
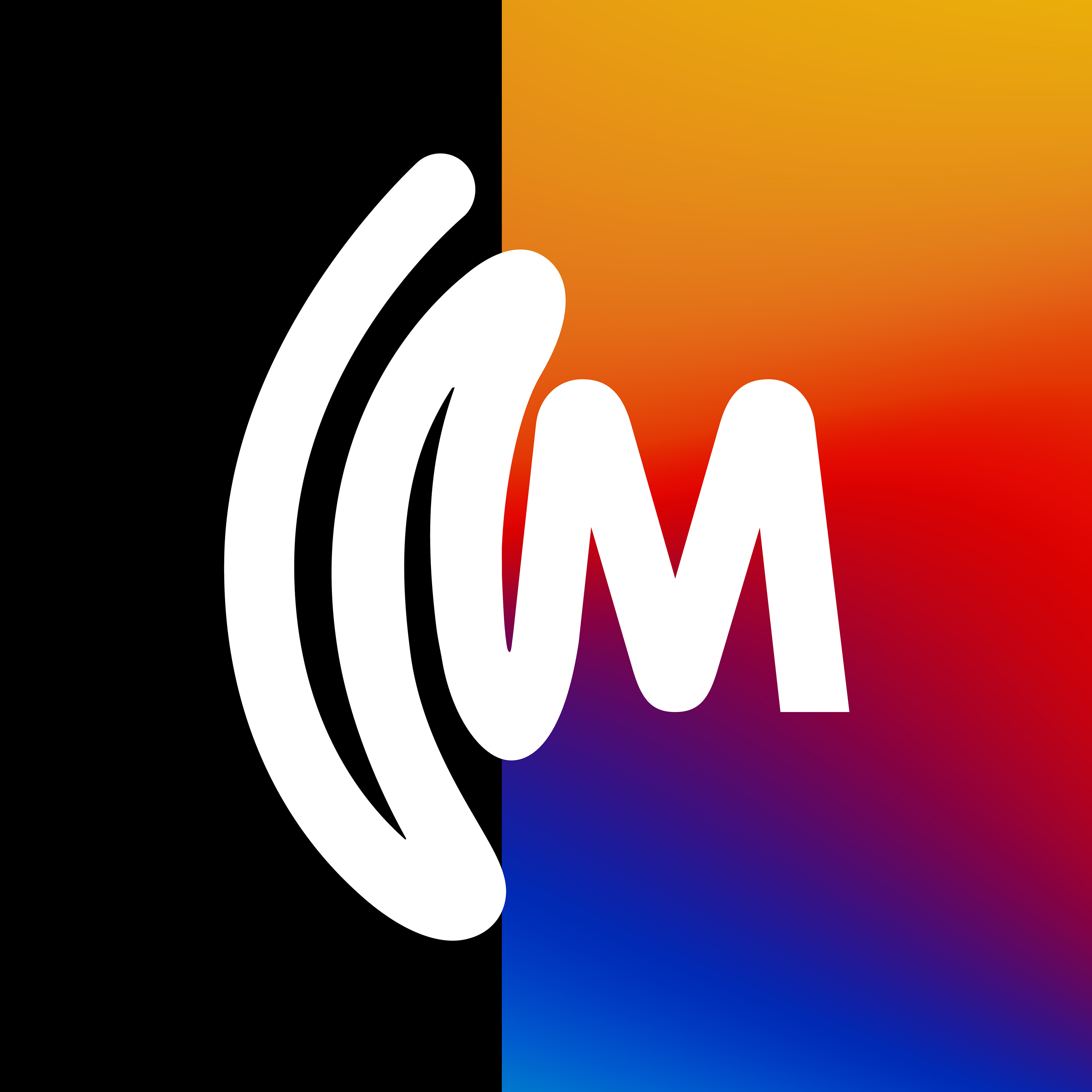
Making Chips Podcast for Manufacturing Leaders
MakingChips LLC
Manufacturing is tough—but you don’t have to go it alone. If you're leading a manufacturing business, you face constant pressure: staying competitive, adopting new tech, managing people, and driving growth. MakingChips helps you tackle those challenges head-on.
Since 2014, we’ve been equipping manufacturing leaders with the knowledge and inspiration they need to succeed. With hundreds of episodes and over a million downloads, MakingChips is a top resource for the metalworking nation—covering leadership, operations, technology, and workforce development.
If making chips is part of your daily grind, this is your podcast. Join hosts Nick Goellner, Mike Payne, and Paul Van Metre for real talk on the issues that matter most.
Since 2014, we’ve been equipping manufacturing leaders with the knowledge and inspiration they need to succeed. With hundreds of episodes and over a million downloads, MakingChips is a top resource for the metalworking nation—covering leadership, operations, technology, and workforce development.
If making chips is part of your daily grind, this is your podcast. Join hosts Nick Goellner, Mike Payne, and Paul Van Metre for real talk on the issues that matter most.
Episodes
Mentioned books

Nov 12, 2019 • 37min
A Different Spin on Social Media Marketing for Manufacturers
Is social media marketing for manufacturers really worth the effort? How should you market your brand in general? It may be hard to figure out where you fit in the social media world and what content to put out. In this episode of Making Chips, Jim and Jason talk about why social media marketing can make a positive impact on your business. Their answers aren’t what you expect! Connect with us:www.MakingChips.com/contact Prioritize Self-Care above your business Jim and Jason had a scary Halloween—but not for the reason you'd expect. They were preparing to record a couple of episodes for the podcast. Instead, Jim was rushed to the ER with a case of Gastritis. Among other factors, severe stress is one of the things that contributed to his illness. Running multiple businesses and caring for unhealthy parents took a toll on him. The moral of the story? Know what’s going on with your body, and take care of yourself. As a business owner, you have an obligation to care for your company. However, it is impossible to do so if you aren’t healthy. Proper self-care should be the entrepreneur’s #1 priority. Jim is already active and watches his diet, but wasn’t limiting his stress. It was a wake-up call for him and he hopes that it’s a wake-up call for listeners as well. Social Media marketing to promote company culture A listener pointed out that he doesn’t believe a machine shop must do any social media marketing. He doesn’t buy it. He believes that it’s a total waste of time for an industrial company. After all, what aerospace engineer goes on Facebook to look for a manufacturer? While Jim and Jason point out and understand that social media isn’t for everyone, there are some important reasons to utilize Social media. Firstly, you’re not creating posts on Facebook to attract buyers. You are doing it to promote your company culture. You can promote new talent or offer a behind the scenes take of what your company does. Social media allows a business to share their values with the world. It is THE most effective way to do so—and costs you nothing but time. Facebook, Instagram, LinkedIn—where do you begin? As much as you may not want to give credence to the importance of the social space, they point out that people build careers in social media. Instagram influencers make thousands of dollars promoting services or products in posts. Instagram is a great model for the manufacturing space because it allows you to share visuals in a meaningful way. You can share photos of parts, people in your business, or of projects you’re working on. Or perhaps a short video of work in progress or a how-to piece. Whatever it is, it allows you to build an authentic connection with your audience. If you’re providing valuable information, social media marketing for your brand can certainly be worth the time and effort. LinkedIn can also be a useful tool to attract new talent. A new hire came across some of the content Jim had shared on LinkedIn. He saw that Jim was hiring a C & C Machinist, and messaged him about the opportunity. He already knew—based on their social media presence—that the company would be a good fit. And he was! Marketing isn’t a waste of time when done properly Marketing doesn’t necessarily reap immediate rewards as far as attracting new clients. However, the immediate reward is how it impacts your company. As you build a website or define a marketing strategy, you are defining how you want your business presented to the world. What are your values? What are your specialties? What is the #1 thing you want the general public to know about your company? As you’re building a vision for your brand it helps lay out the vision for how you operate your business. You differentiate yourself in the industry by being different, and marketing helps you portray what makes you special. If you stand out and exploit what makes your business different, you attract the type of customers that are the right fit. They emphasize the importance of finding a good marketing agency to guide you through the process. It can make a world of difference. Here’s The Good Stuff! Manufacturing leaders need to prioritize self care SIA latest news Social media marketing for manufacturers What can Instagram do for you? Is marketing a waste of time? Find a good marketing agency! What Upcoming episodes will look like A conversation with Peter Goguen of Xometry Tools & Takeaways ProShop ERP StoryBrand Marketing Xometry Titan Gilroy Zenger’s Connect With MakingChips www.MakingChips.com On Facebook On LinkedIn On Instagram On Twitter On YouTube Subscribe to Making Chips on Apple Podcasts, Google Play, Stitcher, or Spotify

Oct 22, 2019 • 47min
Why Manufacturing Leaders Should Employ Veterans with Andrea Biwer & Marne Deithorn
Making the decision to employ veterans may seem like a shot in the dark, but it could actually be the best hiring decision you will ever make as a manufacturing leader. Military veterans not only have the tangible leadership skills you need to grow and succeed in your business, but they also bring a rich set of attributes and experiences to the table. Making the transition from military life to a new, civilian career can be intimidating, however! Helping veterans thrive in their post-military chapters is what brought Andrea Biwer (Executive Director of the Des Plaines Chamber of Commerce) and Marne Deithorn (Director of Human Resources at the Des Plaines Rivers Casino) together to form the Veteran Boot Camp. Connect with us:www.MakingChips.com/contact The “Aha moment” that created the Veterans Back to Work Boot Camp Andrea knew there was a shortage in the manufacturing workforce, but she didn’t see it as an opportunity for veterans until she watched her son and his friends come back from their service in the marines and have trouble finding work. Joining with Marne (a veteran herself!) at the Rivers Casino, the two women helped lead the charge in founding the Veterans Back to Work Boot Camp. The ten-week program is built to help and empower veterans who have given so much to our country and to fill job opportunities within various industries - including manufacturing! A ten-week itinerary of life-changing self-discovery Over 250 veterans have applied to the boot camp since it began. 20 were chosen out of 85 applications for this past year’s program. While there are no set criteria for being accepted, Andrea and Marne explain that they painstakingly go through each application, looking for those they believe will most benefit from the experience and be committed to the learning opportunity. Those that aren’t accepted are still given access to the job fair put on by the Des Plaines Chamber of Commerce. Mentors come alongside the veterans, sharing their own mistakes and experiences. Topics such as Who are You?, Persona, and Introversion vs. Extroversion are covered, as well as interviewing skills and resume building. Marne explains that in the military, everyone is told exactly what to do - all the time. Veterans are used to a life where they are told what to wear, where to move, and what they should do in their job. Suddenly living in a world without constant direction can be daunting. The Boot Camp endeavors to help veterans find themselves again after identifying themselves as “the military” for so long. Employ veterans for their strengths and tangible leadership experience Andrea and Marne share that the veterans who leave the program are filled with newfound confidence and strength in their personal capabilities. The practical experiences they gain from the program, such as participation in networking events and community service projects, help give them a sense of purpose outside of the military. One of the greatest strengths of veterans is their desire for purpose - to give to something bigger than themselves. Veterans have so much to offer, and their military training and experiences have proven them to be men and women of integrity, loyalty, character, and principle. They know how to lead under pressure and how to build up those around them to greater achievements. They know how to make decisions. When you employ veterans, you aren’t just utilizing their skill-set, you are investing in the future. Don’t stereotype - we all have things we struggle with Unfortunately, there are many misconceived misgivings surrounding employing veterans. Firstly, veterans aren’t just line employees. Because of their military experience, they are ready for leadership positions at the get-go. While they may need to learn the details of a specific job, they already have the tangible leadership skills needed to succeed (know yourself, know your troops, and know your mission). Secondly, not every veteran has PTSD. Andrea and Marne warn against placing veterans inside a box of mental disorders. “That negative stigma is absolutely ridiculous,” they say. Everyone has something they struggle with, and not only military members have PTSD. If you find that one of your employed veterans has some type of disorder, help them find the encouragement and aid they need. Thirdly, not all homeless veterans have a debilitating habit that brought them to that condition. Again, everyone has struggles. Veterans are human too, and they deserve a chance. To learn more about the ways you can help give back to military veterans while also growing your business, listen to the episode! Here’s The Good Stuff! Veterans know how to make decisions! The inspired beginnings of the Veterans Back to Work Boot Camp. The three-fold mission of the Boot Camp. How do veterans benefit from a mentorship-based program? Overcoming obstacles on the road to self-discovery. Training built to inspire and create the future. Practical experiences make for a well-rounded education. Unexpected reasons you should employ veterans. How the manufacturing community can help make a difference. Overcoming the negative stigmas surrounding employing veterans. Tools & Takeaways Fifteen Benefits of Hiring Military Veterans Xometry ProShop ERP Text CHIPS to 38470 to subscribe to The Boring Bar This Week’s Superstar Guests Andrea on LinkedIn Marne on LinkedIn Veterans Back to Work Boot Camp Boot Camp Videos Connect With MakingChips www.MakingChips.com On Facebook On LinkedIn On Instagram On Twitter On YouTube Subscribe to Making Chips on Apple Podcasts, Google Play, Stitcher, or Spotify

Oct 15, 2019 • 1h 3min
Training for Performance - not Credentials with Montez King
Training to achieve top credentials has long been a goal of many in the Metal Working Nation, but what about training for performance? Montez King, Executive Director of NIMS, unpacks the power of training machinists to perform at their ultimate best. How do you measure performance? Listen to the episode to find out! Montez grew up on the rough side of the tracks in Baltimore - eager to pursue something bigger than himself when he grew up. Encouraged by a high school instructor to pursue machining, Montez found himself learning the tricks of the trade in his high school machine shop. Over the years in various manufacturing jobs, Montez endeavored to find solutions to the issues he found riddling the manufacturing industry - namely, the habit of companies to reward their employees for hoarding their expertise. As he climbed the industry ladder, Montez encouraged a paradigm shift towards a community rich in growth, teaching, and learning. Connect with us:www.MakingChips.com/contact Redefining the values: training for performance instead of credentials When Montez became the executive director at NIMS, he laid out a new mission for the organization - to train from the end. Manufacturers are always learning. Technology continues to grow at a rate that demands elite performance and an insatiable desire to learn. Montez explains that simply having a list of credentials doesn’t cut it anymore in an industry where performance equals compensation. Employers are coming up against unique problems every day that require quick and expert solutions. Performance has become the new measuring stick. NIMS helps companies train for performance with specific goals and standards in mind. When measuring performance, they determine whether or not an individual can operate within the responsibilities of their job description while drawing upon the competencies associated with that job. The training isn’t just for the sake of training. It’s training with a specific performance goal in mind. Empowering the standards while building the performance Manufacturing leaders know that they can’t wander aimlessly when trying to improve their teams. There needs to be a goal - a standard of achievement. NIMS takes this need for standards and applies it to their performance measurement, creating training methods that enable the trainee to meet the performance goals of the employer. Trainees leave with the ability to make an analysis of the task at hand and to apply their expertise based upon their best judgment of the tools, time, and needs within their environment. Montez makes it clear that standards should not be held above performance. The answer to the employer’s needs is the competent and consistent performance of the trained individual. Credentials are awarded to individuals who complete the training and meet the performance standards so that the trainee is recognized for their hard work, while also meeting the needs of the employer. It’s a win-win for everyone involved. It’s a three-way stop in the NIMS stakeholder environment In order to make the performance training at NIMS a true win-win, Montez has helped create a stakeholder environment in his company’s training methods. Using the image of three bars, each one stands for a stakeholder in the training: the employer, the trainer, and the trainee. Everyone is reaching for the same goal, and each one is held accountable for their part in the deal. Validation is achieved when the trainee can draw upon the competencies they have learned and can successfully apply them to the environment that their employer has defined for them. The employer is responsible for establishing the standards, the trainer is responsible for creating a training method that builds performance and skill, and the trainee is responsible for mastering the craft and competence in applying knowledge to real-life situations. All three bars have to measure up. When one falls short - they all fall short. NIMS is building an exciting opportunity for manufacturing teams at IMTS 2020 To Montez, performance measurement is preventative maintenance! In order to push the Metal Working Nation to the next level, NIMS will be hosting a one-of-a-kind challenge at the IMTS 2020 trade show. The goal will be to measure the performance of a team, since teamwork is such a vital part of the manufacturing industry. This PM will require multiple skill-sets to come together to design, create, and produce a task that will then be voted upon by the IMTS crowd. In accordance with the NIMS training methodology, the competition will include standards, inspections, and requirements modeled after real-life challenges. What’s the reward? You’ll have to find out at IMTS 2020! Here’s The Good Stuff! From Baltimore to NIMs - Montez’s manufacturing story. The detrimental trend of hoarding knowledge. Changing the culture and mission of NIMS. Measuring performance instead of credentials. Creating a win-win training method for employer and employee. The magic of entanglement in training. The importance of having standards and reliable methods. It’s the employer’s job to define the desired performance standard. NIMS is offering an exciting opportunity at IMTS 2020! Tools & Takeaways IMTS 2020 Rockford Rescue Mission Offers New Manufacturing Training Program Xometry ProShop ERP Text CHIPS to 38470 to subscribe to The Boring Bar This Week’s Superstar Guest: Montez King Montez on LinkedIn Biographical video on Montez’s journey to NIMS NIMS Connect With MakingChips www.MakingChips.com On Facebook On LinkedIn On Instagram On Twitter On YouTube Subscribe to Making Chips on Apple Podcasts, Google Play, Stitcher, or Spotify

Oct 8, 2019 • 44min
Creating Company Presence through Value-Driven Content Marketing with Chris Fox
Content marketing provides an opportunity to expand your business and to offer something of value to the manufacturing community around the world. Chris Fox, the creative director at MakingChips, shares why every manufacturing leader should be investing in the development of a strong and value-driven content marketing strategy. It’s all about building your online presence as a company and growing your audience. Connect with us:www.MakingChips.com/contact Provide content marketing with value to those that need your expertise Content marketing has grown from only a couple of usable platforms to several powerful mediums for sharing what your business offers - from products to educational knowledge. Blogging, social media, and YouTube are all avenues for content marketing. The goal is to establish the presence of your business and brand, while also meeting the needs of the Metal Working Nation. Chris explains that learning and teaching are things that every machinist and manufacturing leader can benefit from. Every manufacturing business has expertise and wisdom to share with the manufacturing community. Don’t be afraid to begin documenting the story of your company as you create, make mistakes, and overcome obstacles. Your knowledge can easily become rich building material for content marketing! Create authentic content that offers a valuable return on investment Your audience craves and needs original, authentic content to help them accomplish their work at their very best. Being natural in your content marketing is vital. People easily see through facades and glossy content. Be honest and provide real solutions to real problems through your content marketing. If you want your audience to invest their time in watching your videos, reading your blog, or re-tweeting your twitter post, then you need to provide a valuable ROI. Chris encourages listeners to put aside the notion of proprietary secrets. The goal is to grow as a manufacturing community - while also building your reputation as a brand. Value-driven content marketing can help establish your reputation as a trustworthy source for knowledge and product. Vlogging helps establish credibility with your audience Vlogging is blogging in a video format - most often through YouTube. The true value in a blog comes from the individuals in your business. Content marketing doesn’t have to be formal or impressively polished. Being real is vital, and showcasing the talent and knowledge of individual team members can help establish credibility with your audience. Chris explains how to navigate the nuances of vlogging as a manufacturing company. Being honest with the titles of your videos is key. If your title claims to answer a question, make sure that the video actually answers it. Google is now smart enough to read the transcript of your video and match it with the title. If those two factors don’t match up, Google is less likely to promote your video. The length of your videos should be tailored to the needs of your audience. If it takes an hour to demonstrate the solution to a real problem, then your video should be an hour long. If it only takes three minutes, then only create three minutes. Lots of ads and fluff in your videos will turn your audience away and detract from your credibility. Above all, be honest and be concise. Equip and inspire your audience - and your team The value in content marketing is derived from the desire to give without thought of receiving anything in return. Take the time to understand what your customers, partners, and team members need. Know what platforms they use and what types of mediums they are most likely to engage with. While you may not be able to kick off a content marketing strategy that utilizes YouTube, LinkedIn, TikTok, and Facebook all at once, you can certainly start with one. Don’t have expensive camera equipment to film? Use your phone! Bring in the team and refer to their feedback when developing material. Companies aren’t people, but they are made up of people. Make sure that you are providing excellent content by ensuring that you are not only promoting your brand but also equipping and inspiring. Here’s The Good Stuff! Why Jim and Jason see MakingChips as a way to pour back into the Metal Working Nation. Introducing Chris Fox: Creative Director at MakingChips Is all marketing content marketing? The valuable knowledge that manufacturers have to share. Tracking your marketing performance through content marketing platforms. People want value - not excess material. Knowing what platform is best for your company’s needs. Building credibility through vlogging. How important is the title of your vlog video? Showcasing the people in your business - not just your products. Gaging the appropriate length for your video. Learning how to tag your videos. Tools & Takeaways What Is Content Marketing? MakingChips on YouTube Xometry ProShop ERP Text CHIPS to 38470 to subscribe to The Boring Bar This Week’s Superstar Guest: Chris Fox Creative Director at MakingChips Chris on LinkedIn Chris on Twitter Connect With MakingChips www.MakingChips.com On Facebook On LinkedIn On Instagram On Twitter On YouTube Subscribe to Making Chips on Apple Podcasts, Google Play, Stitcher, or Spotify

Oct 1, 2019 • 37min
A Manufacturing Career Could be the Answer for Those Willing to Learn with Sarah Wierman
Choosing a new career path or education route can be intimidating, but a manufacturing career may just provide the perfect solution! Sarah Wierman shares her inspiring story and helpful insights into joining the manufacturing industry and how being willing to learn and ask questions can open up new and exciting opportunities. Be sure to listen to the episode for a unique look into changing career paths and learning the ropes of manufacturing from a beginner’s perspective. Connect with us:www.MakingChips.com/contact From deaf studies to a manufacturing career: Sarah’s story of embracing change Working on obtaining her bachelor’s degree in deaf studies, Sarah tried a job in sign language and teaching but found that she hated it. She decided to take a break from her education and took a job in sales at Raptor Workholding on the recommendation of a friend. Little did she know that she would soon fall in love with the manufacturing industry and find her new passion and calling. The initial appeal in a sales job was the travel opportunities. Sarah soon discovered that manufacturing was more than producing and delivering products. It was creativity and masterful workmanship created to meet an incredibly wide spectrum of needs - from replacing knees to providing building supplies. Inspired, Sarah took it upon herself to learn as much as she could about the industry and asked questions of everyone she met. “I never stopped talking to people,” she shares. Vendor shows and visiting other shops to sell live tooling afforded her plenty of opportunities to deepen her knowledge of machining. Don’t confuse lack of experience with the inability to take action When Sarah first began her job as a sales rep at Raptor, she didn’t even know what a CNC machine was. After a year of intense learning and diving into the new world of manufacturing, she realized that she wanted to stay in the industry long-term. Her eagerness to learn opened new doors, and she took a job as the regional manager at MD Tooling. “Your lack of experience in the industry doesn’t make you ignorant,” she says. “It makes you eager.” If you find that you truly want to be a part of the manufacturing industry, then you need to be willing to take on the responsibility of learning - and learning well. Listen to the episode to learn more about why Sarah fell in love with machining and why she decided to pursue a manufacturing career. Sarah’s positive experience as a woman in the manufacturing industry Even though there are many women in the manufacturing industry, it still isn’t common. Sarah shares her experiences entering into and growing in an industry that is still considered a man’s world. “It is what you make of it,” she says. Even though some of the people she worked with initially found her presence odd, there was never any hostility or opposition. Once her fellow workers discovered that Sarah was willing to learn and put her best foot forward in every job and customer encounter, they embraced her unique perspectives and place within the team. Sarah shares that while it can be intimidating entering a workforce made up almost entirely of men as a young woman, the important thing to focus on is the experience that you are offering customers and your teammates. View obstacles as challenges and find ways to overcome them. It’s about being collaborative and willing to find the solution and solve the problems that arise. Everyone has something unique to offer, and being confident in one’s perspective - while also acting and speaking in humility - will take you farther than you ever thought possible. Use unique avenues to learn something new Learning about a new career opportunity can be daunting. Sarah shares some tips for exploring the manufacturing industry as a new career. Mentors can be invaluable in helping you navigate how to get started, who to talk to, and how to put your best foot forward. Investing in relationships should be a key component of your entire career, but especially when starting out. You will always need others to help you and provide a place for you to seek advice. Never stop asking questions and making room for edifying voices in your life. Social media isn’t just a business marketing tool. It can be a learning tool for exploring new career paths as well! Sarah explains how she began an Instagram page for Raptor Workholding and soon discovered other manufacturing-related pages from which she learned an invaluable amount of insight and skill. Don’t be intimidated by having to learn a new industry. Put yourself out there. Use social media to learn more about the culture and the skills required. Ask questions and make it fun! Manufacturing isn’t just about the products. It’s about the people, meeting the needs of those across the nation and the world, and creating something beautiful out of ordinary hunks of metal. Here’s The Good Stuff! A massive career change led Sarah to discover her true passion. The importance of taking responsibility for your own education. Live tooling allows machinists to take their tooling to the next level. Appreciating the creative side of manufacturing. Being a woman in the manufacturing industry. Recognizing that everyone has a unique perspective. The importance of mentors in launching your career. Using social media as a marketing and learning tool. Being brave enough to step out and ask questions. Tools & Takeaways ProShop ERP Xometry NIMS, Festo Didactic to develop Industry 4.0 skills standards The Boring Bar Newsletter - Text CHIPS to 38470 to subscribe! This Week’s Superstar Guest: Sarah Wierman Sarah on LinkedIn Connect With MakingChips www.MakingChips.com On Facebook On LinkedIn On Instagram On Twitter On YouTube Subscribe to Making Chips on Apple Podcasts, Google Play, Stitcher, or Spotify

Sep 24, 2019 • 58min
Elevating Knowledge through How-To Manufacturing Videos with Mark Terryberry, Bryan O’Fallon, & Scott Gasich
HAAS Automation is leading the way in how-to manufacturing videos as an education tool for manufacturing leaders around the globe - as well as a content marketing tool to demonstrate how to use the newest HAAS equipment. Guest speakers Mark Terryberry, Bryan O’Fallon, and Scott Gasich share their video-making and content marketing expertise in this fascinating episode of MakingChips! Want to learn what makes a great how-to video and how sharing your knowledge can help boost your business? Listen to the episode to find out! Connect with us:www.MakingChips.com/contact Trading manuals for how-to manufacturing videos After a couple of hit how-to YouTube videos demonstrating how to solve simple manufacturing issues, the HAAS Automation marketing team realized that there was no place for manufacturers to go to learn how to do new things or fix things outside of paper manuals. Jumping on the “video craze” bandwagon, they set out to fill the void of immediately available machining instruction by offering quality how-to and product video content. Quickly finding that people prefer short, to-the-point videos, the HAAS team created short video series on different topics. They now average 4-5 videos per week with several series from “Tip of the Day” to “Don’t Fear 5-Axis” and the “Machine Tool Coolant Series.” Manufacturers today need quickly available and accurate demonstrations to help them master their art and easily find solutions. YouTube offers the medium that HAAS needs to accomplish its goal of meeting the needs of the manufacturing community while also marketing their latest products. Overcoming roadblocks with authenticity It can be overwhelming when trying to decide how much production value to put into video content creation. How polished do you make how-to manufacturing videos? Mark, Bryon, and Scott all share the need to be authentic with your audience. Just because you make a video doesn’t mean that people will watch it. Know who you are as a company and know who your customers and potential viewers are. What do they need and want to learn? How-to manufacturing videos are a way to build trust with current and potential customers. If you are providing real solutions to real problems, then you will earn the trust of your viewers. Mark, Bryon, and Scott encourage listeners to use real-life machinists in their video production. The authentic empathy that machinists will have with viewer issues will come through in the videos and provide an added layer of reality and authenticity. Using the needs of viewers as inspiration Listening to your viewers is key! While the manufacturing community may still be pretty old-school, everyone consumes online material, and everyone is looking for answers through mediums such as YouTube. Be sure to read the comments people are leaving in your channel. Provide a phone number and email address so that viewers and customers have a way of reaching out with questions. Use your own company’s mistakes as opportunities for creating new content that demonstrates how to solve the problems you come up against. Making the shift from traditional marketing to content marketing Scott says that with digital marketing, you have to jump right in and get at it. While print marketing may still claim a slice of your resources, put most of your resources in digital marketing. With $3,000 of Facebook marketing, you can reach a million people. With $3,000 invested in print marketing, you may reach a few thousand. Invest in what works. Don’t know where to start? “Follow your gut,” says Scott. Think about how you would want the material presented to you. “Bet on yourself,” he says. Don’t go spend a fortune on production value right away. Use your phone and some good lighting tools and go from there. Build a script or storyboard to help guide the way. Speaking with passion and truth will win the trust of your viewers and help you build your business. Here’s The Good Stuff! MakingChips receives rave reviews on iTunes! The shift from traditional marketing to video content marketing. HAAS Automation as an early adopter of the video craze. Creating a needed learning space for manufacturers. Overcoming the roadblocks of creating new video content. Gleaning material from viewer feedback. Why content marketing is the most effective way to reach your audience. The behind-the-scenes of shooting a YouTube video. Operator Certification through video training series. Augmented reality may be the future of content marketing. Tools & Takeaways Los Angeles is Largest Manufacturing Center in U.S., Government Says ProShop ERP Xometry This Week’s Superstar Guests Mark on LinkedIn Bryan on LinkedIn Scott on LinkedIn HAAS Automation HAAS YouTube Channel Connect With MakingChips www.MakingChips.com On Facebook On LinkedIn On Instagram On Twitter On YouTube Subscribe to Making Chips on Apple Podcasts, Google Play, Stitcher, or Spotify

Sep 17, 2019 • 1h 4min
Closing the Manufacturing Skills Gap by Inspiring the Next Generation with Hernan Ricaurte, Brian Grigson & Brian Pendarvis
How can the Metal Working Nation close the manufacturing skills gap? As the manufacturing industry continues to grow with the demand for fast and excellent production, it is imperative that the proper skills be found, fostered, and taught. Even with the desirable technological sophistication of the modern manufacturing world, young talent isn’t being found quickly enough to fill the gap left by the retirement of the Baby Boomer generation. Jim and Jason brainstorm with guest speakers Hernan Ricaurte (Owner of Ricaurte Precision), Brian Grigson (General Manager of Axxis Corporation), and Brain Pendarvis (Owner of Pendarvis Manufacturing) about how manufacturing leaders can take action to influence the next generation of machinists. Be sure to listen to the entire episode to catch the best insights into the real and persisting problem of the manufacturing skills gap! Connect with us:www.MakingChips.com/contact Putting a finger on the pulse of the manufacturing skills gap Ricaurte, Grigson, and Pendarvis all agree that the skills gap is certainly a major issue of the modern manufacturing world. The “great wave” is here; the older are retiring and the younger aren’t qualified or aren’t interested. Pendarvis shares the struggle of finding talent skilled in the newest manufacturing technology. Leaders know that you can’t just stick anyone on your CNC machines. While the skills gap is a real and present problem, it doesn’t have to remain that way. Changing the perception of manufacturing is the first step. Most high schoolers don’t even know that trade school for CNC machining or similar work is an option. Many still think that they have to go to college to have a meaningful career. Manufacturing, however, offers so much at such little training cost. Building bridges with your community is the first step to closing the skills gap. Give presentations at the local middle and high schools, invite schools to tour your facilities and show them that what they need - and want - in a career can be found in manufacturing. “It’s not always money that people want,” says Grigson. A clean environment, security, incentives, and evident room for company growth are all attributes that can help your business attract young talent. Effective training is grounded in effective culture Who are you as a company? What is your niche? While there is a skills issue, it is important to only hire the skills that you need. What is your company culture? The culture that you want to foster within your business begins with you as the leader. One challenge created by the skills gap is finding someone who is not only talented but also a good fit within your company. Having more experienced employees shadow and oversee the work of new hires or interns provides the opportunity for not only the skills - but for the culture - to be taught. Ricaurte shares the lessons he learned from studying the manufacturing culture of Japanese machinists. Fostering a culture of accountability and excellence if key. Attention to detail, respect for one another, and the willingness to learn are all necessary to an effective workplace Training the younger generation within that culture will help produce the future talent that you need. Don’t forget to listen to the rest of the episode for more insight into fostering effective culture! What makes a great modern machinist? It actually depends on the work and skill-set required! With the advancement of technology, the skill sets needed by manufacturers grows more diverse. While not everyone will be adept in all areas of machining, they always need to be willing to learn and grow. Curiosity is a sign of a great future machinist. While genuine curiosity, humility, excellent work ethic, and personal drive are all hard to detect in an interview, they should be attributes that you are striving to discover. Running an apprenticeship or internship program at your shop is also a highly effective way to discover and nurture new talent. Involve high schoolers in your company’s growth and demonstrate to them the future possibilities within manufacturing. Hiring part-time can also be a good tactic to see if you and your new employee are a good long-term fit. Finding and providing opportunity in unlikely places Your local high school isn’t the only place to find potential future talent to invest in. Underprivileged communities are gold when it comes to finding young people with the passion and drive to try something unconventional - such as attending trade school to learn CNC machining. There are bright, curious minds everywhere! Many kids don’t know that manufacturing is even an option among today’s career paths. Manufacturing leaders need to begin investing in and inspiring the talent and ability of young people. Yes, the manufacturing skills gap is a problem, but it’s not insurmountable. Listen to the full episode to learn more about how you can make a difference in inspiring the next generation of manufacturers! Here’s The Good Stuff! Preparing for the retirement of the Baby Boomer generation. Do the challenges created by the skills gap affect all parts of the country equally? The tie between the skills gap and advancing technology. Knowing your niche gives you vision in knowing what talent to pursue. The challenges surrounding changing the old perception of manufacturing. Different strategies for finding the right fit. What you should be looking for in a potential hire. What you value may differ with each job opening. Creative inspiration for the next generation of manufacturers. Tools & Takeaways 2018 Skills Gap Report NTMA Training Centers ProShop ERP Xometry The Boring Bar newsletter: Text CHIPS to 38470 This Week’s Superstar Guests Hernan Ricaurte on LinkedIn Ricaurte Precision Brian Pendarvis on LinkedIn Pendarvis Manufacturing Brian Grigson on LinkedIn Axxis Corporation Connect With MakingChips www.MakingChips.com On Facebook On LinkedIn On Instagram On Twitter On YouTube Subscribe to Making Chips on Apple Podcasts, Google Play, Stitcher, or Spotify

Sep 10, 2019 • 1h
Thriving as a Manufacturing Entrepreneur with John Saunders
Being a manufacturing leader is difficult, especially if you are a manufacturing entrepreneur! With so many possible opportunities and pitfalls, it can be hard to know how to navigate the small-business world of an entrepreneur. Guest speaker, John Saunders, shares his insight and experience as a leading manufacturing entrepreneur and the ways he has successfully set his business apart and thrived through slow growth. Founder and owner of Saunders Machine Works, John is a serial entrepreneur with his hands in multiple jobs, including running the NYC CNC YouTube channel and overseeing the training and manufacturing sides of his small business. His YouTube channel has become a medium to influence, inspire, and encourage aspiring and seasoned machinists in their careers. Connect with us:www.MakingChips.com/contact Defining the “why” helps drive the business forward Although he attended college to learn entrepreneurship, John found that his key takeaways came from practical experience in selling and machining. Originally wanting to create a business in order to provide a specific product, he quickly realized that creating an excellent product isn’t the same as creating an excellent business. In order to generate a successful business, you have to know the “why” behind the work and the products created. Entrepreneurship isn’t for the faint of heart. John advises that if you are having doubts as to whether or not you really want to work for yourself and jump into the world of paperwork, legality issues, building, training, hiring, producing, and customer service, then you may want to work for someone else for a couple of years. Study how your boss leads and drives their business forward - and then go try it for yourself. John’s business - Saunders Machine Works - grew out of his love for CNC machining and sharing its workhorse capability with viewers on YouTube via his NYC CNC channel. Continuing with the YouTube channel, he wanted a business that could also train individuals in machining and sell manufacturing tools and products. The three-part business has kept up steady - yet slow growth - just as John wants it. Knowing when to jump at an opportunity and when to say NO Keeping a focus on who you are and why you do what you do helps you to navigate the way forward. Instead of chasing every glittering opportunity, consider whether or not it will help fulfill the goals of your business or help create a better experience for your customers. What you are selling isn’t just the object in the box - it’s the atmosphere, relationship, and experience that you are offering your customers. For John, this means finding the best ways to share the modern world of manufacturing with others. His YouTube channel provides a place for machinists of all experience levels to ask questions, easily view videos that demonstrate solutions to popular machining problems, and be a part of the manufacturing community. The training classes that Saunders Machine Works offers provide practical experience in a variety of machining skills and open the door to both young and old to explore manufacturing as a hobby or career. John’s business also values offering internship and apprenticeship-modeled jobs to those who need practical experience through their product manufacturing side of Saunders Machine Works. The goal in sorting through opportunities is to make continuous improvements in your processes - to make them as efficient and streamlined as possible - all without wasting resources. Bootstrapping is the ability of your business to leverage your equity for the greatest return on investment. Money and time are ever manufacturing entrepreneur’s most limited resources. In some phases of your business, you may find that you are lower in one of those resources than another. If you have the opportunity to grow in your knowledge and skills as a master of your trade, take them! Don’t be wasteful. Invest with results. John’s take on managing growth as a manufacturing entrepreneur “Growth eats cash for breakfast,” John warns. We are trained to think that any growth opportunity is a good opportunity, but it’s wiser and more profitable to consider each one through the lens of your “why.” With such a large following, John often gets calls offering partnerships with other businesses. Due to a poor partnership experience in his early entrepreneurial days, John has decided to never partner with another business. The true 50/50 partnership is rare and often difficult to maintain. That doesn’t mean you should never try it, but know where you want your business to go and maintain integrity with those goals through your growth tactics. Be sure to listen to the entire episode for more insight into making the best growth decisions possible. Creating content that reflects your company’s values and meets your customers’ needs It can be easy for entrepreneurs to become overwhelmed by all the marketing and advertising mediums available. John stresses the importance of only utilizing what you need, what you can afford, and what will speak most authentically to your potential customers. John aligns his content creation with his goal to help others help themselves in their manufacturing stories. Be honest about what you are portraying through social media. Authenticity is a huge factor; make it a point to share the stories that surround the challenges that your business has faced and the solutions that you found. Make note of what you are personally drawn to on social media and study why you like it. At the end of the day, it’s not about you. It’s about your current and potential customers and the quality of what you are offering them. Here’s The Good Stuff! Fostering a positive atmosphere among a multigenerational workforce. Guest speaker, John Saunders - owner of Saunders Machine Works. The product isn’t always the business. Knowing how to market yourselves requires a knowledge of who you are as a business. YouTube, training, and machining. What you sell isn’t just the product in the box - it’s the experience you offer. Hands-on experience provides the best education. John’s love of CNC machining and sharing what modern manufacturing looks like. The apprenticeship model of training provides key experiences. Why John says “no” to partnership opportunities. “Growth eats cash for breakfast” - knowing the goal in your growth. Using bootstrapping to reduce wasted resources and to grow where you are at. Good content creation is about knowing your goals and customers. The role of small businesses in the future of manufacturing. “If you’re not making mistakes, you’re not making money.” Tools & Takeaways How To Create a Thriving Workplace Culture podcast episode Small Business, Big Potential The E-Myth Revisited How To Win Friends & Influence People ProShop ERP Xometry This Week’s Superstar Guest: John Saunders John on LinkedIn Saunders Machine Works NYC CNC NYC CNC YouTube Channel Connect With MakingChips www.MakingChips.com On Facebook On LinkedIn On Instagram On Twitter On YouTube Subscribe to Making Chips on Apple Podcasts, Google Play, Stitcher, or Spotify

Aug 28, 2019 • 40min
Machining Trade Schools Offer an Exciting Alternative to Traditional College Educations with Kurt Preisandanz & Lee Norton
With college skyrocketing in price every year, machining trade schools offer an affordable and promising solution to those looking for a meaningful - and even lucrative - career path. Kurt Preisendanz is the Director of Training at the NTMA Training Centers in Southern California. Passionate about sharing the opportunities that machining has to offer the next generation, Kurt explains the challenges that trade schools face and ways that manufacturing leaders can help lead the charge in alternative higher education. Lee Norton is a board member of the California Manufacturing Workforce Foundation, a 501c3 charity that uses their donations to provide tuition and funding to currently enrolled students who are pursuing technical careers. Be sure to listen to this inspiring and insightful episode to learn more about the amazing option of machining trade schools and how you can make a difference. Connect with us:www.MakingChips.com/contact Overcoming the misperception that trade schools aren’t good enough Kurt shares the struggles that he faces when representing the NTMA Training Centers at job fairs and high schools. Many parents and teachers push their children towards universities and traditional college paths because they believe those are the best options available. Trade schools are often looked down upon as not good enough for promising students or as a legitimate gateway into a successful career. Kurt explains that this is mostly an American view, as Europe has long viewed learning and mastering a trade as a proper way to begin a career and life as an adult. Lee shares that while his children are attending university, they have a clear goal in mind. The problem isn’t that the traditional college route is wrong - it’s that it is often wasted and is perceived as the only path to success. That simply isn’t the case. Both Lee and Kurt believe that low trade school attendance and acceptance has to do with the fact that people simply don’t understand the value of what is being taught. The manufacturing world, especially, is still viewed as the dirty factory work that we all want to avoid and escape. Manufacturing, however, has become one of the most modernized and technological industries in the world. The robotics, engineering, building, and software developed and utilized within the manufacturing industry is extremely cutting-edge. The challenge is to overcome the misperceptions surrounding trade schools and machining and to effectively share the opportunity of a machining certification. Machining trade schools offer modern, effective, and exciting opportunities Forget the old days of dirty shop floors and being “doomed” to dangerous factory work. The modern world of machining and manufacturing is filled with incredible technology. Kurt explains that while students in machining trade schools are required to learn all the basics of machining, they are exposed to the many specializations that are available, including robotics, CNC machining, inspection, Master CAM, and CMM. Every one of NTMA’s students learns turning and milling and the fundamentals of machining so that they understand how everything is made. The program can be completed in as little as seven months, with daily hands-on instruction. Students graduate with a certification and are guided and encouraged in their job-finding journey. Many leave with job offers and the promise of an exciting and lucrative future. Enabling and inspiring the next generation of manufacturing leaders to take action Both Kurt and Lee believe that there is light at the end of the tunnel concerning the skills gap in the manufacturing industry. Many are beginning to understand and view a machining career as a valid and exciting opportunity. Kurt ensures that his presentations at job fairs and high schools accurately depict the advanced technological atmosphere that is machining. He shares the diverse culture of the manufacturing world as well. It’s not just men, but women as well, who are finding meaningful work in an industry where their talents are valued. Both young and old are finding new purpose and life in manufacturing. Lee knows that the manufacturing industry is all about giving back. Many who are in the industry grew up in it and have been a part of the Metal Working Nation for generations. Lee and Kurt believe that investing in the next generation of machinists is vital to the health of the industry. Being able to provide scholarships to currently enrolled students in technical fields of study is a huge part of keeping the manufacturing future strong. Be sure to listen to the whole episode for ideas on how you - as a manufacturing leader - can get involved! Guiding students’ expectations towards a stable and meaningful future Kurt explains that many of the students who go to the NTMA training centers are excited about the opportunities ahead. Kurt makes sure, however, that they understand the level of hard work required. No, they aren’t going to make 100k in their first couple of years as machinists, but what they do have to look forward to is a lifelong career built on engaging and purposeful work. They can grow as fast as they want in the industry - there’s no limit to what they can learn and accomplish. They are investing in a career that can offer them a sense of pride in their labor and skillset, opportunities in aerospace and government - all while supplying them with a stable career that will enhance their marriage and family life. It takes work. But what an incredible opportunity! Here’s The Good Stuff! The college price-tag keeps climbing. NTMA Training Centers provide an alternative education route. The California Manufacturing Workforce Foundation enables students to achieve their goals. Why do parents and teachers continue to look down on trade schools? Machining trade schools help close the manufacturing skills gap. Technological advancements in manufacturing are enticing incentives. The diverse and rich culture of the manufacturing industry. Machining trade schools offer a promising and lucrative future. Tools & Takeaways Price of College Increasing Almost 8 Times Faster Than Wages Xometry Design Guides The Boring Bar Newsletter - Text CHIPS to 38470 to subscribe! This Week’s Superstar Guests: Kurt Preisendanz & Lee Norton Kurt on LinkedIn Lee on LinkedIn NTMA Training Center California Manufacturing Workforce Foundation Connect With MakingChips www.MakingChips.com On Facebook On LinkedIn On Instagram On Twitter On YouTube Subscribe to Making Chips on Apple Podcasts, Google Play, Stitcher, or Spotify

Aug 20, 2019 • 36min
Industrial Vending Machines are Optimizing Manufacturing Processes with Steve Pixley
Another amazing form of automation is here - the industrial vending machine! Guest speaker Steve Pixley - Founder & CEO of AutoCrib - dives into why vending machines are the Metal Working Nation’s new best friend on the shop floor. From solving the issue of lost tools and parts to supplying a charging station for electronics, industrial vending machines will help manufacturing leaders take their businesses to the next level of efficiency and safety. Here’s The Good Stuff! Industrial vending machines are projected to rise in popularity. The new way to manage inventory. Steve’s manufacturing story - from sales to automation technology. Solving the issue of stockouts on the shop floor. Helping minimize FOD: Foreign Object Debris. Overcoming the roadblocks to installing an industrial vending machine. From calibrated drill bits to police tasers. Vending machines are simply another type of awesome robot. Tools & Takeaways Xometry ProShop ERP Industrial Vending Machines This Week’s Superstar Guest: Steve Pixley AutoCrib Steve on LinkedIn Connect With MakingChips www.MakingChips.com On Facebook On LinkedIn On Instagram On Twitter On YouTube Subscribe to Making Chips on Apple Podcasts, Google Play, Stitcher, or Spotify