
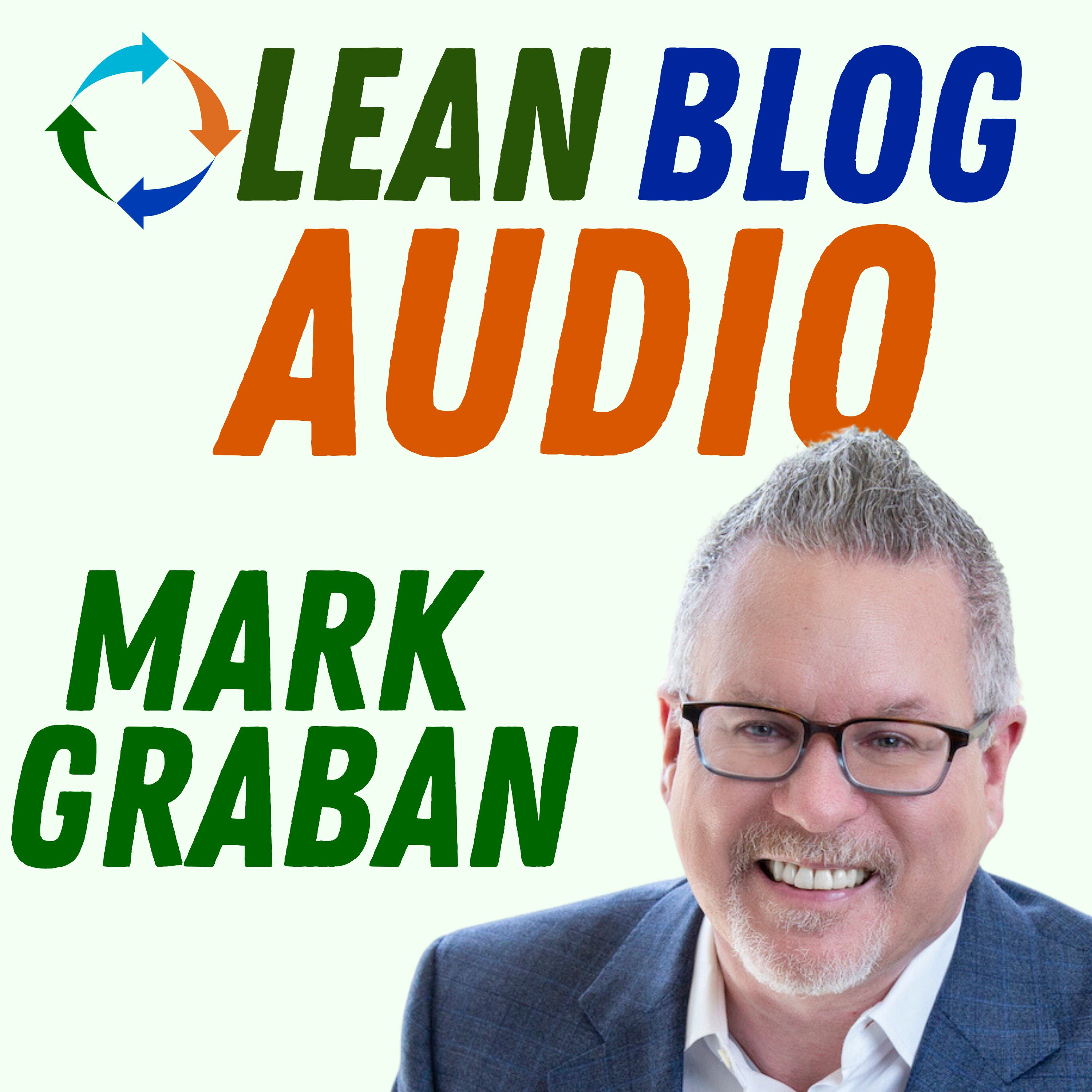
Lean Blog Audio
Mark Graban
Lean Blog Audio features Mark Graban reading and expanding on LeanBlog.org posts. Explore real-world lessons on Lean thinking, psychological safety, continuous improvement, and performance metrics like Process Behavior Charts. Learn how leaders in healthcare, manufacturing, and beyond create cultures of learning, reduce fear, and drive better results.
Listen and learn: leanblog.org/audio
Listen and learn: leanblog.org/audio
Episodes
Mentioned books

May 14, 2025 • 6min
Join Me in Japan: A Lean Healthcare Accelerator Experience This October
Read the blog postSince 2012, I've had the opportunity to visit Japan six times, each trip a deep learning experience–rich with lessons about Lean, Kaizen, leadership, culture, and continuous improvement.This June, I'm heading back for my seventh visit–and what makes this one especially exciting is that it will be my fifth trip focused on Lean in healthcare… and the first that I've helped design from the ground up.It's my first trip in this format, but I was invited to partner up with two amazing individuals who have a great deal of experience in organizing and facilitating such tours — Dave Fitzpatrick, a Canadian who has lived and worked in Japan for a long time, and Reiko Kano, who I know as a translator on my earliest trips — and she's highly experienced with Lean and TPS implementations in healthcare in both the U.S. and Japan.And I want to personally invite you to consider joining us. If not from June 23 to 29, in a later trip. We're also planning on the week of October 26, 2025 along with trips in April and October of 2026.

May 6, 2025 • 6min
Leadership by Fear Doesn’t Work — And Never Really Did
Fear-based leadership is revealed as a misguided approach with detrimental effects. Personal stories from the past illustrate how intimidation fails to yield results. Instead, fostering respect and psychological safety is linked to better team performance. Research supports that belittling employees not only demotivates but also leads to costly errors. Embracing mistakes and creating a supportive environment is the key to true leadership success.

Apr 15, 2025 • 8min
How Psychological Safety Drives Digital Transformation and the Toyota Production System (or Lean)
The blog postBefore I departed for my recent workshop tour of Australia and New Zealand, I knew that I would learn things in the process of teaching and facilitating on my favorite topics. I didn't expect to learn about flying koalas, though!I did expect to learn something when I had the opportunity to meet up for lunch with a friend, former Toyota Australia leader Barry McCarthy. Barry's also the chair of this year's AME International Conference in St. Louis. I first met Barry back in 2018 when I went on a Japan Study trip with Barry and the Honsha Consulting team, and I learned a lot from him on that trip (check out my podcast with him about these topics).Toyota and Psychological Safety–A New BookIn recent years, I've come to believe that Psychological Safety is the oft-unheralded foundation of the Toyota Production System and Lean Management. Former Toyota Kentucky leader Mike Hoseus agrees, as we discussed in this Lean Blog Interviews episode — and as mentioned in the book Toyota Culture, that Mike co-authored with Jeff Liker.I've learned a lot from Barry about Toyota as a “human development company,” as we discussed in his episode.He agrees with me about the direct importance of Psychological Safety at Toyota — and that it's something they intentionally nurture.One new piece of direct evidence of this is a book that was published, in Japanese, back in late 2023. The title can be translated to English as:Two kata that realize psychological safety and speed up work that supports Toyota-style DX: “How to speak” and “How to proceed with work” that resonate with young peopleBarry shared his summary of the book (as translated by him via Google) and I ordered it from Amazon Japan based on his recommendation. When I got home, the book was waiting for me.“DX” is jargon (an abbreviation) for “digital transformation,” something that's increasingly important to Toyota.Back to the title — I suspect that “make work flow better” might be a better translation since we don't normally try to “speed up work” directly through the Lean methodology. Lean is more about reducing and eliminating barriers to flow and not a matter of pressuring people to work faster.The ChatGPT translation of the title says:“Supporting Toyota-Style DX: Two Kata That Achieve Psychological Safety and Speed in Work”“A way of speaking that resonates with young workers” and“A way to move work forward”I've been running pages through ChatGPT as a translation tool. It's incredibly fast. You take a photo of a page (or pages) and out comes the translation. I've been uploading photos in a batch size of “chapter” so ChatGPT can perhaps look at the full context of the chapter instead of only seeing page by page.Before jumping into what Psychological Safety is, the book poses a problem statement:“A diagnostic list for managers–if you mark 3 or more “yes,” you should seriously reconsider your current management style. Examples include:“I've never said ‘thank you' to a team member today.”“I find the word ‘challenge' cringeworthy.”“I haven't talked to anyone outside my own department.”“I tend to suppress my real opinions at work.”I think a good question for leaders is: “Do you remember the last time an employee disagreed with you?” If the answer is “no,” then you have a problem.(1) What is Psychological Safety?“Being able to express honest opinions, candid doubts, and even disagree with others for the sake of organizational or team results–without fear.”— Atsusuke Ishii, 2020, Japanese Management Skills Association

Feb 12, 2025 • 11min
'The Mistakes That Make Us' Receives the Shingo Publication Award!
Blog postI'm very excited to announce that my latest book, The Mistakes That Make Us: Cultivating a Culture of Learning and Innovation, has been officially selected as a recipient of the Shingo Publication Award by the Shingo Institute (the home of the Shingo Prize for organizations).

Feb 7, 2025 • 4min
My Upcoming Webinar on Mistake-Proofing Across Industries
The blog post
I'm excited to be presenting this webinar on February 12th at 1 pm ET as part of the KaiNexus Continuous Improvement webinar series:
The webinar description:
“Are you looking for practical ways to eliminate errors and enhance efficiency in your organization? Join us for “Mistake-Proofing in Action: Real-World Examples Across Industries,” an insightful webinar showcasing how organizations across healthcare, manufacturing, and service sectors have successfully implemented mistake-proofing techniques.
Discover innovative solutions that prevent errors before they occur, improve safety and quality, and save valuable time and resources. Through inspiring case studies and actionable takeaways, you'll learn how to adapt these proven approaches to your unique challenges. Don't miss this chance to gain practical tools and insights to drive continuous improvement and operational excellence.
Register today and see mistake-proofing in action!”
You can also register to win a signed copy of my book, The Mistakes That Make Us: Cultivating a Culture of Learning and Innovation, which has a chapter about preventing mistakes.
Mistake-Proofing in Action: Real-World Examples Across IndustriesEnter to Win!

Feb 6, 2025 • 2min
An Aussie Backpacker’s Workplace Frustration: The Universal Need for Better Leadership
The blog post
Last Sunday, in Frankfurt, Germany, I took part in a guided walking tour of the city.
Our group included a young professional from Australia in his early 20s. He has taken leave from work to travel, backpacking across Europe.
We had an opportunity to chat over lunch and a local “apfelwein” (hard cider). He lamented his frustrations at work.
He said, “My boss thinks he is giving clear direction to us. Then we do the work our best way… only to be criticized for not understanding the direction.”

Jan 21, 2025 • 6min
Safety First: GE Aerospace’s Lynn Facility Demonstrates True Lean Leadership
Episode page
At its core, Lean is about people–respecting them, empowering them, and ensuring their well-being while driving continuous improvement. Recently, GE Aerospace's Lynn, MA, facility provided an inspiring example of what it means to put these principles into action, even under challenging circumstances.
Read more about this and/or watch a video at this link:
Keep the Line Moving: GE Aerospace's Lynn Facility Is Using FLIGHT DECK to Put Safety First

Jan 17, 2025 • 3min
Leadership Gone Wrong: The Cost of Prioritizing a CEO’s Ego Over Effectiveness
Episode blog post
A sad but true leadership tale:
“Unlike most CEOs who rely on their executive team to keep them informed, [redacted] relies on his team to keep him feeling good about himself.
And so whenever somebody would tell him something that he didn't know and make it very clear that he wasn't the smartest person in the room on each and every topic, he generally fired them.”

Jan 6, 2025 • 12min
Starting the New Year with Global Leadership Resolutions: Building a Foundation of Psychological Safety
Read the blog post
During Katie Anderson‘s #JapanStudyTrip this past November, a participant shared an observation with me that resonated deeply:
“The biggest challenge is our blame culture. It's easier for people to do nothing because they don't get in trouble.
But if they make a mistake, they get punished.
And our company is successful enough that there's not a compelling reason for top leaders to change the culture.”
This isn't a story from the U.S., but the feeling is universal.
A workplace culture where individuals are punished for mistakes–especially when those mistakes have systemic causes–is a significant barrier to progress.
It's a global challenge, and addressing it requires rethinking how we approach leadership and learning.

Dec 10, 2024 • 6min
Lost My iPhone in Tokyo: A Lesson in Japanese Kindness and Culture on My Japan Study Trip
Read the blog post: https://www.leanblog.org/2024/11/lost-iphone-japan-taxi-tokyo-kindness-culture/
I'm thrilled to be back in Japan for the first time in five years. Today is the start of Katie Anderson's Japan Study Trip (learn more about joining her in May 2025). It's great to be here for another week of learning and great experiences.
Little did I know, I'd kick off the trip by nearly losing my iPhone on the streets of Tokyo–a mistake that ended up teaching me a valuable lesson about Japan's culture of trust.