
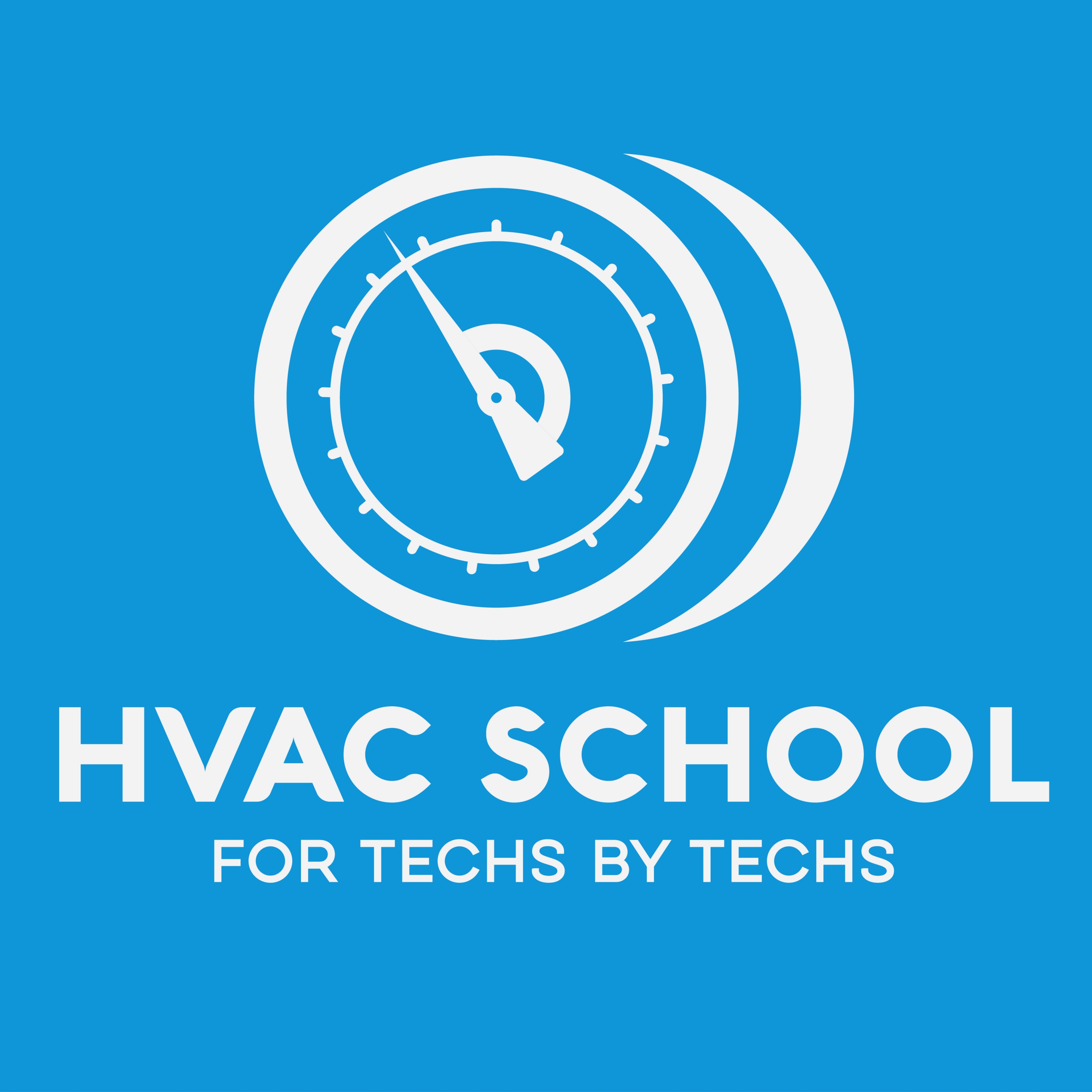
HVAC School - For Techs, By Techs
Bryan Orr
Real training for HVAC ( Heating, Ventilation, Air Conditioning and Refrigeration) Technicians. Including recorded tech training, interviews, diagnostics and general conversations about the trade.
Episodes
Mentioned books

Jan 9, 2020 • 33min
R290 Facts and Service w/ True Refrigeration
Alejandro Rios from True Refrigeration comes on to talk about self-contained R290. He explains what it is, why to love it, and how to service the sealed system. R290 is pure propane, and it has recently made a name for itself as an emerging refrigerant. It is an A3 refrigerant, meaning that it is non-toxic and highly flammable. As we move away from HFCs and other refrigerants with high global warming potential (GWP), we will encounter more flammable refrigerants, usually A2L and A3 refrigerants. R290 is a natural refrigerant and has a GWP of only 3, making it more attractive than 400-series blends and some A2L refrigerants. You can also vent R290 because it has such a low GWP and an ozone-depleting potential (ODP) of 0. Self-contained systems that use R290 have a relatively small charge. However, they effectively run colder coils. Due to the colder coils, these systems have a net refrigeration effect (NRE) about 30% better than previous equipment models with other refrigerants. R290 is also versatile and can work in medium and low-temp refrigeration. Many of the service procedures are quite similar to other refrigeration systems. However, you have to be EXTRA diligent to check for flammable gas leaks; you must use a combustible gas meter for leak detection, NOT your typical electronic leak detector. Like most self-contained equipment, True's equipment is factory-sealed, and you must braze in your own service ports. However, as long as you vent the refrigerant in open areas and purge the line with nitrogen, you normally don't need to worry about anything catching fire. Alejandro and Bryan also discuss: Regulations for self-contained systems Terminal venting High-efficiency R410A systems Small charges Residual refrigerant and evacuation Adding service ports and sealing them Refrigerant recovery with SHORT hoses POE oil Energy savings Check out True's YouTube channel HERE. Learn more about Refrigeration Technologies HERE. If you have an iPhone, subscribe to the podcast HERE, and if you have an Android phone, subscribe HERE.

Jan 7, 2020 • 13min
Short #85 - Low Voltage, Low Voltage
In this short podcast episode, Bryan explains what happens when your low-voltage circuit puts out a lower voltage than it should. Bryan recently received an email asking about the low voltage on a 20-ton split system with a long control wire; the voltage coming back to the condenser is only 19 volts, so there was some contactor chattering. First, in a case like that, you'll want to figure out why the voltage isn't as high as it should be. The control wire and line sets could be longer than the design specs, which may contribute to the problem. If the distance between components is the main issue, then you can use a relay to mitigate voltage drop and amp draw. You'll also want to check that you've tapped the transformer correctly. Since most transformers are single-phase, they'll probably start off tapped to 240v; when you're dealing with three-phase equipment, you must ensure that the transformer is tapped to 208v. One of the obvious issues to check is the voltage drop. If 26 volts are coming out of the transformer but you're only measuring 19, then you're clearly losing volts and have some resistance. Think about ALL of the conductors; is the drop the same across all of them? If so, then you've likely got a length and wire sizing problem. You can correct that issue with proper wire sizing; you can't always control the length, but if you can, then it's a good issue to address. If there's an issue with only one conductor, then the switch could have a problem, or there might be some wire splices. If the load is drawing higher current than it should, then something could be impeding the motion on the solenoid, contactor, or another electrical component. Learn more about Refrigeration Technologies HERE. If you have an iPhone, subscribe to the podcast HERE, and if you have an Android phone, subscribe HERE.

Jan 2, 2020 • 50min
Codes and Failed Inspections #LIVE
In this live podcast from the Castbox app, we talk about codes and common causes for failed inspections. We talk about these topics both broadly and with some specifics. Many of the places where we fail to meet codes are on the electrical side. Electrical components have fire and electrical shock hazards, and codes are stringent for arc and ground fault protection. Leaking current to ground can shock someone, and arcs can cause damage to property and human life. We commonly see failed inspections due to improper marking on the air handler. In the HVAC industry, we have specific wire and breaker-sizing codes for our trade (440 in the NEC). Inspection failures are common in this area, as it's easy to leave the incorrect breaker in place. You also must have a disconnect or easily accessible circuit breaker that can function as a disconnect. In our market, we must also insulate drains and show proper attention to strapping, pitch, float switches, and cleanouts; otherwise, the drains may fail inspection (though it's rare). Clearances also come up quite often and are especially relevant to safety in our industry, as we don't want condensers blocking panels. Obstructed rooms or lack of egress are also common code violations related to safety. Anchorage is another safety-related code category, and there are special requirements in locations that are prone to high winds (like Florida) or earthquakes (California). You can't assume that units installed on rooftops have been anchored correctly, so be sure to check the anchorage. We also discuss: Pulling permits CO detectors PVC primer on condensate drains National Electrical Code (NEC) vs. AHJ Catwalks in attics Duct sealing and mastic vs. metal tape Florida Energy Conservation, Mechanical, and Building Codes Customer complaints Furnace venting and GAMA tables Smoke detectors Locking caps Wire protection Sealing boots Learn more about Refrigeration Technologies HERE. If you have an iPhone, subscribe to the podcast HERE, and if you have an Android phone, subscribe HERE.

Dec 20, 2019 • 55min
FURNACE TALK #LIVE
In this live podcast episode from the Castbox app, we have four techs join us to talk about common furnace issues and best practices. Those of us in heat-pump-dominant markets rarely have to worry about common furnace issues related to gas pressure and flow. In that same vein, we also don't have to worry about clocking the gas meter, which is a common practice on gas furnaces. Checking input and performing combustion analysis is critical to the diagnostic process AND can give you an idea of the unit's safety. There is no reason NOT to do combustion analysis when commissioning a furnace. Furnaces also have electrical components with flashing error codes. You must be careful when interpreting those codes, as multiple issues could show up under one code. (Compare it to going out on high pressure; that error doesn't necessarily indicate a pressure switch issue and could entail other problems.) Common codes deal with the flame sensor, but flame sensor failure is rare; the issue could come down to simple maintenance. When cleaning parts, the most important thing to do is make sure the carbon and debris come off; you don't have to overthink the cleaning material. Cracked heat exchangers are common issues that can present unsafe conditions, though they won't always have CO problems. If there is an issue with a cracked heat exchanger, the technician usually CANNOT turn off the system at the gas. (We usually CAN shut off the power at the switch, though.) Only the gas company can typically shut off the gas. We also discuss: Restrictions at ports Adjustments for altitude Carbon monoxide poisoning Proper drain line Clocking the gas meter in commercial settings Gas pool heater problems Parts that commonly need cleaning Steel wool vs. sand cloth High limit codes Clogged burner wings CO-monitoring Venting issues and negative pressurization Intake/exhaust pipe issues Power passing vs. consuming Learn more about Refrigeration Technologies HERE. If you have an iPhone, subscribe to the podcast HERE, and if you have an Android phone, subscribe HERE.

Dec 19, 2019 • 34min
Mixed Air Temperature w/ David Richardson
David Richardson with NCI, author of Duct Dynasty, joins us on the podcast to talk about mixed air temperature and more topics of interest. When you bring outside air into the home, you introduce positive pressure into the home. That way, you can offset air lost via mechanical ventilation or through cracks, improving air quality. We often assume that the building will "breathe," but tighter constructions make it difficult for the home to bring in enough fresh air to offset harmful chemicals and VOCs. We need to measure two different kinds of airflow: fan airflow and outside air. When we have these numbers, we must figure out how much air is coming through the outside air intake. The fan airflow represents 100% of the air content after mixing has taken place. You can perform a duct traverse to get the airflow measurement; when you plot the fan airflow, subtract the two to know how much return air you're getting BEFORE mixing with the outside air. Once you have your airflow measurements, you must break those into percentages. You must determine the percentage that matches up with the temperature you want to use for the mixed air. Subtract the outside air from the fan airflow to get the CFM from your baseline. You could get 95% of your airflow from the return and 5% from the outside. Once you know the outside air temperature and the percentage of outside air, you will know how much the outdoor temperature will affect the return air and space temperatures. David and Bryan also discuss: How David got into writing Blown-in cellulose insulation Designed and undesigned leakage Duct traverse tools and procedure Dry-bulb vs. wet-bulb measurement applications SEER vs. AFUE Duct leakage Learn more about NCI at nationalcomfortinstitute.com. Learn more about Refrigeration Technologies HERE. If you have an iPhone, subscribe to the podcast HERE, and if you have an Android phone, subscribe HERE.

Dec 17, 2019 • 15min
Short #84 - Power Passing vs. Consuming
In this short podcast, Bryan briefly explains why we use a voltmeter to measure “voltage drop” across loads and switches. He also covers some of the differences between passing and consuming power. Many of us are naturals at using voltmeters already. Voltmeters have two leads, and those exist to measure the difference or potential between them. Voltage is a reference to what is going on between the leads; whenever resistance exists, we have a voltage drop. Resistance can sometimes be designed or undesigned. When we think about power passing and consuming, we should note that "consuming" refers to turning energy from a usable form to an unusable one. Stored energy becomes potential energy when it needs to do work. Power consuming results in work; a coil in a contactor or a filament in a lightbulb is a load (the load has resistance). On the other hand, power-passing components do not have resistance, and the charges merely move. We must keep the intended resistance in mind whenever we measure the voltage of energized components; resistance will impact the voltage drop. If you have a high-limit furnace safety, you will want to measure the voltage drop across the limit. There should NOT be a voltage drop across it because it is a power-passing component; there should be no resistance. Of course, you must determine if there is an energy potential present in the first place. Conversely, you SHOULD see a voltage drop when measuring the potential across a heater or fan motor. Overall, wires and switches are power passing components that should not have voltage drops across them. Heaters, compressors, and fan motors are all loads that "consume" power. Learn more about Refrigeration Technologies HERE. If you have an iPhone, subscribe to the podcast HERE, and if you have an Android phone, subscribe HERE.

Dec 12, 2019 • 52min
Impactful HVAC/R Instruction
Ty Branaman from NTI comes on the podcast to share his passion for teaching. He also discusses his approach to impactful HVAC/R instruction. It can be difficult for instructors to create an appropriate balance between teaching theory and practical knowledge. Students and trainees need to have technical skills in the field, but they also need a solid foundation. Impactful HVAC/R instruction requires a balance of the nerdy stuff and physical skills; good instructors put the theoretical parts simply and give students the opportunity to apply theory to hands-on skills. Engagement is another important part of HVAC/R education. If students are sitting down for 15 minutes, that's too long; the students need to be moving and active with the learning material to stay engaged and help the topics stick. Ty emphasizes the importance of spending time in the lab instead of staying in the classroom the entire time. Unfortunately, many trade schools nowadays don't prepare students for fieldwork because there is not enough emphasis on working with equipment in education programs. The best teachers are those who love teaching AND working in the field, and trade schools need more people who are passionate about BOTH. Passionate technicians need to get involved in education by offering to be a substitute or guest speaker or by joining an education advisory board. Ty and Bryan also discuss: Teaching the refrigeration cycle What the current generation values and needs in education Dealing with distractions in the classroom Using mobile apps to supplement learning Teaching newbies effectively Creating an HVAC/R instruction program on a budget Old equipment Getting involved in education How to guide young people in their careers "Thinking outside the box" Check out Ty's YouTube Channel HERE. Learn more about Refrigeration Technologies HERE. If you have an iPhone, subscribe to the podcast HERE, and if you have an Android phone, subscribe HERE.

Dec 10, 2019 • 15min
Short #83 - Practical Safety Improvements
In this short podcast, we take a quick look at Bryan’s take on practical safety improvements. He also discusses the safety year in review at Kalos. Kalos had a great year in terms of safety. As the managers look back on the year, they attribute their success to having a practical approach to safety. To make practical safety improvements, we must be safety-conscious without obsessing over the risks of our job. Our jobs always have an element of danger, and our goal should be to minimize those and abide by OSHA standards. As an industry, we can do a better job of wearing our eye protection on almost every job. Ear protection is also an area we tend to neglect, especially in motor rooms and industrial environments. Ladders also provide a clear source of danger; we need to make sure our ladders are secure (tied off, set on level ground, etc.) and place some responsibility on our customers to give us a safe work environment. Electrical safety is also critical. Especially on commercial jobs, we should use proper lockout-tagout procedures when we can't monitor the power source while we work on equipment. We must also verify that no power is present after we shut off the disconnects. We also experience some fire safety threats, especially while brazing. Eye protection and gloves are critical if you want to keep yourself safe while brazing. (Gloves are also important when cutting sheet metal.) You should also know where fire extinguishers are anytime there is a fire risk on the job. Perhaps our most dangerous work environment is the road. We must avoid texting while driving, drunk driving, and other unsafe practices. We must also drive defensively to avoid accidents with other commuters who partake in unsafe driving practices. Learn more about Refrigeration Technologies HERE. If you have an iPhone, subscribe to the podcast HERE, and if you have an Android phone, subscribe HERE.

Dec 5, 2019 • 56min
Descaling Large Equipment
Tim Fregeau from Goodway joins us to talk about descaling large equipment. He also discusses best practices and why they matter to you. Scale refers to mineral deposits that build up in any water source. Water can be brackish, rusty, muddy, or otherwise high in mineral content, and those minerals begin to accumulate on heat-transfer surfaces on large equipment. Scale can cause metallic components to weaken and leak, and it can block microchannel coils. The large equipment can't reject the heat efficiently or function as it should when it has scale buildup, so that's where descaling comes in. When it comes to chillers, you can either brush or chemically clean the tubes to remove scale. There will be times when you physically cannot brush the tubes, so you must rely on chemicals to descale the equipment. When you use chemicals, you pump the chemical solution into a low point of the condenser and make it come out of a high point. Factors that influence success are the chemical makeup, flow rate, and pump size. Boilers are quite similar to chillers, but the higher water temperatures come into play. Various chemical agents have different functions. Acids dissolve calcium, and inhibitors protect the base metals. Wetting agents reduce the surface tension and allow the chemicals to spread out. Penetrating agents allow the chemicals to get deeper into the mineral deposit to dissolve calcium and free up the rest of the deposit. Tim and Bryan also discuss: Plate heat exchangers Separating open loops from chillers Goodway clean-in-place systems Chemical selection and dilution Circulation time Why track oil levels and approach temperatures? Compression ratio and system efficiency Common cleaning challenges and mistakes to avoid Water pH Calcium spot tests Goodway products Legionella Check out Goodway's site HERE. If you have an iPhone, subscribe to the podcast HERE, and if you have an Android phone, subscribe HERE.

Dec 3, 2019 • 12min
Short #82 - Brazing Temperature
In this short podcast episode, Bryan talks a bit about brazing temperature. He also covers how to heat your copper to the proper temperature. You can use torches with oxyacetylene or air-acetylene tips. Joining two metals with an alloy above 840 degrees classifies as brazing; anything that uses an alloy to join two metals below 840 degrees is technically soldering. When you join two similar metals by melting the base material (not using an alloy), that's welding. Another temperature of interest is 500 degrees; oxygen rapidly bonds to copper at temperatures above 500 degrees, so we will want to flow nitrogen while brazing to prevent cupric oxide (black scale) from forming on the copper. (We always recommend flowing nitrogen even if you are soldering below 500 degrees.) When brazing with a 15% silver alloy (with a phosphorus fluxing agent), you will want to reach a temperature of 1100-1200 degrees. Solidus is when the rod gets a putty-like consistency. However, we want liquidus, which is when the alloy can flow freely into the joint. The color of the copper will be either dark or medium cherry. To be clear, you DO want to see redness when brazing; the color shouldn't be very bright red or orange, but a dark or medium red is ideal. The brazing indicators hold true for copper-to-steel and copper-to-grass brazing as well. Aluminum brazing should stay below 1200 degrees; aluminum also doesn't have the same color indicators as copper, steel, and brass. Steel is complicated because it has a lower melting temperature, but it has much lower thermal conductivity than steel, so it will take longer to heat up and may heat unevenly. You also CANNOT use an alloy with a phosphorus fluxing agent when brazing steel or brass; you need a silver alloy with a separate flux. Learn more about Refrigeration Technologies HERE. If you have an iPhone, subscribe to the podcast HERE, and if you have an Android phone, subscribe HERE.