
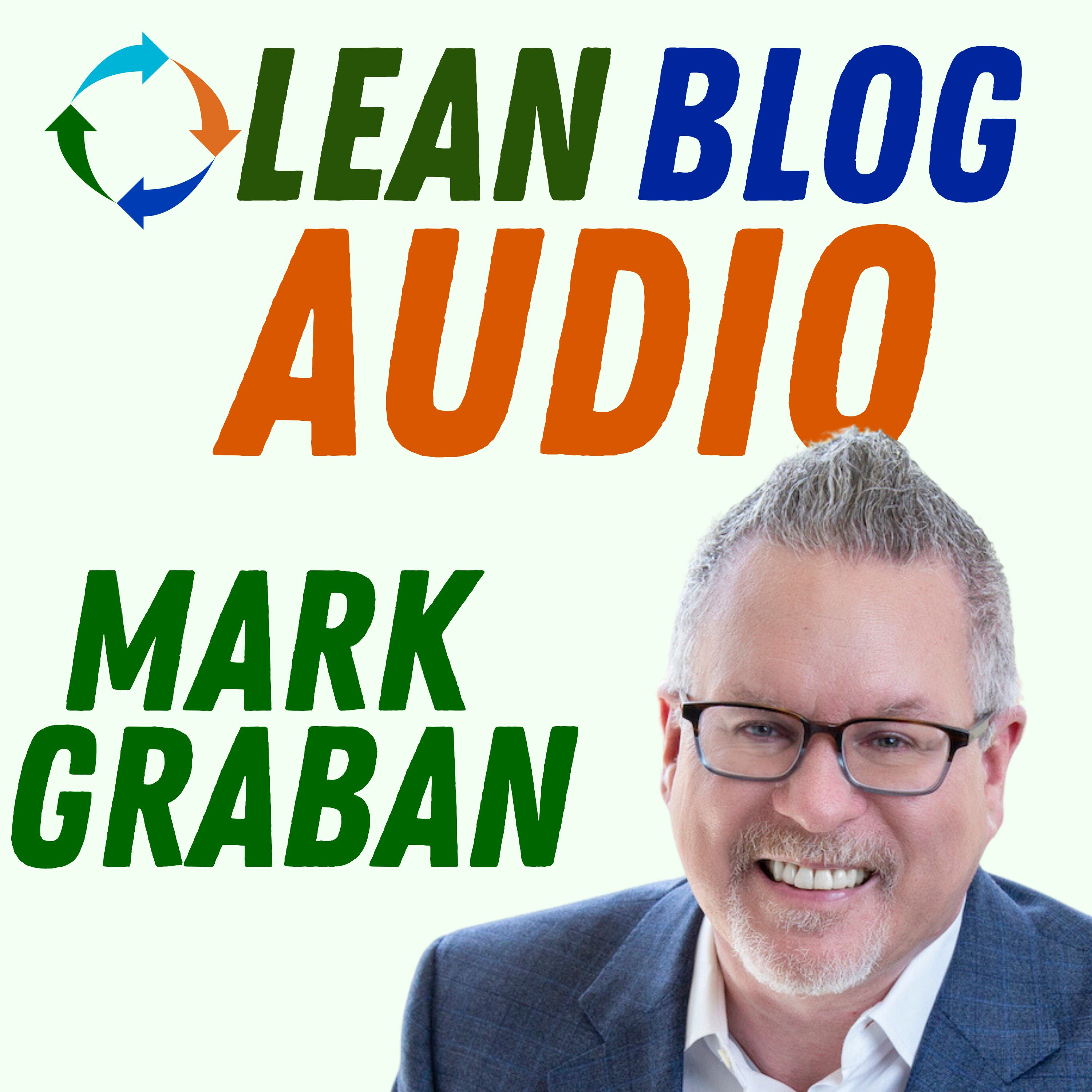
Lean Blog Audio
Mark Graban
Lean Blog Audio features Mark Graban reading and expanding on LeanBlog.org posts. Explore real-world lessons on Lean thinking, psychological safety, continuous improvement, and performance metrics like Process Behavior Charts. Learn how leaders in healthcare, manufacturing, and beyond create cultures of learning, reduce fear, and drive better results.
Listen and learn: leanblog.org/audio
Listen and learn: leanblog.org/audio
Episodes
Mentioned books

Jan 4, 2016 • 4min
Throwback Thursday: Humility is a Rare & Powerful Trait
Humility is an important part of the Lean management philosophy... it also means being willing to admit that there is a problem. Humility means "we don't really know so we must understand and then try many things to see if we have the right solution."

Jan 3, 2016 • 8min
Simple Mixups & How Blaming Workers
When we see a simple error, even in something as silly as sports memorabilia, we would ask "why?" or "how?" instead of "who?" Blaming individuals doesn't help...
http://leanblog.org/audio110

Dec 29, 2015 • 8min
You Can't Force Anyone to Change Their Minds or Actions
When I was at the recent Lean Startup Conference, somebody I know somewhat randomly introduced me to another attendee. As we chatted, I learned her background was social work and she was founder of a technology startup that solves a problem that was important to her and her work. I never met people like that when I worked in manufacturing... again, I've really grown to appreciate the perspectives and experiences of those who have different educational backgrounds than my own.We were talking about healthcare, continuous improvement, and such topics and she suggested that I look into a framework called "motivational interviewing" (MI) as something that might be helpful in my Lean coaching.

Nov 29, 2015 • 10min
You Got Them to Do What? Getting a Hospital to Dedicate
How many times do we hear people say things like“We don’t have time for Lean” or “We don’t have time for Kaizen“? It happens a lot, right? As I’ve said before (and this video) a “lack of time” is a problem to solve... so how did I get hospitals to dedicate staff time for 12 to 16 weeks?
http://leanblog.org/audio108

Nov 18, 2015 • 9min
Maybe We Should Call it "The Many Whys"
The "five" in the "five whys" methodology is not a magic number, be it Lean or Lean Startup approaches.
http://leanblog.org/audio107

Nov 17, 2015 • 10min
You Just Have to Ask Why Five Times?
Why do we need to move beyond "The Five Whys" into a more robust problem solving model for Lean or Lean Startup settings?
http://leanblog.org/audio106

Nov 11, 2015 • 6min
The First Ever Instance of "Lean Doesn't Apply to Us?"
In discussing Lean and working with people in different organizations, I so very often hear things like "we don't build cars" or "we're different." I know I'm not the only one who hears that. The implication is "Lean won't work here, because we're different" in some way. Different country, different industry, different hospital department, different patient or payer mix, etc.

Nov 10, 2015 • 5min
It's Not #Lean to Have Dysfunctional Efficiency Targets
Lean healthcare really is a global movement. Last year, when I went to Japan, we had people in the group from all across Asia, Denmark, Canada, the U.S., and Saudi Arabia. Health systems all around the world need to improve quality and patient safety, reduce waste and create better work environments, reduce waiting times, and get costs under control. These are universal challenges.Thankfully, Lean is helping.
Here's a story from Malaysia that caught my eye: "How assembly lines inspired Asia's hospitals."

Nov 10, 2015 • 4min
Fighting Against "The Way We've Always Done It"
http://leanblog.org/audio103
Through our practice of Lean, we're looking at processes and our management system, looking to identify waste and opportunities for improvement.Lean is about engaging people to have them ask why we do things a certain way or if things could be better (it's not about finding fault from on high and telling them what to do).
The answer to why we (frontline staff or leaders) do something a certain way is often:
"We've always done it that way."
The fact we've always done something that way doesn't automatically mean it's a bad practice. But, we should be willing to challenge things to figure out if we should reinvent that process or tweak it. The same question applies to management practices.

Nov 9, 2015 • 11min
Automakers & Car Dealers Should Survey Customers
http://leanblog.org/audio102
The world (especially the world wide web) is full of surveys. Tell us how we're doing! Your satisfaction is important to us! We see this so often, it's easy to become numb to it in our Yelp-ified world.It's definitely a "first world problem," but I've been shopping for a new car over the past few months and I finally bought something. I won't disclose what I bought, but it's replacing a 2004 Saab 9-3 that I've had for 11 years now.
The car shopping and buying experience has its frustrations - that's nothing new...