. And the worst part where Deming was really getting to was there's very few people you'd run into that actually under the Shewhart methods and charts and understand the difference between special and common cause variation. 0:17:27.0 Cliff Norman: And so you had to bring that kind of knowledge in from the outside. And frankly, we've had people go off the rails here. You know, Dr. Deming in the teaching of statistics has identified analytic studies which is focused on looking at data over time and trying to understand that and simple methods and approaches and then what he calls enumerative statistics, which is use of T tests, F tests and all the rest of it, which assumes that under the IDD principle that data is independent and identically distributed. Well, if you have any special causes in the data set, it blows up both of those assumptions and the use of those methods doesn't offer any help in prediction. And as Dr. Deming often said, prediction is the problem. And then go back to Shewhart. And Shewhart said, things in nature are inherently stable, but man-made processes are inherently unstable. So when Dave and I first do a Shewhart chart for a client, we don't expect for it to be stable. We expect for to have special causes. And as Dr. Deming said and also Dr. Juran, that when you get a stable system, that in and of itself is an achievement, that means nobody's messing around with the system anymore. 0:18:43.0 Cliff Norman: And you see this in the simplest things, like in an office, somebody will walk in and they think that their body is the standard for what the internal temperature should be for that room. So then they walk up and they start tampering with the thermostat. And by the end of the day everybody's irritated because we've had so many bodies up there with their standard. Moving the funnel on us here, and just leaving it alone would probably all be better off. But you have to learn that. And I think that's what Dr. Deming was saying, is that that kind of knowledge is going to come from the outside. Now the good news is is that since he wrote that in 1986, we've got a lot of people out there and some of them are in organizations that do understand the Shewhart methods and can understand the difference between common and special cause variation. They do understand the difference between a new and analytic studies and statistics and they can be of help. So the Deming Institute has a room full of these people show up, but they're at their gatherings annually. So we're a lot further along than we were in 1986. 0:19:45.2 Andrew Stotz: Yeah. So let's go through that for just a second. Some considerations you've talked about. You know that it's a leadership change. Right. And you gotta ask yourself, are we ready to work on this? And you know, this is not a hands-off thing. The second thing you talked about is time and energy. Are we ready to make the space for this? We have to have regular meetings. You know, we've gotta really... There's some work involved here. And then the third part you've talked about is outside help. And you mentioned about this story of Joe Balthazar and how he asked you to do the same topic over and over for four years. And imagine if he was telling his team, let's meet and try to implement some of this stuff on our own. Everybody dig into a book and then let's try. It would be very difficult to make that kind of progress compared to bringing an outside person. Which also brings me to the last thing that you said, Cliff, which was the idea that Dr. Deming had mentioned, that you need an outside person to truly change something. Everybody's got the expertise on the inside. 0:20:44.5 Cliff Norman: I appreciate you summarizing that because my job and working with Joe and leadership team, I was meeting with him every month. But what the four years that Jane and I spent were the next levels of his leadership. You know, it wasn't the leadership team. And I'm glad you brought that up because it was the very next level that he wanted exposed to this and the VP of sales that came in, he was new, so he had to be part of this group because he wasn't there originally. And so there was that ongoing... He wanted that next generation that was going to take over for him and the others to really understand this. So I'm glad you summarized that for me to help. 0:21:30.5 Andrew Stotz: Yeah. And I think one of the starting points too, I mean, the body of work, not just this book, but the other books that you guys have been involved in and produced provide a lot of the starting points for this. So there's a lot there. Dave, where do we go after these considerations? And the people say, okay, yeah, leadership says, we want to make this change. We're ready to make some time for it. We're willing to get outside support and help. Where do we go next. 0:21:57.7 Dave Williams: Right. Well, one thing that we typically invite a leadership team to do is to take kind of a self assessment of where they sort of see their baseline in relation to the methods and activities of QOS. So in chapter one of the book, there's actually a table that is 10 different categories. And then each leader takes it independently and they rate their level of agreement with different definitions from 0 to 10. 0 being this really isn't present, and 10 is, I'm very, very far along on this journey that in the book that's out now, there's a summarized table, it's on a page. But actually in the QOS field guide that we're working on publishing this year, there's a much more detailed version that we use in practice that has deeper definitions, but basically it works its way through purpose and leadership and systems thinking and measurement and all the things that are tied into QOS and what... And as I mentioned, we have each individual member of the leadership team take it independently and then we bring those scores together to learn together. 0:23:32.5 Dave Williams: And there's different ways in which you can display it. In the book, we show an example of a leadership team's scatter plot where it shows the rating and then it also shows the standard deviation amongst that exists between the leadership team. It's very, very common for leaders to not be in agreement in terms of their score in each of the different areas. You know what I said, It's a 0 to 10 scale. Typically, in my experience using the tool, people tend to be between a 2 and a 6 and hovering around a 2 or a 4. But it sort of looks like a buckshot or shotgun blast where there's a very... If you were to put dots where everybody scores, where there's variation that exists. And that's good because it's useful for the team to pause and think about why they assess the organization the way that they did. Looking at it through this new lens, where are the places that there's agreement and also where are the places that there's variation? And that helps them to be able to think about the fact that through this process, they're likely to both improve their assessment of the organization, but also increase their agreement about where they are and what they need to do to move forward and what they need to do to improve. 0:25:05.2 Dave Williams: And so that's a useful starting point, gets everybody kind of on the same page, and it's something that we can use at intervals as one of the ways to continually come back and evaluate progress towards the destination of pursuing quality as an organizational strategy. 0:25:23.7 Andrew Stotz: Yeah, I mean, I imagine that self assessment, it helps you too when you work with companies to be able to really understand, okay, here are starting point with this company is really, they just really don't know much about all of this stuff, whereas you'll have some other clients that basically, wow, okay, there's a lot of knowledge here about it, but how's the implementation and all that? So are we ready to change? Are we prepared to devote the time and energy? Are we going to get outside help? And where are we now? What's our starting point that's great to help us understand exactly how you step through it. What comes next? 0:26:03.5 Cliff Norman: Well, in that very first milestone, in that table, is it table three, Dave? Anyway, the very first milestone is to establish formal improvement efforts. And the reason for that is that unless people experience what it takes to develop, test and implement changes in the organizations, they really can't appreciate the structure that comes with quality as an organizational strategy. Because it's very difficult for many organizations to launch three or four improvement efforts and then bring them to fruition. And there's all sorts of stuff that happens. And then you find out very quickly whether you have managers or leaders, and organizations they've brought me in, they say, let's do some leadership training. I said, no, let's just do some improvement and then we'll find out if we have leaders or not. And one group, I won't mention who it was, but they had five people on their leadership team and they had to replace two of them because they found out they couldn't actually manage an improvement effort. And then the CEO was wondering how they actually manage their organization, which they weren't either. And so it's a rather, it's an important test in the front. 0:27:22.2 Cliff Norman: But as Dr. Juran says, it's real important to develop the habit of improvement. And if you don't know what that is, if you've never experienced it, then it's hard to say to people, gee, I need a purpose that aligns my improvement efforts. I need to understand my system so I know where those improvements are going on. I need to build an information system, get information from customers outside, people inside. I need to put together a strategic plan that actually makes improvements on purpose. That's a lot of work. And once you understand how complicated it can get in terms of just doing three or four improvement efforts and then all of a sudden you got a portfolio of 30 to do your strategic plan. Now that needs some structure, that needs some guidance and all the rest of it. But I'll just go back one step further. My own journey. I was sent by Halliburton at Otis Engineering to go see Dr. Deming 1982 in February. And coming back, I had an audience with the president of our organization, Purvis Thrash. And I went on and on about Dr. Deming. He said, Cliff, you know what I'd like to have? I said, what's up, Mr. Thrash? 0:28:27.5 Cliff Norman: He says, if you'll take this 50 million dollar raw material problem and solve this for me, I'll be a happy man and I'll give you all the quality you want. But go take care of that problem for me first and then come back to me and talk about Deming and Juran and anything else you want to talk about. So I put together four or five people and over about three months we solved his 50 million dollar raw material problem. And then he had a meeting of all executives and I was sitting with the managers in the back row and he called me to the front and he says, Cliff, will you sign this card right here? And I says, well Mr. Thrash, what is this? He says, well, I'm giving you authority to sign $50,000 anytime you need it to get all the quality we can stand here at Otis Engineering. One of the vice presidents said, well, I don't have that authority. He said, you didn't save me $50 million. You know, but once that happens, Andrew, once you do that, then you've got people that are willing to help you. And then once that takes place, I can't tell you how important, it allowed me then to bring in Lloyd Provost to help me. 0:29:36.2 Cliff Norman: And they weren't about to pay out money. They didn't like consultants, in fact, they were anti-consultant. But you saved us $50 million. I gave you $50,000. And Lloyd doesn't make that much. So get him in here, do whatever you need to go do. And I just think it's so critical that we have that demonstration project that people understand at the leadership level what we're talking about when we talk about design and redesign of the system. 0:30:00.0 Andrew Stotz: Yeah. I mean, I appreciate in the book you're talking about this concept. I'm not going to call it quick wins, but the idea is we need to get results. You know, this isn't just about talking about stuff so that's one thing that as you just illustrated, that's one point. The second thing you mentioned, is this person a leader or a manager? You know, and I think for the listeners or viewers out there, they're probably... When they heard you say that, they're probably thinking. Okay, wait a minute. Are my team managers or leaders? How do I know? What would you say? What differentiates the two? 0:30:37.2 Cliff Norman: I was fortunate to hang around Dr. Maccabee, as Deming did, and I asked Dr. Maccabee that question. He said, Cliff it's actually pretty easy. He said leaders have followers, and if you have followers, you can be anywhere in the organization, be a leader, but if you don't have followers, you're not a leader. You might be a manager with authority. You're not a leader. 0:31:02.7 Andrew Stotz: Can I ask a little bit more on that? So I'm thinking about my own business, which is a coffee factory, and I have people that are running the business, but I also have people that are running departments like the roasting department. And that area when they're overseeing this and they're doing a very good job and they're keeping things up and all that. How do I understand in a sense you could say, are they followers? Well, not really. They're people working for them and they have a good time and so do I view that person as not necessarily a leader, but more of a manager, or how do I look at it in my own company? 0:31:35.5 Cliff Norman: It could be a manager, which is essential to the organization. And that's another big difference. You see, the leader can't delegate their relationship with the people who are followers. You can't do that any more than a teacher can dedicate her class to a substitute teacher. Anybody that's ever watched that knows that chaos is getting ready to break out here because that teacher has a relationship with those students. She knows them all in a big way. And when the substitute comes in is game time in most classrooms and so forth, the managers have skills and things that they're applying and they can actually delegate those. Like when I was a foreman, I could have somebody come in and take over my department and I say assign all my people tomorrow. And they could do that. Now, in terms of the people that I was leading that saw me as a leader in that department, they didn't have that relationship. 0:32:30.2 Cliff Norman: But management or skills and necessary things to make the organization run like you're talking about, the coffee is not going to get out the door unless I have people with subject matter knowledge and competent managers to make sure that the T's are getting crossed, the I's dotted and the rest of it. But the leadership of the organization that has followers, that's a whole different person. And I think it's important. That could be anywhere in the organization. Like I had at Halliburton, I had a VP of engineering. Everybody went to him, everybody. He had 110 patents. You know, he built that system. He built the whole organization. So the CEO did not have the followers that the VP of engineering had. And it was well earned. It's always earned, too. 0:33:16.7 Andrew Stotz: Yeah. Okay, that's great. Leaders have followers. Leaders cannot delegate their authority. They have a different relationship. 0:33:24.0 Cliff Norman: They can't delegate the relationship. 0:33:25.8 Andrew Stotz: The relationship. Okay. 0:33:27.4 Cliff Norman: Yeah. Very important. 0:33:34.3 Andrew Stotz: So now let's go back to what, where we were. So we were saying some of the considerations. Are we ready to change? Are we prepared to devote the time and energy? Are we ready to get outside help and where are we now? And that self assessment that you talked about helps us to understand what's our starting point. I always tell a joke with my students about this when I talk about. I'd say, imagine you go to London and you're going to go visit your friend and you call your friend up, you say, I've arrived and I'm calling from a phone booth and just tell me how to get there. And the friend says, well, where are you? And you say, I'm not really sure. Well, do you see anything around you? Yeah, well, there's lots of buildings, but I don't really, you know. Well, do you see any names of any streets? No, I don't really see anything. But just tell me how to get there. There's something missing. If we don't know where we are, it's very difficult to get to where we're going. So now we understand where we are. We got that scatter plot that you guys have that you've talked about. Dave, where do we go next? 0:34:26.6 Dave Williams: Well, so Cliff already mentioned one of the fundamentals. And sometimes I think this is something that people struggle with because they want to jump into something new. But one of the best starting points is to focus in on improvement. And there's a number of different reasons for that. So one is that I don't know about you all, but in my experience, if I ask people, like, hey, I want to create some improvement projects and get started on improvement, I always tell people, like, if you remember the old Stephen Covey exercise where he put the rocks and the stones and the sand into a jar and poured water. And like you would do it in different orders. And I'm fascinated that people will stare at the big rocks or the things that are right in front of them, or the things that are on their agenda, or the things that are part of their strategy. And then they'll look to the side and grab some rare event or some extra thing that isn't related to that, but they've always wanted to work on. And where we try to focus people's attention is one, what are you already working on? Can you look through your and ask around, what are the things that are currently in play, projects that exist? And sometimes we won't ask, what improvement projects do you have? Because if you do that, you get a short list. 0:35:51.4 Dave Williams: Those are the things that people defined as an improvement effort, or maybe use some kind of framing to decide it was an improvement project. It may be better to in the beginning of the book, in the first chapter, we talk about different ways that you improve. And there's designing and redesigning a process. There's designing and redesigning a service or a product. There's changing a whole system. And so it can be useful to say, well, what are we doing in these areas? And that may actually create a bigger list of the various things where people are working on something that's about change to the system that may lend itself to be better activated through firing it up as an improvement project. And then, of course, there's a good chance that any organization, especially if they've done some kind of strategic planning, have some strategic objectives or some strategic priorities which they've committed to or already said, these are the things we're going to work on. So kind of crowdsourcing or bringing those together helps us to potentially find the early portfolio of projects without having to look much further, without having to say, what else do you want to work on. 0:37:07.0 Dave Williams: And then if we've got that, if we've got that list, a second thing that we can do is invite people to use the three questions of the model for improvement and reflect on can you answer these three questions? Do you know what you're trying to accomplish? Do you know how a change will result in improvement? Do you know what changes you'll make? What's your theory about how you'll get to improvement? And so having a list of the things that are already present or existing may be one first step. Another second step in the firing up a portfolio of improvement projects is asking the three questions for the model for improvement. And then a third one, if it's an active project is we have a project progress scale that you might use that can help you gauge. So I've got a project where is it on its journey towards achieving its aim or getting results? Those three can help us to sort of get a sense of the work that is at hand and that has already been sort of started in some fashion that is already in progress and maybe to get a sense of the level of definition and the progress that exists. 0:38:22.3 Dave Williams: They may not be the right projects, but that's a good place to start before trying to create new ones. And I'll hand it to you, Andrew. 0:38:30.4 Andrew Stotz: I find that interesting. Both the story that you told Cliff about fix my raw material problem and then, Dave, what you're talking about is as you talk in the book, focus first on improvement. What are we already working on? What's an improvement project we've got? What's a problem we've got? Because a lot of times, let's say in the teachings of Dr. Deming, it's like, no, get your mind right, read this stuff, read this, figure this out, think about this, go to a seminar, talk to other people before you do anything. I feel like that is oftentimes where people get caught is they get caught up in, I need a year to think about this. And can you explain a little bit more about why once we've done our self assessment and we're ready to go, that you focus on improvement rather than the thinking process? 0:39:21.7 Dave Williams: Well, because we want to... Well, one, we know that in order to get results or to get a different result than what we want, we got to change the system that we got. Right. So in order to do that, we've got to do improvement. The other thing is that there's already energy that's being expended here. 0:39:41.4 Andrew Stotz: That's a good point. 0:39:42.7 Dave Williams: The risk that often I find people run into is that they then add other projects that are not strategic into that bucket and take up more energy. I'll tell you an example. I was working with the health system here in the States and we crowdsource just the things that they were calling improvement projects. The health system had 25 active teams that were just the ones that were called out as improvement projects. When we looked at those 25 teams, the vast majority of them were not actually... They had been meeting for months and doing things for quite some time, but they actually weren't doing any changes and, or they've been testing changes for quite some time. So, now just this exercise alone by only asking, what improvement projects do you have? You realize you've got 25 teams that have been resourced or are spending energy or going to meetings or focused on something. They may not be the strategic thing that matters, but that's irrelevant right now. We just know that we already have invested some interest here. The second thing is these folks have been on this journey for quite some time and are not making progress. 0:41:01.7 Dave Williams: So that tells me something about maybe the way that they framed it. Did they charter it well? Did they have the right people in the room or the right team? Did they have the right tools and methods to be able to break down the problem and then figure out what to test and learn? So there may be some difficulty... 0:41:19.4 Andrew Stotz: Or did they even just dissipate their efforts across 25 projects too? Right in their resources, yeah. 0:41:26.1 Dave Williams: Yeah. Or there are overlaps? So there's a number of different factors. There's actually a paper that was published by a health system in the United Kingdom, and it was really interesting. They spent a lot of attention on generating will through training and getting people in the classroom and teaching them about improvement methods. And they fired up all this energy. They had a massive explosion of the number of projects that were started or where somebody went into their software. They had a software platform. Anybody could go and start a project. Well, something like 50% of those projects never actually got to PDSA testing where they changed anything. And then there were a slew of them that were stuck in PDSA testing but never saw any movement in their process measures or their outcome measures. And only a small number actually progressed in achieving their aim. And I asked the Chief Quality Officer about this, and and he admittedly said that it was very exciting that we we're generating will and getting things going, but that alone was only getting them to maybe some early design and some thinking, but they weren't getting them to results. 0:42:34.8 Dave Williams: And I said, well, what about the ones that were getting results? And he said, well, those are actually ones where we've got an improvement advisor who's got some skills and ability and improvement. There are things that are resourced, there are things that were prioritized. And man, when we did all those things, they moved from planning and organizing and thinking to testing changes and moving in a direction of goodness and getting at least results in their process measures, if not their outcome measures. And so in my mind, I was like, I appreciate you're trying to build this sort of culture, but it felt like a lot of burnt energy at the front end with all these teams getting into training and firing up their software and more energy might have been strategic in copying what was getting to results. And I think that's part of what we're trying to get to, is helping people learn. You've got if you don't have a method to figure out strategic projects, let's look at the ones you got. How are they going? Where are people at? And how effective is the capability that you have within your system right now? And the leaders want to be part of that, and they can learn within that to go, oh, wow, this is our current state. 0:43:47.2 Dave Williams: And so maybe we're going to agree to continue on with these projects. Maybe we're going to sunset some of them, but we're going to learn together about how do we get better at getting better, and how do we learn how to move projects forward and not to have them take two years. Let's try to get them down to four or six months, whether that's through scope or execution. But let's get better at getting better. And then as we're building... Developing the early activities of QOS, we'll eventually get to a point where we'll also be able to identify more strategic projects that are going to move us towards our aim or towards our purpose better. And this will help us as we're trying to build the capability to get there. 0:44:32.7 Cliff Norman: You know, Andrew, early on, when Dave went down this path, he said that we got to make sure that somebody's working on improvement. They're actually making changes. And Jane and I were working with a group, and the CEO said they've been meeting a long time. Could you down there and see what they're doing? Because nothing's happening. And we started looking through their agendas and they had everything well documented, and it was all about getting ready to get ready. And then they'd assign the dessert. Who's going to bring the dessert to the next meeting. And Jane looked at him and says this reminds me of something, Cliff. I said, what's that? Can I share my screen? 0:45:10.9 Andrew Stotz: Yeah. Yep, go ahead. 0:45:13.7 Cliff Norman: I may send this to. You may know about it, but this is Dr. Deming's Diary of a Cat. And everyday... 0:45:20.6 Andrew Stotz: It hasn't come up yet. Hold on one second. Hopefully you've got permission now. 0:45:28.6 Cliff Norman: Let me go back and check here. 0:45:33.9 Andrew Stotz: Okay. It looks like it's coming up. One second. 0:45:38.4 Cliff Norman: It said every day is today. There's no theory days of the week. But today I got up some food in a bowl, it was great. Slept some too. Play with yarn, got some food in a bowl, had a good nap, slept, food, yarn, fun. Play with a shoelace. There's a big change right there. Went from yarn to a shoelace. Some people call that a job shop. And ate, slept, had a good day, slept, ate some food, yarn, so forth. So, and the team meeting looked just like that. But there's really no changes going on relative to improvement. So Dr. Deming would often share this into four days seminar to make sure that we weren't involved in the Diary of the Cat, but we were actually doing something useful in terms of making changes in the organization. 0:46:24.4 Andrew Stotz: That's a great one. And it helps us to understand that we could be busy all day long and not improve anything. 0:46:31.8 Cliff Norman: You know, or actually confuse that with improvement. In fact, we have an operational API that my team, we were embarrassed in our first, wait a second, our first improvement guide we wrote. And Dr. Adamir Pente, who's a professor at the university in Brazil, he sent us a note and he said, I know you guys and he said you're real big on operational definitions, but you've written this book on improvement and nowhere have you, you've defined what you mean by improvement. And then he put together a three part definition that there's a design and redesign system, there's system measures and the change is sustainable and lasting and so we put that definition in the second edition. But I was confronted at a university, I won't mention which one it was, but they had 30 Keystone projects for a advanced degree program for nursing and they were convinced they were doing improvement. And when I had them apply that definition, they came up out of the thirty. They only could find two projects out of the 30 where they were actually designing and redesigning the system, which, that's the first thing Dave said are we designing and redesigning and making real changes? And people think just showing up and going through motions and all the rest of it is improvement. No, it means... 0:48:07.8 Dave Williams: Looks like we've lost... 0:48:11.9 Andrew Stotz: We lost you at the last, the last statement you just made. People are going through all this stuff and thinking that they're improving, but they're... 0:48:22.8 Cliff Norman: Yeah, it's showing up and going through motions and you know, having the meetings and making sure we assign who's bringing dessert. But we're not really designing and changing the system. We're not getting measurable changes of improvement. In other words, we haven't tracked the data over time and we can't say that the changes that we've made are going to in fact be sustainable because we haven't known what we've done to the system to deserve a sustainable change. 0:48:51.4 Andrew Stotz: By the way, what a buzzword these days, sustainability, sustainable and all that. And you just think do people really think about how we're building something that's really lasting and sustainable? 0:49:04.8 Cliff Norman: Well, we have a checklist and actually Jane designed it for the first edition and it literally lays out what changes did you make, which processes did you change, what's going to change in the documentation, whose role statements have been changed in the organization because of this change. And once all that's answered on that checklist, which is in the book, then we can... But we're pretty certain that we've created the structure to make it easy for people to do the right thing and hard to do the wrong thing. But unless that structure's changed, probably not much going to happen. 0:49:40.8 Andrew Stotz: Just for the sake of time, because I think we want to wrap up in just a bit. But there's so many stuff, so much stuff that we've been through. But I know there's even more in this chapter, but how would you start to bring this together for the person who is a leader, himself or herself, and they're listening to this and they're thinking, okay, I'm ready to make a change and I'm prepared to devote the time and energy because I see the outcome and I'm open to help, whether that's through the book and other books, whether that's through a consultant, whatever that is. And I can even do a self assessment to some extent and know where our level is, which is very low. We don't know much about this type of stuff and that type of thing. We talked about the first focus on improvement. How do they pull this all together and start moving on it? 0:50:35.0 Dave Williams: There's three things that follow the self assessment. The first one is this focus on doing improvement work and setting up a portfolio of projects. And we just kind of talked about many of the different methods that go into that. And like I said, sometimes that when you say that out loud, leaders don't initially get excited by it because they think they have it. But actually it's a powerful opportunity for you to learn about what's currently going on in the organization and about where this opportunity is to reduce a lot of the noise and a lot of the friction that's getting in the way from you getting to results. The second thing that often happens in parallel is that the leaders need to build a learning system where they're going to be able to learn together both about these projects and what these projects are telling them about their organization, about their culture, about their people, and about their capacity to get results, but also that they can start to be learning about the science of improvement and profound knowledge and the activities of QOS that are going to be part of what they're going to work on developing over the course of the first year or two. 0:51:50.6 Dave Williams: And so that typically is, that's making that space and energy. It's a blend of book learning and application and practical. Trying and looking at things within the organization. It's a very applied approach, but it's an ongoing piece of their discovery. And I often argue that this is a real opportunity for leadership because they're going to be able to see their organization in a way that they haven't seen it before. And when we talk about profound knowledge, they're going to gain this profound understanding and expertise about what they're charged with and what they own and what they want to change in a way that they haven't been able to have it before. And so it's a hard work, but rewarding work. And then third is that typically where the, where we invite people to start is to focus in on the first activity, which is to develop or establish or develop their purpose. When this work was initially framed, not everybody was as... Not everybody had a mission, vision and value statement or a purpose statement that wasn't as common, but today people do. But the difference here, and you'll see this in the chapter on purpose, is that organizations that are pursuing quality as an organizational strategy are organizations that are systems that are built to constantly be trying to match a need that exists out in the world. 0:53:34.7 Dave Williams: And so often a learning for people is to step back and have to reflect on, well, what is the need in which we are creating these products and services to match? And if we're creating these things to match the need, how do we understand what's important, what are the quality characteristics that matter? And then how do we define what our mission is in that context? And being able to say, here's why we exist and the need that we're trying to serve, and in what way? And how do we set a vision for where we want to get into the future and what are the tenants or the practical values that exist in our organization, that we want to define how we work together in terms of building in that way. And so purpose is a big focus. It's that clarity of the need, the clarity of the quality characteristics that it takes to match that need. Understanding what are the products and services that we have. I know that sounds a little trivial, but you'd be stunned how hard it is, especially in service organizations, for people to actually describe what it is that they do, what are the actual services. 0:54:54.3 Dave Williams: They might have the name of the service or the class or the whatever, but to actually say this is what we deliver, and then really think about how do I use this as our organization's sort of North Star, our aim, so that everything else that follows is going to be about building a system that produces the results that we want and produces the services that match that need. So going forward, that's going to be very, very important in instructing the direction and instructing the way in which we're going to work as a community of professional people together. 0:55:30.8 Andrew Stotz: So after self assessment, we're talking about focusing on improvement. We're talking about building a learning system, and we're talking about revisiting or establishing or developing our purpose? 0:55:43.3 Cliff Norman: Yeah, I'll just add to what you just said there, Andrew. There's three basic things that have to happen when we start working. Number one is create the habit of improvement. Start improvement right away. Second thing, Dave just went through some detail on building a system of improvement. And Dave called that a learning system, which I thought was interesting because that's what Dr. Maccabee called it when he saw the five activities. Said, these are really methods for building a learning organization. And he said, I've never really seen them before, but this is what will come out of this, which is the essence of what you want. You want people continually learning, as Dr. Deming said, so they can continually improve. But the third thing that has to happen is we have to develop internal capability for them to carry this on, because we're not going to be around with them. We've never advertised. We don't advertise for clients, and we only get word of mouth. And we're only in there to do those three things, get them started on the habit of improvement, start building the system improvement so they can take it over. 0:56:43.4 Cliff Norman: And the third thing, start developing internal capability so they can continue it on into the future. So those three things basically take off on day one. And depending on the organization, I think this is critical. Dave, you asked this question the other day, if the context is such they've got things in front of them are so bad and so challenging that they just need to work on improvement. That's where we're going to be focused. But now if they can chew gum and walk at the same time, we're going to start building the system of improvement. And the first people I want on those initial teams, I want people on there who are going to be future improvement advisors. And more importantly, they perceive them as future leaders in the organization. I don't want a cadre of a whole bunch of improvement advisors. I want leaders in the future who actually understand the science of improvement, understand these methods, so when they go to the next department, the next organization, they can carry this on. So those three things start improving, start building a system of improvement. And the third thing, start developing internal capability. Those have got to take off almost simultaneously, depending on the situation, of course. 0:57:49.8 Andrew Stotz: Well, on that note, that's quite a discussion. I'm so happy that we can have this to go in a little bit deeper into the work that you guys have done. Again, the book is Quality As an Organizational Strategy. I got mine on Amazon and it sent it to me. But I wonder if you have any last words that you'd like to share about what we've talked about today in relation to getting started. 0:58:18.3 Cliff Norman: So, Dave, why don't you talk a little bit about. Because I think this is critical. We've just finished Andrew, the book that's going to be for the people who actually have to build this system. So Dave, just say a few things about that if you would, because you. 0:58:32.0 Dave Williams: About the field guide? 0:58:33.8 Cliff Norman: Yeah. 0:58:35.5 Dave Williams: Yeah. Well, so when this body of work was first created, there was the content of which you see in this book. And then there were also a lot of exercises and methods and applications and examples that existed as well. And it was a pretty thick binder. We have created two volumes. One, the book that you have, which is the description of the theory and the method and gives you some of the tools. And we're now in the process of pulling together what we call the QOS Field Guide, which is a guide that is supporting people that are going down this journey. It follows the same structure as the book, with the exception of the, the Getting started chapter that we had at the end is now at the beginning. And it walks through in great detail various ways in which you leaders and practitioners can approach getting started and building the capacity and then working through each of the activities. And it's equal in size, I mean, it's about the same thickness. But what we tried to do is to give people really pragmatic things to do. 1:00:01.1 Dave Williams: So there are exercises where people are simulating an idea or a concept or a particular piece. There are what we call QOS applications, which are where you're actually taking the theory or the method and applying it to your own organization. There are case studies and things that have been built that might allow you to practice. There's wonderful examples of just about everything from all, from people that we have worked with over the years across multiple different fields, from my background in emergency services and healthcare to education to manufacturing to elevator companies, all kinds of great stuff. And so that will be helpful as people are trying to think about pursuing this journey and working through that first phase of developing QOS and moving into using it. And we're in the stages of having it done to be available later this year. 1:01:08.6 Andrew Stotz: Exciting. 1:01:09.2 Cliff Norman: We've tried to make it useful, Andrew, that the people have to stay overnight with the management and actually get something done and build it without being run off. That everything is there for them to make sure that they make it successfully. That's the thing we kept in mind as we kept writing this second volume. 1:01:25.2 Andrew Stotz: Yeah, I mean, I would say my experience with your guys's writing is that it's applicable. 1:01:34.1 Dave Williams: Well, Andrew, one thing I was going to add on you mentioned a lot of different examples. There are a lot of books in which people tell you a theory, but they don't tell you how to do it. Or they tell you about their own experience, but they don't actually convey the theory. The Quality as an Organizational Strategy book is laying out the theory and the methods of this approach built on the foundations of the science of improvement and profound knowledge and the Deming philosophy. The QOS Field Guide adds to that by giving you the methods and the tools and the things. It doesn't mean that that by itself you can't just go through like it's some kind of self guided tour and all of a sudden magic happens. There's a lot of work and learning and things that have to go into going through that process. But between these two volumes, a leadership team has the tools and methods that put them in position to be able to make this journey. 1:02:41.4 Andrew Stotz: Right. Well, let's wrap it up there. On behalf of everyone, I appreciate Dave and Cliff. All that you're doing and you're sharing with us and taking the time to do that. So from everyone at the Deming Institute, I want to thank you again for joining this and bringing your discussion on these topics. And for listeners, remember to go to deming.org to continue your journey. And you can find this book, Quality as an Organizational Strategy at Amazon and other booksellers. Are there even booksellers these days? I don't even know. They're mainly online these days. So this is your host, Andrew Stotz, and I'm going to leave you with one of my favorite quotes from Dr. Deming, which is "people are entitled to joy in work."

Mar 24, 2025 • 27min
Powerful Learning with PDSA: Path for Improvement Part 8
It's time for PDSA (Plan-Do-Study-Act) Cycle 2 in John Dues' journey to reduce chronic absenteeism in his schools. His team is using PDSA to quickly test ideas and learn on a small scale. Find out what happened and how PDSA can be a powerful tool for learning. TRANSCRIPT 0:00:02.2 Andrew Stotz: My name is Andrew Stotz, and I'll be your host as we dive deeper into the teachings of Dr. W. Edwards Deming. Today, I'm continuing my discussion with John Dues, who is part of a new generation of educators striving to apply Dr. Deming's principles to unleash student joy in learning. The topic for today is Powerful Learning with the PDSA Cycle, Part 2. John, take it away. 0:00:26.7 John Dues: It's good to be back, Andrew. Yeah, like you said, we, I think for the past three episodes or so, we've been working towards getting a better definition of our problem specific to this chronic absenteeism issue that we're working on this year. I don't know if you remember from last episode, but we have this team working and they've basically said we don't have enough information quite yet to write this precise problem statement. So we decided to gather information running the Plan-Do-Study-Act cycle. And last time we focused on the first cycle. This episode, we're gonna focus on a subsequent PDSA cycle, sort of along those same lines. For folks that are watching and perhaps just joining for the first time, I'll kind of share my screen and do a little bit of a review so that everybody can see or know what we're talking about, even if they're just listening for the first time. So we've talked about this improvement model. We're working through this four step improvement model. So set the direction or challenge is the first step. Grasp the current condition is the second step. Third step is establish your next target condition and then fourth, experiment to overcome obstacles. 0:01:44.3 John Dues: And we're doing all this with a team, people working in the system. People have the authority to work on the system and someone with the System of Profound Knowledge knowledge. right. And so, you know, we've talked about setting that challenge or direction. And as we're grasping the current condition, we've actually decided to skip to step four and experiment a little bit so we can get a deeper understanding of this problem that we've been working on. And you'll remember probably as well, did the screen change for you so you can see the chart now? 0:02:21.8 Andrew Stotz: Yeah. 0:02:22.9 John Dues: Yeah. Great. So I thought it'd be helpful to show this again too. So this is our process behavior chart of the chronic absenteeism rates dating back to the 2016/'17 school year. So we have eight years of data in regards to this problem. And you'll remember when we talked about set the direction or the challenge, we wanna basically cut this chronic absenteeism rate we're seeing coming out of the pandemic by a lot. So we're hovering around this 50% chronic absenteeism rate. We wanna cut it to 5%. So that means, you know, 50% or more of our kids, or right around 50% of our kids are missing 10% or more of the school year. 0:03:06.2 John Dues: And this is a trend that we're seeing all over the United States right now. And the other thing that we talked about is when we looked at this process behavior chart, that it's basically like there's a pre-pandemic system of chronic absenteeism, and then there's a post-pandemic system of chronic absenteeism. So, you know, before the pandemic, the rates were too high, but nowhere near to where they are now. So, you know, prior to the pandemic, we were sort of hovering around the, you know, 20 to 30% of kids chronically absent. And then, you know, coming out of the pandemic, it's been more like that, that 50% number that we've, that we've talked about. 0:03:49.4 Andrew Stotz: And so to reiterate for the listeners or the viewers, this is the chronic absentee rate at your school, as opposed to nationwide, which I remember last time you talked about, it's about 30% nationwide, and pre-pandemic, it was about 16%. 0:04:06.5 John Dues: Yeah. Right around there. So, yeah, so I'm talking about the four schools that make up our school system in Columbus, Ohio. 0:04:15.8 Andrew Stotz: Yep. 0:04:16.6 John Dues: And, you know, we have a pretty high percent of our kids are economically disadvantaged. And so the rates in schools that have that demographic tend to be more like ours, in that 40, 50% range. And then, but all schools coming out of the pandemic had much higher rates than what they had pre pandemic. No matter your affluence levels. It's just, just like a lot of things the schools with the most kids living in poverty get hit the hardest when you have these problems, basically. So, yeah, yeah. So what we were, we were studying this problem, and, you know, we have some idea of what's causing our challenges, but we've started running these PDSA cycles to dig into that a little bit more, and I'll, I'll, I'll stop sharing. So that's not distracting. And so we ran this first PDSA cycle we talked about last time, and now we're running, or we've just gotten finished running a second PDSA cycle. So for folks that are new to that, what that means is that we are basically running an experiment to test an idea, an idea about how to improve chronic absenteeism. 0:05:26.6 John Dues: And to do that we plan the intervention, then we do or run the experiment, we study it and then we act on that information. 'Cause that's where the PDSA comes from. So basically the objective specific to PDSA 2 is were or we designed a individualized intervention based on responses we get from interviews with kids using this five whys sort of empathy interview template. Right? And then after we do that, what's happening is that students are actually. So after the five whys is completed with the student, we move right into creating the plan of the PDSA still with that student. So they're part of the process. So that's also sort of a key, I think innovation of this particular round of PDSAs is the student is sitting there as we design the intervention. A student that has some issues with chronic absenteeism. And then basically in this particular plan, we decided we're gonna collect detailed attendance data for two weeks to evaluate the effectiveness of that. 0:06:39.7 Andrew Stotz: When you said this one, are you talking about the PDSA one or two? 0:06:43.5 John Dues: Two. The one. The one you just got done running. The one we're talking about. So the PDSA 2 ran for two weeks. So when I say experiment, I'm not talking about, you know, like a randomized controlled trial that can last a year or two years or five years before you get the results. I'm talking about something you can do in a day, a week, two weeks. My general rule is not to go over a month with these PDSA cycles. It starts to feel like it's too long. I wanna get data back quicker than that on an intervention. And so that's what we did with this PDSA cycle 2. And it was really, the plan was built around this key question. The key question was, will involving students in the design of an individualized intervention to address their chronic absenteeism lead to an increase in their average daily attendance rate during that period of intervention. So we're not taking that for granted just because we're sitting with the kids creating a plan with them. We don't know, we don't know what's gonna happen exactly. And basically step one of that plan was this five wise interviews that I talked about. 0:07:50.2 John Dues: So basically we had four staff members. So each one was assigned a student at their campus that they chose to work with on this initial intervention. And they took a piece of sticky paper and up top they basically wrote, here's our problem, the student's name. So let's say James is not coming to school consistently. And when students miss a lot of school, they're at risk of falling behind academically. And right below that problem statement, then they wrote, why are you not coming to school consistently? 'Cause that's the first why question. So that's sort of the first part of this five whys interview. So it's very simple. You need chart, paper and marker in about 20 minutes to do this. Step two is, then they used the information that they gathered from that five whys interview to design the intervention with the student. And basically what they did was they designed the intervention around the root cause that they got to at the bottom of that five whys sequence. So basically, you know, when they said that, when they asked that first question, you know, why are you not coming to school consistently? The student is then going to say something, right? I miss the bus almost every day. 0:09:10.7 John Dues: And so the next question, the next why question is built on the previous answer from the student. So why do you miss the bus every day? And you kind of keep going. And it doesn't always happen perfectly. Sometimes it takes three questions, sometimes it takes a little more than five. But generally speaking, once you drill down with those five whys, you'll get to sort of a root cause from the interviewee, right? And so then they're basically saying like, you know, based on that root cause we identified, what do you think we can do to improve your daily attendance? And then now they're sort of transitioning from the five whys into the planning of the intervention. And sort of that was step two of the plan. And step three is then actually starting to track the student's daily attendance as they do whatever that plan is across the 10 school days that are in that particular cycle. So that's the plan phase. You know, we had a key question that we designed around, and then the team also makes predictions about what they think is gonna happen during that cycle. That's the plan. 0:10:23.5 John Dues: And then, so then they move into, once the plan's in place, you run the experiment. That's the do, right? And so in this particular do, PDSA cycle two here, that team collected both the quantitative data, so that's the five whys interview, and then the quantitative data, that's the daily attendance data. And so, you know, I mentioned that they had chosen four students to do this work with. And so what you're doing in the do is saying, did you do the plan? Basically. And that shouldn't be assumed because things may happen that interrupt the plan or derail the plan or make you change the plan. The guy that's designing these PDSAs is pretty good project manager. He knows improvement science, he knows the Deming stuff pretty well. So largely this experiment ran as planned. It's also for a pretty short time frame, so there's less time for it to go sort of off the rails and go wrong. But one of the student's attendance, it was so poor during this two week period that they never actually held the empathy interview. So you're noting stuff like that. You plan to interview four kids, you actually only interviewed three kids. 0:11:34.9 John Dues: And here's the reason why, we couldn't even get to the part of interviewing the student, this particular student, because he was not there during that two week period when they were gonna do the interviews. And so then the data comes in, right? The data comes in and now we're ready to study what actually happened during that two week period. So with the first student, interestingly, during the course of the PDSA, that daily attendance rate did go up. Right? And he was actually, he did miss a couple days, so it wasn't perfect, but he brought a note and there was actually a medical diagnosis. There was like a excuse reason for those particular days. Right. The second student was that student I was just referring to. So it was, his attendance was so poor that weren't even able to do the interview. That happens that you know, in real life. Third student's, this was a real success story. She was a part of her, the plan that she designed. She was meeting with one of the staff members at the school she attends that she chose one-on-one at the start of the day and she had significantly increased attendance during this two week period. 0:13:04.0 John Dues: And then the last student had this initial bump early in the PDSA and then had four straight sort of missed days at the end of that two week period also due to an illness, due to the flu. So you know, four kids, one uh two kids, pretty good success. Two kids still had some absences throughout the period. And then one kid sort of really didn't break the cycle. Nothing changed. And in fact the interview didn't even occur. Which means there was also no intervention that occurred with that particular student. Even so, with the student where we couldn't do the interview during that period, part of the plan was to get him a more reliable bus stop and we actually were able to change his bus stop, communicate that to the family and then that still didn't lead to increased attendance. And that's, you know, when you, I think when you work like this too, when you are sort of a policymaker or politician and you make these proclamations, we're gonna decrease chronic absenteeism or to cut it in half. And then you say, okay, well here's four students. Do that in two weeks. Do that over the course, just two weeks, just 10 days. How hard could it be? Right. [laughter] You see, you see just how hard these things are in reality. Right. So can't just make these proclamations. 0:14:32.9 Andrew Stotz: And is that part of what you're trying to do also in this process is get people to, you know, I mean, obviously what you'd love is to be able to come up with solutions from these four students. But really what you also are identifying is the other side of that. Wow, this is even harder than I thought. 0:14:50.2 John Dues: Yeah. And I, you know, with the people that work in schools, like the folks that are on this improvement team, none of this is gonna be a surprise to them. 0:14:57.3 Andrew Stotz: Yeah, they already know that, I guess. 0:14:58.6 John Dues: They already know. 0:15:00.3 Andrew Stotz: Yeah. 0:15:00.4 John Dues: Because they're on the front lines. I mean, they already know knew this is, you know, multi layered, challenging problem to address. But on the flip side, there were some pretty encouraging signs that getting, we call it getting proximate to students, individualizing some of those interventions and then including the student in that attendance monitoring and the intervention that it, you know, like I said, there were some success stories. So that first student I talked about, he went from 52% attendance to during the intervention period, it jumped up to 70%. So, you know, it's a short time frame, but a positive sign. That second student that I said that, you know, we never even got to do the interview with, he actually got quite a bit worse. So he had something like 37% attendance and that dropped 10% during that two week period. And then that third student that I said was a real success story, she went from 75% attendance to 96% attendance. And 96% attendance is good. And then the last student, she was the one that I said, you know, there was an initial bump and then kind of fell off, due to the flu at the end, she basically stayed the same. Like she was at right around 56% attendance and stayed right in that mid-50s range during the intervention. 0:16:19.8 Andrew Stotz: And just for, if a listener or a viewer has come in just on this episode and they're trying to understand where we're at, it's maybe you could talk a little bit about what you're doing in the sense that someone may look at it and say, wait a minute, this is just some anecdotes and how does that help you? And then on the other hand, one of the lessons in the business world that people sometimes say these days is do things that don't scale, which is counterintuitive. But what they're trying to get you to do is focus in, on getting it right with a small number of people before you then, you know, decide to go to the next level. So just maybe just give a brief of where it's at in this whole process. 0:17:04.8 John Dues: Yeah, I mean, I think. I mean, that's the whole point of the PDSA. The counterintuitive thing is that while you want to improve things for all students, you may start by working with a single student or a single classroom, or in our case, you know, four students. So, you know, the good thing is, is that what you could possibly do out of a cycle like this is, and this is only two weeks. But there's significant learning. And so what you would then do with cycle three, perhaps if the team decided this was what they're gonna do, is make some adaptation to this process, and if you were feeling confident that the adaptation was gonna work, then you could possibly. It's pretty early cycle two to start spreading this real wide. But I mean, you could spread this, you know, if you wanted to, to instead of four students, maybe you wanna try 10 students, something like that. Right. And in that way, and that's the basic idea, is to go from one student to one classroom of students to maybe one grade level of students to a whole school, perhaps if some type of idea is working really well. But the thing is, is that the whole mantra is, I lost my train of thought. Start small, learn fast. That's the mantra. Right. 0:18:23.7 Andrew Stotz: And then the other question I would have is, to what extent is this, you know, just subject to the Hawthorne effect in the sense that we knew in the many years ago that when they increased the intensity of the light, the workers did better, and then when they reduced the intensity of the light, the workers did better. So it was just that somebody was paying attention to the workers and the result was they appreciated that and so they did better. 0:18:53.9 John Dues: Yeah, I mean, that's possible. I mean, I would say... 0:18:57.0 Andrew Stotz: Which of course. Which of course may be the solution anyways. Right? You know, like, geez, if a teacher was... If each student was greeted by a teacher who cared about them and said, I'm so happy to see you, and it's great that you made it on time. Let's get started. I mean that could change the life of some people for sure. Including me. 0:19:13.7 John Dues: Yeah, I mean, I think, you know, like the girl that went from 75% to 96% attendance during the intervention. I wouldn't say, oh my gosh, we're gonna do this school wide now, but what I would say is, wow, that worked for that two week period. 0:19:25.7 Andrew Stotz: We're learning. 0:19:27.5 John Dues: It was relatively easy to do on a daily basis, so let's do more of that. Right. And also another thing you can think about is when you run PDSA cycles and you, let's say you do have really great success on whatever that thing is and you've spread it throughout your system. But now the priorities have changed. There's some other thing that really needs intensive intervention. One thing you can do is sort of as the 10th step in our improvement process is hold the gains. And so you often can then check back in on that thing in a month or two months and just see what the data says. Did it deteriorate because we're not paying as much attention to it or because we put that thing in place and left it in place? Although we're not as hyper focused on it, is it still sort of continuing on in a way that's at least acceptable to us? 0:20:22.3 Andrew Stotz: I just had an idea. Why don't we put a finish line and a countdown clock and a checkered flag and cheer every student as they get over the line? [laughter] 0:20:35.0 John Dues: Yeah, that would be great. That would be great. The problem is, is the cheering isn't the thing that's preventing them from coming to school. 0:20:45.1 Andrew Stotz: Yeah. 0:20:46.1 John Dues: Maybe like the cherry on top, but you know. 0:20:49.4 Andrew Stotz: Exactly. 0:20:51.6 John Dues: So, so it's tough. Yeah. 0:20:52.2 Andrew Stotz: Great, great example of where superficial things that outsiders see may not really connect with the real trouble that they're struggling with. Yep. 0:21:01.5 John Dues: And remember, the student's not the only part of the process. The people, the staff that were doing these interventions, they reported that this was like a really powerful experience for them. Most of them haven't been through a PDSA cycle before. 0:21:18.6 Andrew Stotz: Right. 0:21:18.6 John Dues: So this. 0:21:20.3 Andrew Stotz: Maybe I was, slogans and exhortations is what I was just talking about. 0:21:24.8 John Dues: Right, right, right. Yeah. But they felt pretty confident that doing more of that thing was a good idea coming out of cycle one and then this second cycle. Now, with that being said, one of the things that we've also discovered is that there's some required intervening that has to happen as kids meet certain thresholds that are required by the state of Ohio. And so I think I mentioned this before, that one of the things that we're doing as a part of the project was mapping out the intervention process in place at each campus. So while the benchmarks are the same for when you need to do that, the how and the who and the when, that there's variation in that. So right now we're taking like each of the campuses mapped out their intervention process for attendance, and we're taking a look at that. And so what we're actually gonna do in the next cycle is work to put together a more standardized approach to these intervention teams. So, and that... And you get that from the team, you know, you're sort of talking about, you know, as we get to the Act. 0:22:38.4 John Dues: I think I've talked about this before. There's sort of the three A's. You can adopt this into your system, write it down in a manual or whatever, you can adapt it, change it a little bit, or if it's really not going well, then you abandon it. So in this case, there's an adaptation where we're gonna sort of shift gears and work on this process mapping and get that put in place 'cause the team feels like that's the highest lever, next thing to do, basically. 0:23:06.5 Andrew Stotz: And is that. Have you already mapped out PDSA 3 now? And you're in that process? Is that. And that's what we're gonna talk about next one, or where are you at with that? 0:23:15.5 John Dues: Yeah, so I think looking at the process maps would be interesting because you can sort of assume that things happen relatively similarly, you know, especially in a small school system like ours. But you're gonna see that there's... And it's not right or wrong necessarily, but there may be a sort of like, again, a better way to do things because there are many... There's sometimes many people involved, many processes, many forms. And so, yeah, we're gonna look and see, basically, is one more efficient than the other, is one more effective than the other, that type of thing. 0:23:51.4 Andrew Stotz: Okay. 0:23:52.3 John Dues: Yeah. So a lot of learning, you know, I mean, I think, and you know, again, this takes time. But, and we're still sort of in that "define the problem" step. But again, the fact that we're studying the problem, the fact that we're talking to kids as a part of it, we're actually learning from data coming from what's happening on the ground. The ultimate solution or set of solutions we come up with are gonna be much more robust, you know, and they're gonna be much more sort of durable into the future, anti-fragile you know, into the future because of this work versus, you know, the typical fly by night. Let's have a pizza party on Friday to encourage kids to come to school, that just... There may be an initial bump, but it's just, this has no durability into the future. Yeah. 0:24:44.8 Andrew Stotz: Great, great. Well, I like that. And I got excited 'cause I thought, oh, maybe we can come up with some incentive or something. But what I see is that the challenge is how do you make it durable? So I like that word. And this was a good discussion on that. 0:25:01.8 John Dues: Yeah. Well, I was just gonna say the other point I would make is, you know, sometimes you can plan, plan, plan, but that, you know, at any point of an improvement process, you can use a PDSA cycle, start running an experiment and start gathering information right away. Just do something, you know, thoughtful, but do something. Don't plan in a room when you can go out and get actual, run actual experiments and get back real data. 0:25:27.5 Andrew Stotz: All right, and one other question I had that just came to my mind is what is the value of doing this in such a structured way as the PDSA versus Oh, come on, John, we're testing things all the time, you know, and let's say that to some extent they are, right? We all are testing every day. Why is it important that it's done in a structured way, in a documented way? 0:25:50.8 John Dues: Well, I mean, one, you have a historical record. Two, you know, we had four. So there's one PDSA cycle, but actually there's four different mini experiments happening, one at each campus. And if you didn't write it down like the guy does that's designing these, every one of the experiments would have been different. And he really thinks through step by step. Okay, put this number here. How are we gonna define that? There's a validated list of definitions of that type of attendance issue that day. Because if you don't have all that stuff, then there's no way to analyze it after the fact, or at least it's a lot less, a lot less efficient. 0:26:28.3 Andrew Stotz: And the learning could be lost too. 0:26:30.1 John Dues: Learning could be lost. And you know, I would venture to guess that, you know, if you run a sort of an experiment haphazardly, especially if there's multiple locations, the people sort of, their definition of the thing that's being measured is gonna vary too. 0:26:45.0 Andrew Stotz: Yeah. 0:26:45.5 John Dues: Almost every time. Almost every time, even subtly. 0:26:50.9 Andrew Stotz: All right, well, that was a great discussion. And on behalf of everyone at the Deming Institute. I wanna thank you again for this discussion and for listeners, remember to go to deming.org to continue your journey. You can find John's book, Win-Win, W. Edwards Deming, The System of Profound Knowledge and The Science of Improving Schools on Amazon. This is your host, Andrew Stotz, and I'll leave you with one of my favorite quotes from Dr. Deming. People are entitled to joy in work.

11 snips
Mar 10, 2025 • 32min
Don’t Be Limited by Quality Management: Misunderstanding Quality (Part 13)
Bill Bellows, a quality management expert with 31 years of experience applying Dr. Deming's principles, joins host Andrew Stotz to unpack critical insights from the Misunderstanding Quality series. They discuss the transformative impact of viewing quality through a broader lens, analyzing the Red Bead Experiment's significance in quality management. Bill emphasizes the importance of continuous improvement and understanding system variation, while advocating for fostering a feedback-rich culture to empower individuals and enhance overall performance.

31 snips
Mar 3, 2025 • 42min
Do Specification Limits Limit Improvement? Misunderstanding Quality (Part 12)
In this discussion, Bill Bellows, a quality improvement expert with over 31 years of experience applying Dr. Deming's philosophy, shares insights on how specification limits can hinder progress. He reflects on Stephen Hawking's captivating lecture, urging listeners to avoid self-comparison and embrace personal growth. Bill challenges conventional quality standards, promoting a mindset of continuous improvement over mere compliance. He also critiques change management strategies, emphasizing the need for proactive adaptation and customer satisfaction in quality pursuits.

Feb 24, 2025 • 29min
Plan-Do-Study-Act: Path for Improvement (Part 7)
Can you use Plan-Do-Study-Act (PDSA) during the information-gathering phase of an improvement project? Yes! Join John Dues and host Andrew Stotz as they discuss how John's team used PDSA to learn more about chronic absenteeism, their surprising findings, and what they'll do next. TRANSCRIPT 0:00:02.8 Andrew Stotz: My name is Andrew Stotz, and I'll be your host as we dive deeper into the teachings of Dr. W. Edwards Deming. Today, I'm continuing my discussion with John Dues, who is part of the new generation of educators striving to apply Dr. Deming's principles to unleash student joy in learning. The topic for today is powerful learning with the PDSA cycle. John, take it away. 0:00:25.5 John Dues: Yeah, Andrew. It's good to be back. For the past two episodes or so, we've been working towards defining the problem of our chronic absenteeism issue, of course, we have a problem with chronic absenteeism, but we're trying to narrow that down and get a more specific problem statement. Last time we talked about how our improvement team, basically, had come to the conclusion after a few weeks of study that we didn't have enough information to write that specific, precise problem statement. So what we decided to do, and we started looking at this last time, was we started to gather additional information through a Plan-Do-Study-Act cycle. So that's what we'll focus on today, is this first PDSA cycle, and I think it's good to know that you can use PDSAs to run an experiment to test a new idea, but you can also run a PDSA to gather more information. Those are both very worthwhile uses of the PDSA cycle. So I go to share my screen just so I have that model up so that people who can see it, for those that are viewing. Can you see that now? 0:01:33.8 Andrew Stotz: Coming up. Okay, we can see it. 0:01:36.6 John Dues: All right, great. So you remember, we've been working through this four-step process for those who are hopping in for the first time or as a review for those that have been following along. So we have these four steps: set the challenge or direction, grasp the current condition, establish your next target condition, and then an experiment to overcome obstacles. And remember, we've been working through this team, that's a combination of people working in the system, people who have the authority to actually change the system, and then the System of Profound Knowledge coach. So I think that's a pretty powerful combination of people, and that's our team here working on this chronic absenteeism problem. You also remember that we have this long-range goal that this challenge that is to improve our chronic absenteeism from right around 50% to down closer to 5%, and I don't know if you remember this, but a number of episodes ago, I showed you the data we had over time, and we just had three years of data. Since that time I showed you that first run chart, I've actually gone back and added chronic absenteeism rates for our schools going all the way back to the 2016 - '17 year, and I think it's worth it to just take another quick look at those rates over time in a process behavior chart. 0:03:00.2 Andrew Stotz: Exciting. 0:03:01.5 John Dues: So, yeah. This is our chart. So we add more days so why not display it in this way. So what this chart is, is again a process behavior chart, we have school years going back to the 2016-'17 school year, and then through last school year. And we have the blue dots displaying the chronic absenteeism rate for each of those school years across our school system, and then the green is... The green line is that central line, it's the average of all years, the red lines are those natural process limits that sort of tell us where we can expect our data to fall given that this is a predictable system. So you can see right off the bat, something that's pretty obvious is that the first four years of data are below that central line, and then the last four years of data are above that central line. And of course, it's not too hard to sort of recognize that the pandemic happened towards the end of the 2019-'20 school year, and then sort of... We were all remote heading into that 2021 school year, and then for a number of years after we were in remote or hybrid, and so you can see very clearly that while there was chronic absenteeism in our system prior to the pandemic, after the pandemic, it exploded and it has not subsided. 0:04:28.7 John Dues: So in a typical year prior to the pandemic, we were somewhere around that 25, about a quarter of the kids give or take, depending on the year, of the kids were chronically absent, and then after the pandemic, we can see it sort of... Or at the begining of the pandemic, explodes up and then has settled around this, right about 50% average. 0:04:51.1 Andrew Stotz: And the fact that it's remained at this much higher level of, let's say 50-55% tells you that there's like... It has had somewhat of a permanent impact, whereas some people may think that the COVID situation caused a spike in chronic absenteeism up to 70% or whatever that number was, and then it came back to normal. But it's far away from normal. 0:05:26.4 John Dues: Yeah, and I haven't done a deep analysis. But in addition to the chronic absenteeism, the National Assessment of Educational Progress, which is like the gold standard, the report card for the nation, a nationally known test given every couple of years, that data shows that the 4th and 8th graders that take that test across the country in ELA and math, the scores are down coming out of the pandemic as well and have not rebounded. So I think that data is important. I'm not necessarily saying one way or the other, what we should have done, but what I am saying is like when we make decisions like shutting down schools, it's not just a decision that has an impact in the moment, there are ramifications on an ongoing basis. And we should sort of take that calculus into consideration when we're deciding what to do in a situation like that. 0:06:20.0 Andrew Stotz: And this also shows that you're taking on a pretty serious challenge because... 0:06:23.8 John Dues: Very serious. Yeah. 0:06:25.0 Andrew Stotz: Yeah, it's serious for the students, but it's also serious in the sense that it's been lingering at this very high level of chronic absenteeism, so, okay. 0:06:37.0 John Dues: Yeah. 0:06:37.5 Andrew Stotz: Shocking. 0:06:38.1 John Dues: Yeah, it is pretty shocking. 0:06:38.7 Andrew Stotz: That's not happening in Asia. 0:06:40.6 John Dues: No, and it's... I think a number of places in the United States, the learning chronic absenteeism has bounced back, but in the places where you expect where there's, especially high concentrations of poverty and things like that. It's sort of remained a serious issue even depending how you mark the end of the pandemic, two or three years after the primary part of the pandemic anyway. The height of the pandemic, if you will. So, ongoing challenges for sure. So what I said was that the team was going to run this initial PDSA cycle to gather more information, of course, there were some initial thoughts on why kids were missing so much school. We've talked about these transportation, different expectations that have been set for when to stay home, family and instability, those types of things. But again, we want to further test those assumptions early on in the project. So the key question that we were looking at is, for this first PDSA cycle, at least was will the combination of a what we call an empathy interview, which is just like where we sit down with a student or the family and try to better understand what's going on, and then daily attendance tracking was the other part of this, will that lead to a modest increase in the students average daily attendance rate during the period of the intervention. 0:08:11.9 John Dues: So even though we weren't necessarily testing a change idea, there was this sort of like... We framed it as a modest intervention in terms of sitting down with the kids and then doing this daily tracking and showing them the data. And a key part of this plan phase is we had all of our team members predict what they thought would happen with the four students that we chose to have those interviews with and track the daily attendance of during Cycle 1. So we had everybody really think through, "Okay, what do we think will happen when we put this plan in place?" And that's going to be really important because when we actually run the test, we want to compare the predictions to what actually happens, and that's where a lot of the learning happens from a PDSA cycle. 0:09:02.9 Andrew Stotz: And just for the listeners or viewers out there, why is it important to do that? Some people would say just do it and find out what the result is. 0:09:12.3 John Dues: Well, if you don't take a stance basically before the intervention happens or before the plan is put in place, then there's no learning that can really happen because whatever happens happens. But you didn't sort of say, "Here's what I think's going happen." And a lot of times, we quantify that prediction, and then what you can see is the difference between those two things is not only the learning, but it's also an indication of how well you understand your system. So what I mean is, if we put an intervention in place and I say, "Okay, I think this is going to have a 15% increased impact on whatever it is, a test score or attendance in this case," and then it has no impact, then I don't have an understanding really of what's going to work to fix whatever I'm trying to fix. But if the prediction bears out and it's pretty close to what actually happens, then that means, oh, I have a pretty good grasp on what's going on in my system. Yeah, kind of makes you put a stake in the ground, and it makes you mentally when you're doing it, it makes you think. 0:10:19.0 John Dues: Look further ahead and say, "Okay, if I do this, do I actually think this is going to be effective?" And you can also see the team's thinking. Some people might think this is going to be very effective, and some people may think it's not. Some people might think it'll work with some students, but not other students, and it gives you that picture black and white before you actually run the test. 0:10:37.8 Andrew Stotz: And in academic studies, it's really important to identify your end point that you're testing for. Otherwise, you run the risk of switching your end point as you get through your research because you're grounded initially. 0:10:53.2 John Dues: Right, exactly. Right, yep, absolutely. So in this plan, what we did was, this... We had parent conferences coming up, so we just said, that's a natural time to sit down with these four students that we chose at parent conferences. So at the end of November, we did that, we reviewed the data, we sat with the family to discuss some of the causes of the attendance challenges. We explained the plan to track attendance for 15 days coming back from Thanksgiving break. And then part of the plan was collecting that quantitative data, like the actual attendance rates each day for each kid, but then it was qualitative too, because we were asking the family on the front end, what was the sort of overall cause of the problem. And then we were asking the actual student every day like, "Oh, on this particular day, why were you absent, or why were you late, why did you miss school?" And we were tracking that across 15 days, so it's a relatively short time period, 'cause we don't want to go off on some grand experiment and then find out three months from now that our intervention wasn't effective. 0:12:02.5 John Dues: So that was the plan. And then the next step in the PDSA cycle is the do and that's just like it sounds. So we ran the experiment for 15 days and then started gathering that data. So what we found was that in two of the cases, transportation challenges were in fact the primary issue, in the third case, it was sort of transportation, but that was exacerbated by a family that was homeless during this period, and then in the fourth cause, or in the fourth case, there was actually some sort of anxiety issues with coming to school. So you can see three very different causes just across four students. So again, if you don't have that picture, then it's very hard to sort of design the right type of interventions 'cause you don't really know what's going on. You have assumptions, right? So I don't think it's rocket science, but the team learn that there are so many layers to this attendance challenge, and even for a single student, there's often multiple factors rather than some single explanatory variable. And so you have to sort of uncover that, and I think the key thing was that holding these empathy interviews, just these four interviews allowed us to challenge some of our initial assumptions. Like maybe a family doesn't value attendance, that didn't seem to be the case, at least with any of these four students who are facing some serious challenges on the home front. 0:13:48.6 John Dues: But it wasn't like families didn't value school or having their kids attending school, there're just major obstacles. And so digging deeper allowed us to explore these various causes with the families. Another thing that was interesting is that as we talked with the team about... As the data came in and what they were doing, we also learned that we need a better, more systematic process for intervening with chronically absent students, that's everything from reviewing the data, identifying those chronically absent students early on in the school year, for those that we're required to do something like file truancy for those processes and then monitoring attendance, there's various requirements public schools have on that front. Every school is... They have a system in place, and they have a team in place, and they have a process in place for these different things, but they're all doing it differently, and so there's not a standardized process across our system. And another thing is, some parents didn't even realize that they may have a general idea that the attendance isn't great, but don't... Most parents don't actually realize what is the actual attendance rate of their child, how far off is it from what's considered exceptional or at least okay attendance. 0:15:17.6 John Dues: Almost nobody has that. Those numbers at the ready. Another thing that has happened as we studied the data was that there was a really wide variation in terms of the difference in student daily attendance between the period of the intervention and end of the school year up to that point. So there's basically a lot of learning going on with just a very simple four student experiment. So even though the predictions weren't perfect, and one thing with the predictions is, this is Cycle 1, so what should happen over time as we gain knowledge about our system, is that the predictions get closer and closer to what actually happens because we're learning with every PDSA cycle that we're running basically. So the last part is, then you act, so we've done the plan, we've done the do, the study, and the act, and the way I frame this is that you have three As that you can choose from in the Act segment. You can adopt that change that you've tested, you're going to adapt that into the next cycle, or you can say this is not working at all and you can abandon it and just do something else. 0:16:34.2 John Dues: Yeah, those are the three options. So what we've actually decided to do, what happens in a lot of early tests, is we're going to adapt Cycle 1 into Cycle 2, and in fact, Cycle 2 has actually already started. But the aim of Cycle 2 now is we're going to increase the extent to which we're involving students and families in the data collection process, and we're going to hold what we call like a... We call this a 5 Whys Empathy interview with each student that we've identified, and then use that to create a plan for a PDSA that's specific to that one student, basically. So it's going to be very hyper-focused and so we're going to collect this data for two weeks, we recognize that doing this intensive of a process with the entire school or the entire group of students that are chronic absent probably isn't possible, but what we're doing is learning so much from this, that seemed like we're going to take another step to learn more and work with the individual student to set up the next round of interventions. 0:17:49.4 Andrew Stotz: And what are you guys expecting for an outcome? You know, talking about prediction? I don't know. Should we think about where are you going to be in one year or two years, three years? 0:18:00.7 John Dues: Oh no. It's very closely tied with the PDSA. So if it's a two-week PDSA, then we're actually saying, what is that the average daily attendance going to be for that two-week period? 0:18:11.7 Andrew Stotz: Yep. Yep. 0:18:14.3 John Dues: I mean. It's very tightly closed. Yeah. 0:18:14.8 Andrew Stotz: What I'm saying though, let's just take the attendance levels that we've seen in the chart, let's just talk about annual and let's say, "Okay, one year from now, two years from now." 0:18:23.7 John Dues: Oh yeah. That's right. Oh I see. 0:18:26.7 Andrew Stotz: Are you... Is it right to make a prediction about where you think you would be or is that not the right way to do it? 0:18:32.0 John Dues: I think it's too early in the process to make... I see what you're saying now you're talking about the actual... That overall system measurement. Yeah, I think it's too early to make a prediction on that, if you were holding a gun to my head and making me put money down, my prediction would be right in line with what it is this year, basically. I would think it... Because it's a stable system. Those last four years, all bounce around 50-55%, like you said. So my bet would be on 50-55%. Because... 0:19:11.2 Andrew Stotz: And what would... How would things change for you or the school? Let's just imagine hypothetically... I'm going to push back a little bit here and just get some thinking, but from a hypothetical perspective, let's say a new school opened up and their number one focus was chronic absenteeism, and they decided that the most important thing for them is to solve that problem. And they had been doing it for a while in other locations, and now they've come in, now you're competing with them. They're an option for some people, and they're just the place for others, and let's just say that they have optimized for chronic absenteeism and it's down to 10% at their school. Does that change how you think about what you're doing? Again, it's hypothetical, but I'm just curious. How does that... 0:20:01.3 John Dues: No. Not me, because this is what our system produces right now, so... Yeah, I think I would say I don't have enough information to make a prediction about what the ultimate outcome measure will be. 0:20:19.4 Andrew Stotz: And I guess you could say this is what our system produces in this area based upon what we see as important, right? Like this is... 0:20:32.4 John Dues: Yeah. That's fair. 0:20:33.2 Andrew Stotz: And there may be another area that you think is very important in that those numbers in that area may be very, very different from that, but another... Go ahead. 0:20:43.7 John Dues: Yeah, well, I was going to say, so in this attendance team, there's... The empathy interview is going on with these four students, and then in the Act phase, we also said we're launching an effort to make the intervention process more consistent across all of our schools. And we're starting by understanding the process that's in place right now, but this team is not the only team pulling levers that ultimately could impact attendance. I think they're pulling important levers, but there are other improvement teams across the school system, for example, I think I mentioned this maybe a few episodes ago, transportation. Transportation did come up like we thought it would in three of the four interviews. So, and we have mentioned how poor the bussing has been in Columbus for the last several school years, but especially last year and this year. And so we're working to see can we do something significantly different next year on the transportation front. 0:22:00.1 John Dues: And I think if we can pull that lever, that also... But that would be a change to the system, like a very significant change. Now, if that went through, I would be much more confident about making a prediction about improvement on the attendance front next year, so. 0:22:17.9 Andrew Stotz: If I look... 0:22:19.2 John Dues: It's not going to solve our problems though. Yep. 0:22:21.2 Andrew Stotz: Yeah. If I look at my roasting business for coffee, if I replace my pretty much manual roasting machine with a fully automated high-tech one, it's going to have a massive improvement in variability. Invariability is going to reduce way beyond what our current system can produce and it will happen in a day, right? When that happens, it'll happen in a day. 0:22:47.4 John Dues: Yeah. 0:22:52.9 Andrew Stotz: And being late for class is a big bag-a-boo of teachers here in Thailand, particularly at universities where I go to, and it's a problem and nobody likes it and students come in late and all that. But I solved that problem with just the twist of my finger, one twist of my fingers, and I solved it. What was that twist? I locked the door. And then as the students were outside waiting to come inside, I would eventually go out and I'd say, "Look, it's important to me that you're on time. I'm going to lock this door. If you can't make it... You got to figure out how to make it." I know you got two hours of traffic and you're coming in from abroad, or you're coming in from outside of the city, I know that your parents don't have the money to pay for a car for you and you got to take the subway or you've got... I know. Everybody's got their circumstances, but you're making an effort to get here, I want you to get here on time. 0:23:52.4 Andrew Stotz: The next class that I have, everybody's on time. So one of the questions I have, and this is, again, push back is, some people may look at this and go, "Oh. Come on. All this work. Why don't we just massively prioritize and focus." Let's just say that... Let's just say, I don't know what the answer is, but let's just say that the principle of the school, all the teachers and all the students gather out in the front area at the time that you're supposed to be at school, and there's a band playing. Everybody's cheering. We're getting ready. Whatever that thing is. I remember a boss I had that used to have a stand-up meeting every single morning, and you didn't miss it. And so for some people who are listening, they may think, "Oh, come on, John, you're going through all this stuff and it's not going to improve. Why aren't you just taking more aggressive action right now." 0:24:48.9 John Dues: Well, I didn't say I was going to improve it, I just said I wasn't going to make a prediction. 0:24:51.9 Andrew Stotz: Yes. Yes. Sorry. I didn't mean... 0:24:53.8 John Dues: So yeah. What would I say? I think when you have... So the person that is in charge of this project, for example, I don't know that anybody's ever gotten better results while a principal of a school in Ohio with the challenges that he faced. So this is not people that aren't driven to get extraordinary results. This is a multi-faceted problem that is incredibly tough to improve, and when I have the view point of sitting down with the students and hearing what is... Keep the obstacles are... It is just a very hard thing, and I'd say one of the reasons we're pulling that transportation lever early, or at least attempting to is because that's such a big part. Again, that's not going to solve everything. But like I said, if we were able to pull that lever and it's a big if because we get no funding for transportation. All the funding flows through the school district, so that's a massive obstacle. Millions of dollars that we aren't allocated to do this service, someone else is. So right now we don't have control over it, and so those are the types of obstacles, we can't just buy buses, for example. Because... 0:26:36.1 Andrew Stotz: Yeah. And it's like you got 50 problems that you're trying to... 0:26:41.7 John Dues: 50 problems. 0:26:41.7 Andrew Stotz: And 50 more constraints that you're operating within. 0:26:45.9 John Dues: Yeah. And so we were attacking it from multiple angles, so we were attacking it on the attendance front with kids, at the State House with funding, with trying to see if we can set up our own transportation system even without that funding. So there's many, many levers being attempted, but they are not quick and easy, simple, so. 0:27:12.8 Andrew Stotz: And for a listener who's listening to this, who may not be the CEO of a company, let's say who's got resources he can allocate or she can allocate, they also may be in a situation like, "This is all I can impact. I can impact this area, but I have to be realistic about what resources I have." 0:27:33.6 John Dues: Yeah, and I think one of the things we're doing too, we don't have rose colored glasses on, we're saying, even if we did fix this transportation system, and that's a big if again. That doesn't mean that the chronic absenteeism problem is going to be solved. Maybe it's significantly better, maybe it goes down to 30%, 35%, if we had a good transportation system, but that still means... And even before transportation was such an issue, even before the pandemic, these rates were still... The quarter of the kids who are so chronically absent, that's way too high, that's way too high. So we recognize that, but these are very, very thorny problems to try to improve. 0:28:15.0 Andrew Stotz: Yeah. Well, and also you're trying to make lasting change too, so. 0:28:18.6 John Dues: Lasting change. Yeah. 0:28:19.6 Andrew Stotz: Yep. 0:28:19.7 John Dues: Yep. Yeah. 0:28:22.1 Andrew Stotz: Okay. Great. So I'm going to wrap it up there. And thanks... 0:28:23.3 John Dues: Yeah. Absolutely. 0:28:24.6 Andrew Stotz: And thank you for, on behalf of the Deming Institute, and I want to encourage all the listeners out there to follow what John's doing and what he's talking about, and of course, go to Deming.org to continue your journey. You can get his book, Win-Win, W. Edwards Deming, The System of Profound Knowledge and the Science of Improving Schools on amazon.com. And this is your host, Andrew Stotz, and I'll leave you with one of my favorite quotes from Dr. Deming, people are entitled to joy in work.

33 snips
Feb 18, 2025 • 33min
To Improve Quality Don’t Measure Quality: Misunderstanding Quality (Part 11)
Bill Bellows, a quality improvement expert with over 31 years of experience applying Dr. Deming's principles, joins the discussion to debunk common misconceptions about measuring quality. He highlights that true improvement doesn't stem from mere metrics but from understanding functionality and customer needs. Bill shares engaging examples illustrating how teamwork can falter when individual interests overshadow collaboration. The conversation emphasizes creating holistic, desirable solutions in organizations to ensure both quality and profitability.